What is a flow chart?
A flow chart, often referred to as a flow diagram, is a technical drawing that shows the structure and functioning of processes, systems or plants in a schematic form. Such diagrams are of central importance in plant and process engineering because they visualize the course and relationships within a system, process or plant. In a flow chart, the movements of materials, energy, information, or other resources through various process stages and components are shown in a comprehensible manner.
Flow charts provide a simple, abstract presentation of process processes defined by specific standards, such as EN ISO 10628. In Germany, for example, DIN EN ISO 10628 is considered a standard standard. The precise regulation of such standards ensures comprehensible and uniform documentation throughout all phases of the plant life cycle.
Different types of flow charts
Flow charts are available in different versions, each covering different levels of detail and objectives. These types of diagrams range from simple overviews to very detailed representations for technical operation and maintenance. Choosing the right flow diagram is crucial to meeting the target group's information needs.
Basic flow chart
The basic flow chart, often also known as a block flow diagram, represents the simplest type of flow diagram and is limited to the basic structure of a process. It is therefore particularly relevant for pre-engineering. It uses blocks and connecting lines to represent the individual process steps as well as input and output materials.
As a rule, only the essentials are shown here, without going into the details of the technology or equipment. For basic information, the main substances and energies are named, sometimes supplemented by information on flows, operating conditions such as temperature or pressure, or important properties of the starting materials. This reduced presentation is particularly suitable in early project phases or for a general process overview.
Block flow chart
The block flowsheet is similar to the basic flowsheet and is often used as a synonym, but usually represents a more detailed level. Here, the blocks symbolize important steps or operations in the process, such as reactors, evaporators or pumps, and are connected by lines that indicate the flow of substances or energy.
This flow chart is also intended for a general overview and is particularly useful in strategic planning and for communication with investors or decision makers.
Process flow chart
The process flow chart (PFD) goes one level deeper than the block and basic flow chart and is therefore relevant for basic engineering. In addition to the main plant components and machines, it also shows the most important process flows and their flows, including key operating parameters such as temperature, pressure or flow. The graphical symbols represent the various devices and machines in the process and are provided with specific abbreviations that provide additional technical information.
This type of flow diagram is particularly valuable in technical plant operation and in process planning, as it provides a more comprehensive description of the process. The process flow chart also forms the basis for communication between the technical departments of a company.
Pipeline and instrument flow chart (P&I flow diagram)
The pipeline and instrument flow chart (P&ID), represents the most detailed form of a flow diagram. It is therefore particularly interesting for detailed engineering. It is based on the process flow diagram, but expands it to include an exact representation of the connection between the lines and instruments. Here, all cables, instruments, control and connection types are specified and marked in accordance with standards. The symbols are standardized and show pipeline sizes, connections (e.g. flange connections) and any necessary insulation. For planning and installation, the geometric shape and height differences of the pipes are also shown.
The P&I flow diagram is essential for the precise planning and installation of pipeline systems and serves as the main document for instrumenting and controlling the plant. It also takes into account the requirements for process control technology and shows the operating principles of all control devices, which is particularly important for maintenance and repair.
Process parameters such as pressure or temperature are often not shown in the P&I flow diagram, as these are not relevant to operating personnel. For this purpose, there are detailed markings for pipe classes, media and dimensions. Standards such as DIN EN ISO 10628-1 and ISO 10628-2 define the exact representations and symbolism, which ensures clear comprehensibility even for technical service providers.
Choose the right flow chart type
The choice of the appropriate flow diagram depends largely on the target group and the project stage. Each scheme provides specific information based on different interests:
- The basic or block flow diagram is sufficient for a general process overview. Here, complex process structures are presented in a simplified form so that even those not familiar with the subject can quickly gain an insight into the process. This is particularly important for strategic planning and in early project phases, when the main focus is on a rough idea of a project.
- The process flow chart is useful for detailed planning and analysis of a process. It offers a more comprehensive representation and is aimed at specialist departments such as process engineers who want to carry out technical optimization, dimensioning or analysis. System components are specified here and the most important process parameters are included, making the diagram ideal for in-depth technical coordination.
- The P&I flow diagram is essential for detailed planning, installation and operation. This diagram is indispensable for the construction and installation phases as well as subsequent system operation, as it shows all lines, instruments and connections in detail. It enables precise planning of the necessary equipment and serves as a reference for maintenance and repairs. This diagram is particularly important when handing over to the maintenance teams or external service providers, as it contains all the necessary details for control and regulation.
For the successful implementation of a process engineering project, it is crucial to correctly select the flow diagram type and adapt it to the respective target groups. This is the only way to ensure that the relevant information is available at the right time and for the right experts.
Relevance — What are flow charts useful for?
Calculation and offer precision
Flow charts play a decisive role in calculating and preparing offers. P&I flow diagrams in particular make it possible to derive precise parts lists directly from the flow diagram. These are often available in a format appropriate to the format and can be seamlessly integrated into spreadsheet programs. This not only makes it easier to create detailed calculations, but also significantly increases accuracy and efficiency in the quotation process.
High level of detail and adaptability
A flow chart allows attributes to be added for specific details, such as pressure levels, sizes, materials, pipe contents, capacities, and temperatures. These attributes can be displayed both visibly and invisibly and can be included in the parts lists. This allows very precise planning to be carried out, which at the same time requires no additional documents. Modern P&I systems offer the option of flexibly specifying such attributes or assigning them to standardized specifications. This results in a comprehensive presentation that requires no additional documentation, which increases the consistency and accessibility of information.
Optimizing process efficiency
Flow charts make complex processes visible in an understandable way and help to identify potential bottlenecks or inefficient process stages at an early stage. Visualization increases efficiency, as problematic process points are immediately identified and can be optimized in a targeted manner.
Avoiding errors through visual planning
A detailed flow chart significantly reduces the likelihood of errors in the planning process. By visually presenting critical elements and their links, potential sources of error can be identified and resolved at an early stage. This reduces the risk of errors later on in the project, which is a major advantage, especially with complex systems.
Training and maintenance documentation
Flow charts serve as valuable documentation that can be used in many phases of a project — from training to maintenance to safety inspection. They provide a clear overview of the process, which is helpful for employee training as well as for inspections. This ensures that all parties involved can access the same information at all times, which contributes to higher safety and quality standards.
Communication base for departments
A flow chart is a common communication basis for various departments such as production, engineering and management. It supports consistent coordination and exchange between these teams by providing a clear picture of the process structure. This makes it easier to discuss complex processes and avoid misunderstandings, which improves collaboration and coordination.
Components of a flow chart
Symbols in accordance with ISO 10628-2
The basis of flow charts are standardized symbols, which are regulated by ISO 10628-2. These symbols represent various devices and process components, such as pumps, valves, heat exchangers, and reactors. Symbols simplify the presentation of complex system elements so that their function and position in the process is easy to understand. Frequently recurring elements such as pumps, containers or compressors are therefore represented by clear, easy-to-understand symbols in order to maximize clarity.
Key symbol categories include:
- Devices: Machinery and equipment such as compressors, motors, turbines and vacuum pumps.
- Piping: Connections and lines that ensure flow and connections between plants.
- Receptacles: Storage units such as tanks and silos, which store liquids and, if necessary, influence their properties.
- Heat exchanger: Equipment for efficient transfer of heat, e.g. boilers and condensers.
- Pumps: Devices to increase or regulate the pressure of liquids.
- Instruments: Measurement and control devices for monitoring parameters such as temperature, pressure and flow.
- Valves: Controls for the flow of liquids in pipeline systems, such as ball valves or shut-off valves.
These symbol standards are not only important for planning and construction, but also for the uniform interpretation and documentation of process systems.
Connections and lines
Flow charts show the course and direction of the flow between the components using lines and arrows. These connections define the flow direction and link individual process steps. Pipes and lines play an important role here and are essential for connecting the individual machines and devices together.
In industrial processes, the pipes are used in various materials and shapes, adapted to the respective requirements and the medium being carried out. For example, special materials are selected for liquids, gases or vacuum applications. In the flow diagram, the link between the systems is made visible so that the flow and sequence of the process steps are clearly comprehensible.
Captions and notes
For complete comprehension, it is important that symbols and lines are supplemented with labels. These contain additional information such as temperatures, pressure values, flow rates and material properties. Labeling thus makes the meaning of the symbols and connections easier to understand and is a helpful guide for engineers and technicians working in plant operation or maintenance. Notes and special comments in the margins of the flow chart also provide important process details and requirements that are essential for the process or safety standards of the plant.
Process steps
The arrangement of the symbols and lines in the flow diagram reflects the sequence of process steps. Each step of the production process is visualized by placing and linking the symbols so that the entire process chain and the steps it contains can be understood at a glance. This makes the flow chart an indispensable tool for planning and optimising process flows by structuring and presenting the processes within the plant in an easy-to-understand manner.
Create a flow chart
In order to create a flow diagram efficiently and without errors, specific software tools are helpful, which both support planning and drawing and minimize errors during creation.
Software — Tools for creating flowcharts
Modern software solutions offer various approaches to creating and managing flow charts. In the past, flow charts were often created manually, which was time-consuming and had potential sources of error. The software that you can use today is essentially divided into CAD programs (computer-aided design) and specialized process flow diagram software.
- CAD software Like AutoCAD, it allows you to create precise and true-to-scale flow schemes. CAD tools offer extensive drawing functions that give you a high degree of flexibility. Many CAD systems have libraries for frequently used symbols and standardized components, which speeds up the process and reduces errors. We too rely on AutoCAD Plant 3D to create our flow charts.
- Specialized process flow diagram software: Some programs are specifically designed to meet the requirements of flow diagram creation. These software solutions offer you the opportunity to clearly plan the entire structure of a flow diagram. It is particularly valuable that these programs comply with consistent standards and provide the database with supported symbols and components. In this way, the flow diagram remains uniform and automation reduces the risk of errors.
Avoid creation errors
A major advantage of this specialized software is the built-in consistency check. As you create the flow chart, the software automatically checks the accuracy and consistency of the entries. The programs highlight potential faults, identify the respective problem and suggest solutions if necessary. In this way, errors can be identified and corrected directly in the work process before they affect further planning phases. The most common sources of error that you should avoid are:
- Inconsistent icon usage: A common mistake is using inconsistent symbols for the same components. Pay attention to the standardization of the symbols in your flow diagram and comply with current standards.
- Missing or incorrect labels: Accurate and uniform labeling of components is crucial. This applies to all pipes, instruments and fittings. The software can often help here by notifying you of missing information.
- Incorrectly sized or disconnected connections: A typical problem caused by manual errors is incorrectly dimensioned connections or incorrectly connected pipes and instruments. Good software recognizes such errors and marks them for you so that you can correct them directly.
- Inadequate consistency check for connections and devices: Sometimes connections between components in the system cannot be correctly mapped. An automatic consistency check ensures that all connections are created correctly.
Areas of application of flow charts
Chemical and petrochemical industry
In the chemical and petrochemical industries, flow charts are used to visualize and optimize complex manufacturing processes for chemical products and petroleum products. They help to represent the sequence of chemical reactions and physical processes required to produce chemicals, plastics, and fuels. Flow charts support the planning, monitoring and maintenance of systems to ensure that they work safely and efficiently and that potential hazards can be identified at an early stage.
Especially in large industrial processes, where large quantities of raw materials are processed, flow charts make it easier to understand and analyze the material flows as well as to comply with legal regulations and safety standards.
Pharmaceutical industry
In the pharmaceutical industry, manufacturing drugs is a strictly controlled process that requires precise control and documentation. Flow charts are essential here to plan and document the production process, which ensures consistent quality and effectiveness of pharmaceutical products.
Flow charts help to transparently represent all processing steps — from raw material preparation to synthesis and purification to final packaging — and thus make it easier to comply with regulatory requirements, such as Good Manufacturing Practice (GMP). When automating processes and in quality control, flow charts are also an indispensable tool to ensure process efficiency and product safety.
Food and beverage industry
In the food and beverage industry, flow charts help to represent and control production processes to ensure consistently high quality standards. They are used, among other things, in the production and processing of beverages, baked goods, dairy products and canned goods.
Flow charts show how raw materials are prepared, processed and packaged and provide a clear overview of all relevant process steps. In this industry, flow charts support compliance with hygiene standards, traceability of production, and prevention of contamination. They also provide a basis for improvements in terms of efficiency and sustainability and help to use resources, such as water and energy, in a targeted and economical manner.
Water management and sewage management
In water management and wastewater management, flow charts enable detailed presentation and control of water treatment and wastewater treatment processes. Here, all steps — from raw water extraction to treatment and purification to distribution or disposal — are mapped.
In sewage treatment plants in particular, a precise description of the process steps is necessary to ensure compliance with environmental protection requirements and to ensure trouble-free operation of the plants. Flow charts also help with planning maintenance work and monitoring parameter changes that indicate potential faults or optimization opportunities. In this way, flow diagrams help to efficiently manage water resources and minimize environmental impact.
Energy supply
In energy supply, particularly in power plants and in the generation of renewable energies, flow charts are crucial for vividly presenting and optimising generation and conversion processes. For example, they visualize the process from fuel supply to power generation and allow efficient control and monitoring. In thermal power plants, flow charts show the various thermodynamic processes, such as steam generation, turbine work and the return of water to the cycle. In the area of renewable energies, such as in biogas plants, wind power and solar plants, flow charts help to illustrate the various process steps for energy use and storage. By mapping energy conversion processes in flow charts, energy suppliers can specifically monitor and control their plants in order to maximize efficiency and minimize emissions.
FAQ — Frequently asked questions about the flow chart
What is a flow chart?
A flow chart is a technical drawing for the schematic representation of processes or plants. It shows the flow of materials, energy, and information through various components and process stages. Standardised by standards such as DIN EN ISO 10628, it is used for uniform documentation.
What details do flow charts contain?
A flow chart contains detailed information about plant components, connections and process flows. This often includes the following elements:
- Process components: Presentation of containers, pipes, pumps and other plant components.
- Interconnections: Pipelines and other connections between components, often marked with diameter and material.
- Measuring points: Positions and functions for measurement, control and regulation instruments (MSR) to monitor and control operations.
- Energy flows: Information on how energy (e.g. heat or electricity) enters or is used in the system.
- Inscriptions and markings: Reference markings in accordance with DIN and ISO standards, which enable the components to be clearly identified and assigned.
What are the advantages of flow chart?
Flow charts are valuable tools in industry for understanding, planning and controlling processes and systems. Key benefits include:
- Transparent process presentation: Visualize the flow and structure of a process, making it easy to understand how it works.
- Efficient planning and troubleshooting: They enable weak points or bottlenecks to be identified quickly.
- Documentation help: Support plant management and serve as a means of communication between engineers, technicians and other stakeholders.
- Optimization potential: Identify potential for improvement, as the entire process is clearly presented.
What are the limits of flow charts?
Despite the many advantages, flow schemes also have some limits:
- Complexity: In very large or complicated systems, flow charts can become overloaded and confusing.
- Limited momentum: Flow charts show static information and are less suitable for representing dynamic changes in operation or process conditions.
- Symbolism that needs explanation: A flow chart can only be read and interpreted by experts, as it often uses a standardized symbolic language.
What tools can I use to create a flowsheet?
There is specialized software for creating flow charts. The most well-known tools include:
- AutoCAD Plant 3D: Designed for technical drawings and specifically for plant construction and plant design.
- Microsoft Visio: Provides templates and icons for simple flow charts.
- Lucidchart: A web-based tool that enables collaborative work on flow charts.
- SmartDraw and ConceptDraw: Provide a user-friendly interface and features for creating technical diagrams.
Can I derive parts lists from a flow chart?
Yes, modern P&I systems make it possible to automatically derive parts lists from the flow diagram. These parts lists contain precise information on the required components and materials and are often directly available in a spreadsheet format that can be used for calculations. This enables a detailed and accurate calculation of offers, which promotes planning and cost efficiency.
Which standards apply to flow charts?
There are binding standards for the creation of flow diagrams. DIN EN ISO 10628-1 specifies which information must be included in a flow diagram and which may be added as an option. In addition, the IEC 81346 standard enables standardized identification of system components. These standards ensure uniform communication and documentation across all project phases, from planning to maintenance.
What does R&I mean?
R&I stands for “piping and instrumentation.” This is a term used in process engineering and plant engineering, which is often associated with the P&I flow diagram or diagram. Such an P&I flow diagram shows in detail the pipelines, valves, measurement points and instrumentation in a plant. It provides an exact overview of all components and their connections and is essential for planning, monitoring and maintaining a process.
What does EMSR mean?
EMSR stands for “Electrical Measurement, Control and Regulation Technology.” In a P&I flow diagram, the EMSR points are the points where the process is monitored and controlled. These bodies are marked in accordance with DIN 19227 and contain functional descriptions and an identification number. EMSR stations are used to automate the process and to monitor operating parameters. The symbolism also provides information about the operating and monitoring options at these locations, which is decisive for technical and operational process reliability.
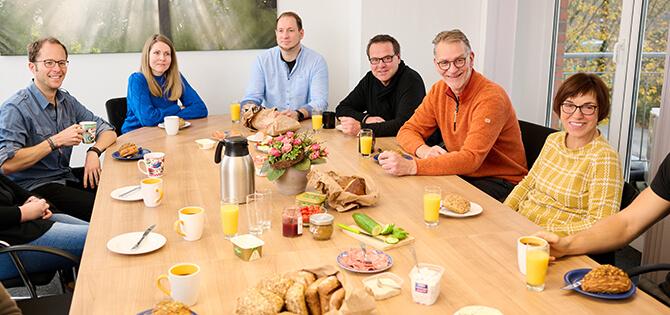
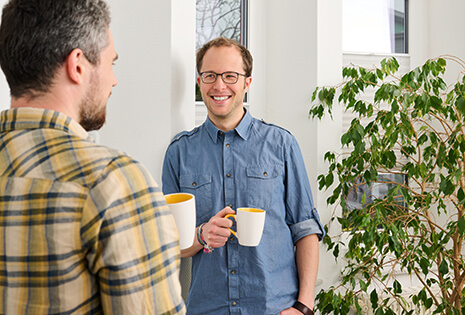
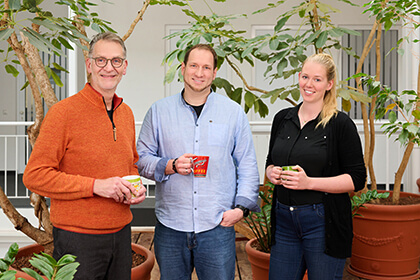
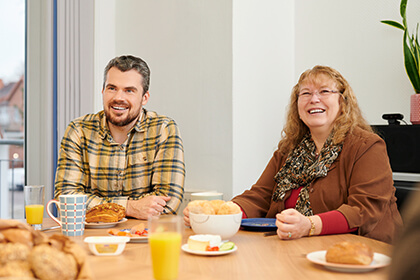
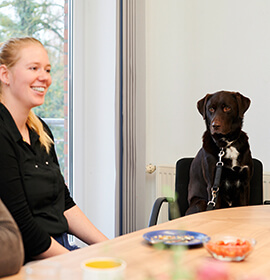
Are you an engineer or designer looking for new challenges? With us you can expect a familiar atmosphere and exciting tasks!
View Job Ads Now!