What is a basic flow diagram?
A basic flow diagram, also known as a “block flow diagram” or “principle diagram”, is a simplified, schematic representation of a process or a technical plant in process engineering. It uses minimalistic symbols, such as boxes or blocks, which are connected together by lines or arrows to represent the essential process steps and the main directions of material flows. A basic flow diagram thus provides a quick and easy-to-understand overview of the general flow of a process. Main substances such as starting materials and products are named, and sometimes additional information such as substance quantities, energy flows or important operating conditions (e.g. pressure and temperature) is included.
Historical development of basic flow charts
Basic flow charts have developed from the need to present complex chemical or technical processes in a clear and simplified manner. This form of presentation has evolved over time with the standardization of symbols and the introduction of standards such as EN ISO 10628. The original, rudimentary presentation of process flows has been refined over the years to meet the growing requirements for readability and comprehensibility.
Distinction from other flow sheet types
In process engineering, in addition to the basic flow diagram, there are other flow sheet types that are used depending on the level of detail and area of application:
- Process flow chart: More detailed than the basic flow diagram, in addition to the basic processes, it also shows specific information on the exact process conditions, apparatus and material flows. A process flow chart is used to understand the process flow more precisely and is particularly relevant for technical and chemical process optimization.
- Pipeline and instrument flow diagram (P&I flow diagram): Even more specific than the process flow chart, it comprises detailed information on pipelines, instruments and control devices. The P&I flow diagram shows the exact structure of a plant and provides support, particularly in the area of plant control and maintenance.
Compared to these more detailed flow charts, the basic flow diagram only represents a reduced, schematic overview that focuses on the essentials in order to provide a quick overview of the process structure.
What are basic flow charts useful for?
Use in concept and basic planning
As part of pre-engineering, the basic flow diagram provides a simplified but meaningful representation of the entire process sequence. This form of overview makes it possible to quickly understand the sequence and connection of the basic structure of a plant and the individual process steps. This makes it possible to estimate the need for resources and put planning on a solid basis at an early stage without having to go into technical details. Especially in the early phases of a project, the basic flow chart makes planning and decision-making easier by providing a clear visualization of the processes and dependencies in the process.
Communication and documentation support
Basic flow charts are an effective means of communication between various departments and specialist areas, such as between engineers, technicians and plant managers, in various engineering phases, such as basic and detail engineering. The simplified presentation ensures that even people who are less tech-savvy can quickly get an idea of how the process is going. The basic flow diagram therefore serves as a common language that promotes understanding of the processes and minimizes misunderstandings. In addition, it functions as important documentation for the process, so that the plant details and process steps remain comprehensible even later, for example during maintenance work or when training new employees.
Contribution to cost estimation and risk assessment
A basic flow chart significantly supports the cost estimation and risk assessment of a project. By presenting process steps, material flows and the required plant components, it provides a solid basis for quantifying material and energy consumption and thus estimating the resulting costs. It is also easier to identify potential risk factors, such as points where adverse metabolic effects or high pressures can occur. This overview helps to analyze high-risk areas in advance and to plan safety measures, which is crucial for efficient and safe plant planning.
Basic flow charts as a basis for process optimization and troubleshooting
When operating a plant, basic flow charts are essential for continuous process optimization and troubleshooting. Since the basic flow diagram schematically depicts the main material flows and energy paths, engineers and technicians can quickly identify potential for efficiency improvements when analyzing performance data, for example through adjustments to flow rates or operating conditions. In the event of a fault or failure, the basic flow chart provides quick orientation to identify problem areas and take targeted troubleshooting measures.
Components and symbols in basic flow charts
The symbols and components used in a basic flow diagram help to clearly represent the structure and functioning of complex systems. Basic flow charts use standardized symbols that provide a universal language for representing and understanding systems and processes.
Main components in basic flow charts
- Process vessels and reactors: These symbolize the main devices in which chemical reactions and physical transformations take place. The presentation is usually rectangular or cylindrical, often in combination with symbols for temperature or pressure information.
- Pipes and conduits: They connect the various components and show the material flow. The directional arrows show how and where materials are moving. The size and type of pipe can also be specified, which provides important information about pressure and temperature.
- Pumps and compressors: These symbols indicate points where pressure is increased or volume is changed. They are characterized by characteristic shapes, such as triangles and circles with special markings.
- Heat exchanger: These components symbolize the heat flow and are represented by special icons that indicate the exchange of thermal energy between two media.
- Valves and control devices: Valves control the flow and direction of liquids and gases. Different valve types are marked with different symbols, such as simple straight-through valves, check valves, and control valves.
- Separators and filters: Separators separate mixtures and are often presented as special, labelled containers. Filters symbolize the removal of solids and are usually represented by grid or network representations.
Symbols and their meaning
- Standardised symbols: For basic flow diagrams, there are standardized symbols in accordance with international standards, such as ISO or DIN, which ensure that symbols are understood worldwide. Such symbols are often kept geometrically simple, such as circles, squares, and triangles with clear, unique additions.
- Liquid flow and gas flow symbol: With arrows, line structures and sometimes colored markings, you can immediately identify various types of flow, such as liquids, gases and steam flows.
- Temperature and pressure displays: Measurement points and sensors for parameters such as temperature, pressure and flow rate are often recorded in basic flow charts and displayed as small circles or rectangles with letter or number markings.
- Special signs for security and control mechanisms: Safety components such as pressure relief valves, safety valves or emergency shutdowns are indicated by specific symbols. Control units that deliver information to central control systems are also clearly marked.
Using the symbols for various material flows
An important aspect of basic flow charts is the visualization of different material flows and types. Special symbols and arrow designs, such as broken lines for steam and solid lines for liquids, allow clear differentiation. The use of different line thicknesses also signals the flow volume and provides information on the technical design of the lines and connections.
Symbol legend
Each basic flow diagram contains a legend that explains the symbols used and their meaning. This legend is essential to capture and analyze the details of the flow diagram without misunderstandings.
Creation of a basic flow diagram
Step-by-step guide to creating a basic flow diagram
- Determining the scope of the process Define the exact scope of the process that is to be represented in the basic flow diagram. Ask yourself the question: Which process stages are relevant, and which devices and material flows must be considered? A clear distinction helps you to focus on the essential aspects.
- Gather data and information Collect all necessary data and information about the components, substances and conditions involved. These include process parameters (temperatures, pressures, flow rates), device specifications and safety requirements. The quality of the flow chart depends largely on the availability and accuracy of this data.
- Creating the basic structure of the process Outline the basic process flow, in which you arrange the most important process steps, such as reactions, distillations or heat exchange. This can be done on paper or a digital note first. It is about developing a general understanding of the order and connection of steps.
- Arrangement of main units Place the main units in the flow chart, such as reactors, columns, pumps, and heat exchangers. These components are often presented in a logical order that corresponds to the flow of materials or energy. Pay attention to the real distances and relative positions of the units to get the most practical picture possible.
- Connecting the units via lines Draw the lines between the units that represent the flow of materials and energy. Make sure to clearly label the flows and mark the direction of flow. Many software solutions have special tools for this, which help you to ensure a clean and easy-to-read presentation.
- Insert control loops and instrumentation Add control and regulation elements, such as valves, pressure and temperature sensors, and measuring devices. These instruments enable subsequent automation and monitoring of the process and are therefore essential for the flow diagram.
- Defining the material flows Name the material flows and, if necessary, provide them with information about the substances they contain and important parameters (e.g. flow rate, temperature, pressure). This contributes to the accuracy and traceability of the flow chart.
- Review and fine-tune Check the basic flow chart for completeness and comprehensibility. Check whether all relevant process steps, devices and connections are correctly placed and labelled. Ideally, discuss the flow chart with colleagues or project participants to uncover any gaps or ambiguities.
- Finalization and storage Save the final version of the basic flowsheet in an appropriate format so that it can be easily accessed and edited later. It is recommended that you save the document in common formats (such as PDF) to ensure compatibility.
Choosing the right software
Good software makes it easier to create basic flow charts precisely and efficiently. The choice of software depends on the complexity of the basic flow diagram and the planned area of application. Here is an overview of the tried and tested options:
- Microsoft Visio: Visio is particularly popular for basic flow charts because it offers a variety of diagram and icon templates that are easy to customize. For users who are looking for a clear tool without much training, Visio is ideal for simple basic flow charts.
- AutoCAD P&ID: With AutoCAD P&ID, flow charts can be created with a high level of detail and precise technical presentation. This software is particularly suitable for more extensive and complex basic flow diagrams and offers specific tools for process engineering. We at GCEA GmbH also use AutoCAD, as it is particularly suitable for creating and editing complex diagrams in projects.
- Aspen Plus or Aspen HYSYS: In addition to creating flow charts, Aspen Plus and Aspen HYSYS also offer simulation options and are firmly established in process engineering. Aspen HYSYS allows complex processes to be simulated and modelled, which is particularly helpful for planning and optimising systems.
- Lucidchart: Lucidchart is cloud-based software that combines diagramming and collaboration tools. It is particularly suitable for teams that want to work together in real time and enables intuitive operation and integration with other applications.
- CAD Schroer M4 P&ID FX: This software, developed specifically for process engineering, offers comprehensive tools for creating P&ID and basic flow charts. The symbol libraries and automated report generation, which saves time and minimizes sources of error, are particularly helpful.
Application examples in process plant engineering
Basic flow diagrams are used in a wide range of industries.
Process design and plant planning in the chemical and pharmaceutical industries
In the chemical and pharmaceutical industries, process design plays a central role in the planning and development of plants that can implement chemical reactions and synthesis processes reliably and scalably. The development of a suitable basic flow diagram helps to present complex processes in a structured manner to ensure efficiency and safety.
- Scalable reaction and synthesis processes: Scalable processes are crucial for transferring reactions developed on a laboratory scale to industrial scale. A well-thought-out basic flow diagram ensures that parameters such as reaction time, temperature and pressure can be controlled on a large scale to ensure consistent product quality.
- Thermal separation processes: Thermal separation processes such as distillation or evaporation are often used to separate substances based on their boiling points. The efficient planning of these processes depends on a detailed flow diagram in order to optimally coordinate heat supply, pressure conditions and throughput.
- Sterile processes: In the pharmaceutical industry, sterility is a top priority to prevent contamination. Basic flow charts help to design sterile production lines by taking into account cleanroom requirements and disinfection processes, so that the risk of contamination is minimized.
Energy and environmental technology
Energy and environmental technology relies on a variety of processes for the treatment and use of renewable energy sources as well as for waste treatment and resource conservation. A precise process presentation is required here in order to meet the requirements of environmental standards and to work sustainably.
- biogas plants: Biogas plants convert organic waste into biogas, which is used to generate energy. A basic flow chart makes it easier to plan the fermentation process and shows how various waste streams and fermentation processes are controlled and monitored.
- Waste gas purification and waste water treatment: Exhaust gas and waste water treatment is essential for environmental technology. A well-thought-out flow chart shows the steps for removing and neutralizing pollutants and enables compliance with strict environmental requirements.
- Heat recovery systems: Heat recovery reduces energy consumption and increases the efficiency of a plant. Basic flow charts of these systems help to integrate heat exchangers and other components that utilize the waste heat and reintroduce it into the production cycle.
Food and beverage industry
The food and beverage industry requires precise and hygienic process solutions that meet the high standards of food processing. Clean and detailed planning ensures safety and quality.
- Process equipment for beverage production: Beverage production systems must be designed for efficiency and hygiene. A basic flow diagram helps to represent production processes such as mixing, pasteurization and filling in order to ensure the quality of the end product.
- Dairy processing and dairy industry: Hygienic working methods and fast processing times are crucial in milk processing. With a basic flow diagram, the stages of pasteurization, homogenization and filling are clearly structured and optimized.
- Aseptic production equipment: Aseptic processes are essential to preserve packaged foods without preservatives. Planning such processes requires a precise description of the sterilization and filling processes in a flow chart in order to minimize contamination risks.
Petrochemicals and refinery plants
The petrochemical industry and refineries process large quantities of fossil raw materials and require robust and safe plants to produce chemicals and fuels. Optimizing these processes is critical to maximize efficiency while meeting environmental regulations.
- cracking and distillation plants: These plants convert crude oil into various products, such as gasoline and diesel. A detailed basic flow diagram shows the phases of heating, cracking, distillation and post-treatment and contributes to monitoring and process optimization.
- Polymer production: The production of polymers requires precise control of reaction parameters. With a flow chart, the steps of polymerization, purification and further processing can be presented in a structured manner, which increases the quality of the end product and process reliability.
- gas treatment plants: These systems remove impurities from natural gas and make it usable for further processing. A flow chart helps to efficiently plan gas purification and drying steps and to comply with legal regulations to reduce emissions.
Frequently asked questions about basic flow diagrams
What is a basic flow diagram?
A basic flow diagram, also block flow diagram or principle diagram, is a simplified representation of a process or plant in process engineering. It shows key process steps and material flows using symbols and connections and provides a quick overview of how a process works.
What are the limitations of basic flow charts?
Basic flow charts are used to simplify the presentation of processes, but their abstraction also has limitations:
- Limited level of detail: They do not represent detailed technical specifications. Details such as exact pressure and temperature conditions or small components are often omitted.
- Limited change flexibility: Adaptation is time-consuming, particularly with paper-based basic flow charts. Even with digital versions, the effort required for complex changes is high, as several adjustments are often necessary in different areas.
- Limitation through standardization: Standards and norms determine which symbols and display options may be used. This limits flexibility when presenting special or unconventional process steps.
- No real-time display: Basic flow charts represent static information and are therefore not suitable for real-time monitoring or short-term adjustments. Dynamic visualizations or digital twins are better suited for these tasks.
Which standards and norms apply to basic flow diagrams?
There are internationally recognized norms and standards for creating basic flow charts, which are intended to ensure a uniform presentation and prevent misunderstandings:
- DIN EN ISO 10628: This standard specifies the general requirements for basic flow diagrams and the presentation of processes in process engineering. It also defines the symbols and structures that may be used in basic flow charts.
- ISO 14617: This standard describes graphical symbols for technical diagrams and is often used in addition to ensure uniform symbolism.
- ANSI/ISA S5.1: Widely used in North America, this standard provides instructions for symbols in instrumentation and process flow diagrams, which may also be relevant for basic flow diagrams.
- Guidelines of the VDI (Association of German Engineers): The VDI provides recommendations on the structure and design of basic flow charts, which is particularly important in German-speaking countries.
What are the challenges and sources of error when creating a basic flow diagram?
Creating a basic flow diagram is a complex process that is often characterized by the following challenges:
- Information collection: Comprehensive and accurate data collection is essential. Inaccurate or incomplete data often result in inaccurate or misleading representations.
- Consistency of presentation: The symbols and representations must be consistent and compliant with standards to avoid misunderstandings. This is particularly important when multiple stakeholders are working on the project.
- Interpretation errors: Misunderstandings when interpreting symbols and processes often lead to errors in system planning.
- Outdated information: Changes to the system that are not incorporated into the basic flow chart increase the risk of incorrect planning and safety problems.
Another common mistake is the lack of regular updating of basic flow charts, which leads to a discrepancy between the presentation and the real system.
How do I avoid mistakes when creating a basic flowsheet?
In order to minimize errors when creating a basic flow diagram, you should pay attention to careful planning and a methodical approach. Here are a few proven strategies:
- Careful data review: Make sure that all data used is up to date and correct. Check sources multiple times, especially for critical process parameters such as temperature, pressure, and material flow.
- Use standards-compliant symbols: Use symbols in accordance with applicable norms and standards (such as DIN EN ISO 10628 or ISO 14617). Uniform symbols prevent misunderstandings and increase comprehensibility.
- Step-by-step creation: Break down the basic flow diagram into logically structured steps. This allows you to review each section individually, identify and correct errors early on.
- Regular reviews with the team: Carry out regular reviews with other specialist departments and project participants. External perspectives and feedback help identify and eliminate potential errors.
- Documentation of assumptions and deviations: Carefully document all assumptions, simplifications, and deviations from the standard. This makes it easier to understand and reduces the risk of misinterpretations as the project progresses.
- Use software tools in a targeted manner: Choose specialized software that automatically supports error checks and consistency checks. Many modern tools provide validation features and enable more efficient troubleshooting.
- Regular updates: Always keep the basic flow chart up to date. Update changes in processes or plant structure directly to avoid a discrepancy between presentation and reality.
What does the future hold for basic flow charts?
Digitalization and progressive automation are significantly influencing the development of basic flow diagrams. In the future, it is expected that software solutions will increasingly offer automated functions for creating and adapting basic flow charts. These technologies could enable features such as AI-based optimizations and improved simulations for complex process flows. In addition, the use of cloud-based solutions for basic flow diagrams is becoming more likely, which enables more efficient, location-independent collaboration. With digital twins that supplement basic flow charts, it could be easier in the future to visualize real-time data and integrate it into the planning and maintenance of systems.
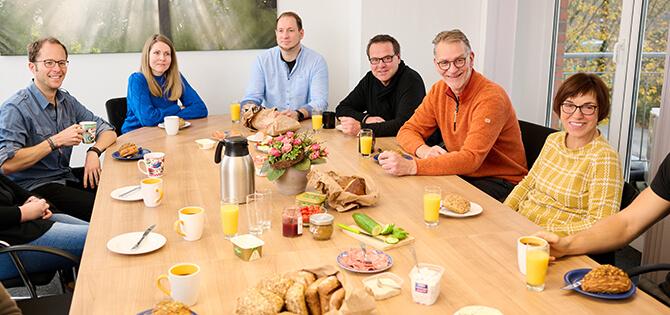
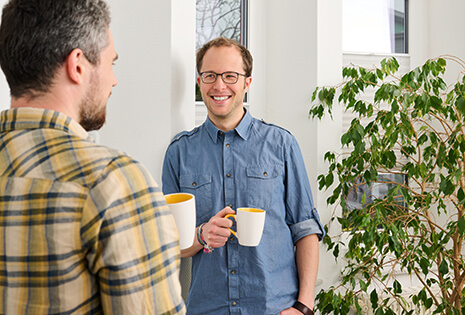
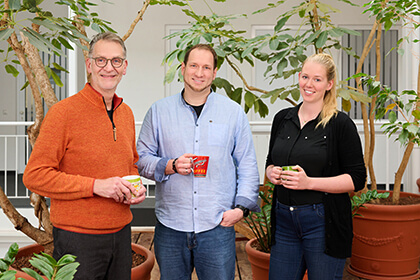
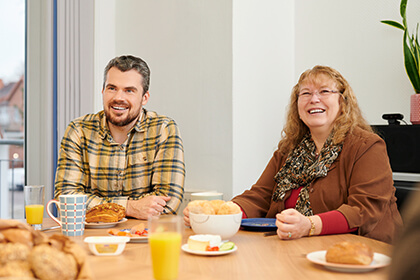
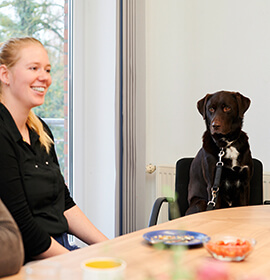
Are you an engineer or designer looking for new challenges? With us you can expect a familiar atmosphere and exciting tasks!
View Job Ads Now!