What is a process flow chart?
A process flow diagram (PFD) is a technical drawing that represents the main aspects of a production process in process engineering. It visualizes the sequence of process steps, apparatuses, machines and pipeline systems as well as key process variables such as pressure and temperature.
Process flow charts make it easier to understand the flow of a process or how a plant works and provide all relevant information needed to plan, control and optimize processes.
Historically, process flow charts have been created to simplify and standardize the complexity of technical processes in the chemical industry and later also in other industrial areas. Since industrialization, the process flow chart has been continuously used as a universal tool to comprehensibly represent the construction of plants, the execution of processes and the flow of materials and energy within the plant. Standardizations such as EN ISO 10628 later standardized the presentation and enabled a clear and understandable visualization, which simplifies communication between different specialist departments.
Types of process flow charts
There are various types of process flow charts, which vary depending on the purpose, level of detail and subject area. The main types include:
Basic flow diagram (Block Flow Diagram, BFD)
The basic flow chart represents the essential steps and units of a process on a very abstract level and is therefore particularly useful for pre-engineering. This type of process flow diagram shows only the main components of the process and dispenses with detailed information. Block flow charts are particularly useful in the planning phase to get an initial overview of the process and the main steps.
- Area of use: Early planning phases to get a rough understanding of the overall process.
- Details: No specific details about piping, instrumentation, or exact operating conditions.
Process flow diagram (PFD)
The process flow chart provides a more detailed presentation than the basic flow diagram and shows all relevant process steps, main equipment and essential pipelines. PFDs are particularly useful for illustrating the flow of the entire process with the specific material and energy flows.
- Typical information: Apparatus and equipment, main flows, temperature and pressure data.
- Area of use: Engineering planning and design phase, as the flow charts can be used for a detailed analysis of the process.
Piping and instrumentation flow diagram (P&I flow diagram, P&ID)
The pipeline and instrumentation flow diagram goes into even more detail than the process flow diagram. A P&ID shows all equipment, instruments, pipes, valves and control circuits that are required to operate a system. The high level of detail enables technicians and engineers to carry out maintenance and operation efficiently. The PFDs often serve as a basis for basic engineering, while the detailed information in P&IDs is essential for detailed engineering.
- Details: All pipes, instruments, control and regulation circuits.
- Purpose: Precise instructions for operating, maintaining and monitoring the system.
Control flow chart
A control flow chart focuses on the presentation of automated control and regulation systems within a process. It shows control loops, control devices and sensors that contribute to automating the process. Control flow charts are particularly helpful when setting up and testing control systems.
- Area of application: Optimization and testing of control and regulation technology.
- Specifics: Focus on the logic and control process, without explicit details of the physical plant structure.
Energy flow diagram
An energy flow diagram represents the energy aspects of a process and provides information about energy consumption and energy distribution within the plant. It helps to analyze the efficiency of a system and identifies areas of high energy consumption.
- Details: Energy volumes, heat flows, efficiencies.
- Benefit: Identification and reduction of energy losses.
Safety flow chart
Safety flow charts highlight safety-relevant aspects of a process. These process flow charts highlight potential hazardous areas, safety valves and emergency shutdown systems. They are an important part of risk assessment and contribute to the safe design and operation of the plant.
- Contents: safety valves, emergency shutdown systems, potential hazardous areas.
- Application: Managing risks and ensuring safe operations.
Material flow diagram
The material flow diagram describes the course and quantity of material flows within a process. It shows how raw materials, intermediate products and end products are moved and processed in a plant. This is particularly helpful for identifying bottlenecks in the material flow and increasing the efficiency of the production process.
- Emphases: Material flows, quantities and flow directions.
- Scope of application: Optimizing production processes and minimizing material losses.
Important symbols and notations
Symbols in the process flow diagram: meaning and use
Process flow charts use specific symbols to represent various components, such as machines, lines and valves. These symbols are standardized and each has a clear meaning, which makes it much easier to understand the flow diagram. Recognizing and interpreting these symbols is crucial for understanding how a process works and analyzing the role of individual components.
Examples of symbols:
- Container/tank: A rectangular icon with a half-open or open top represents a tank that stores liquids or gases.
- Pump: A circle connected to a triangle represents a pump and indicates that liquid is being pumped at this point.
- Valve: A square symbolizes a valve that controls the flow of media.
- Heat exchanger: A heat exchanger is symbolized by two intertwined rectangles and represents the exchange of heat between different flows.
For example, you can immediately see that it is a compressor based on a circle with a distinctive triangle. This enables you to understand the importance of this component within the process and to analyze how it influences the medium.
Flowchart symbol language: Understanding flow direction and control
In addition to standard symbols, the symbolic language in process flow charts is important to illustrate the flow direction and control of material or energy flows. Various lines and arrows in process flow charts describe these flows and their degree of control.
Icons to represent flow and control:
- Arrows: An arrow shows the direction of the flow of materials or energy, so you can immediately see where a stream is flowing.
- Dotted lines: These represent control or data paths that point to specific control points.
- Line widths and types: Different line types, such as solid or dashed lines, indicate the degree of control over a stream. A solid line often stands for a completely controlled current, while a broken line indicates a less strictly controlled line.
- Circles: Circles are often used to identify measurement points that are necessary to monitor certain process parameters.
Step-by-step instructions for creating a process flow chart
Step 1: Choose the right tool
To create a process flow diagram, you need specialized software that meets technical requirements and offers common symbols. A common tool that we also use to create process flow diagrams is AutoCAD Plant 3D. It enables a detailed representation of processes and supports the creation of precise piping and instrumentation diagrams. Alternatively, there is software such as Microsoft Visio for simpler flow diagrams or specialized process design tools such as Aspen Plus and Siemens COMOS for more comprehensive and simulation-ready diagrams. The choice of software depends on the level of detail you need and the requirements of the process.
Step 2: Purpose of the process flow chart
Define exactly what you need the process flow chart for. Requirements vary, depending on whether the diagram is created to plan a new process, for internal communication, or for training purposes. The purpose determines how detailed the flow diagram must be and which symbols and notations you should use.
Step 3: Layout planning and structure
Plan the layout of the process flow chart before you start the detailed development:
- Set flow direction: The process flow is usually presented from left to right or from top to bottom to ensure a clear reading direction.
- Placement of main components: Determine where the most important units such as reactors, heat exchangers, pumps or separation units should be positioned.
- Scale and spacing: Make sure there are consistent distances between the individual units to achieve a clean and easy-to-read presentation.
- Pre-arrangement of measurement and control elements: These elements should also be planned as they monitor and control an important part of the process.
Step 4: Detailed preparation of the process flow chart
Now start with the detailed development:
- Mark process units: Mark every important process unit and use standardized symbols (usually provided by the software), e.g. for reactors, storage containers and other technical devices.
- Make connections: Connect the units to piping systems or pipes and ensure clarity. The connecting lines should precisely represent the reality of the process.
- Mark flow directions: Add arrows to indicate the flow direction and make sure that all major and tributary flows are clearly understandable.
- Insert measurement and control elements: Place measuring devices such as pressure, temperature or flow meters at the relevant locations. Also add control elements that influence the process (such as control valves or automation systems).
Step 5: Check and correct the flow chart
Check your process flow chart for completeness and accuracy. Make sure that all symbols have been used correctly and in accordance with standards and that all flow directions and connections are clearly represented. Correct potential errors and simplified representations, if necessary, to ensure clear readability for other engineers and stakeholders.
Step 6: Labeling and Labeling
Give each unit and connection a clear name. These should be clear and reflect the purpose of the respective component or line. You can also include a legend that explains all symbols. Clear labeling makes understanding easier and reduces the risk of errors.
Step 7: Finalization and export
When the flow chart is complete, save it in a common format (e.g. PDF or DWG, depending on the requirements of the target group). Verify that the format is supported in the planned application.
Applications and practical examples of process flow charts in process engineering
Chemical process engineering
In chemical process engineering, process flow charts are used to visualize and plan complex chemical production processes. Here, they are used to structure the various process steps for converting raw materials into end products. Applications range from the production of basic chemicals such as ammonia or sulfuric acid to complex synthesis processes in the pharmaceutical industry. For example, process flow charts help to arrange reactors, heat exchangers, distillation columns and other apparatus and to record the material and energy flows. This enables efficient control and optimization of production processes.
Practical example: In the production of ammonia, nitrogen from the air and hydrogen from natural gas are converted into ammonia. A process flow chart shows the steps from gas treatment to compression to reaction and cooling of the end product in order to control the process flow and identify bottlenecks.
Mechanical process engineering
Mechanical process engineering focuses on physical separation and mixing processes in which substances are processed without chemical transformation. Process flow charts are used here, for example, when planning mills, filters, cyclones, centrifuges and other mechanical devices. The aim is to adjust particle sizes and to separate or mix substances. This technology is used in the food, pharmaceutical and construction industries, where it is often important to precisely control material properties such as purity or particle size.
Practical example: In a grain mill, the process flow diagram shows the grain's path through the various mill stages, sieves and filters, which are used to separate and adjust the particle size. Such representations make it possible to monitor the entire milling process, which improves quality and efficiency.
Water and waste water technology
In water and wastewater technology, process flow charts are used to represent treatment processes in which wastewater is purified and drinking water is treated. They show the sequence of mechanical, biological and chemical purification steps required to remove pollutants and comply with water quality standards. Such flow patterns generally include sedimentation basins, biological clarifiers, aeration stages and disinfection plants.
Practical example: A municipal sewage treatment plant uses process flow charts to map the process from coarse-break removal to sludge treatment to the last purification stage in the sand filter. This enables precise control and adjustment of processes in order to guarantee the legally required water quality.
Supply technology and disposal technology
Supply technology provides resources such as water, gas, electricity and heat, while disposal technology organizes the environmentally friendly and economical disposal of waste. Process flow charts help to represent systems for distribution and recovery in order to optimally control supply and disposal processes. In the area of waste disposal, for example, they show the path of waste from collection to sorting to recycling or final disposal.
Practical example: In thermal waste treatment, process flow charts illustrate the process from filling the waste to incineration and exhaust gas purification. This shows how heat is recovered to generate energy and pollutants are filtered out of the flue gas, which ensures environmentally friendly energy generation.
Frequently asked questions about process flow charts
Which standards and norms apply to process flow charts?
There are numerous norms and standards for process flow diagrams that are intended to ensure a uniform and comprehensible presentation worldwide. Of particular relevance is the DIN EN ISO 10628 standard, which sets out specific requirements for the structure and content of process flow diagrams, including the necessary symbols and labeling. This standard ensures that process flow diagrams can be easily interpreted by experts, regardless of the country or industry.
Another important standard is DIN 28004, which provides guidelines for the structure of process flow diagrams in chemical and process engineering. In the field of plant design, the standards VDI 3699 and VDI 3703 are also frequently referred to, which focus on piping and instrumentation diagrams (P&ID) but also contain aspects relevant to process flow diagrams.
Some international standards such as ANSI/ISA-5.1 (instrumentation symbols and labels) and ISO 14084 (for process illustrations and process flow diagrams) also play a role. Compliance with these standards ensures that process flow diagrams are clear and universally understandable, which makes both the planning and maintenance of systems more efficient.
What must be considered when documenting process flow charts?
The documentation of process flow charts is crucial because it records the complete functionality and structure of a plant and provides precise guidance to all parties involved. It is important that the documentation not only describes the current design and functioning of the system, but also shows changes and updates over time. To this end, all modifications and additions should be precisely documented to ensure complete traceability.
Another important point is the comprehensibility of the documentation. Use clear, unmistakable names and symbols that are defined in applicable standards. In addition, the documents should always be up to date and accessible to all departments involved. Integration into a document management system (DMS) can also be helpful to store documentation centrally and clearly so that changes and new versions are always comprehensible.
When archiving process flow charts, backup copies and regular updates are essential. Especially in safety-relevant areas, such as the chemical industry, documentation should be comprehensive and complete in order to avoid operational disruptions or risks due to outdated information.
What are the future prospects for process flow charts?
The future of process flowsheets will be significantly shaped by digitalization and new technologies. Digital flow diagrams, which are directly connected to process control systems, enable dynamic visualization of operating processes in real time. These dynamic process flow diagrams offer real-time monitoring and make it easier to immediately record the current status of the system and detect any faults at an early stage.
Another trend is the use of 3D visualizations and virtual simulations. These technologies make it possible to better understand complex systems as early as the planning phase and to identify potential weak points at an early stage in operating simulations.
The integration of artificial intelligence and machine learning is also pioneering. These technologies can support process flow diagrams in error detection and analysis. Algorithms could, for example, point out potential problems or optimization opportunities at an early stage and thus improve the efficiency and safety of the systems.
Process flow charts are therefore increasingly developing into dynamic, intelligent tools that not only support the planning and documentation of processes, but also contribute proactively to process optimization.
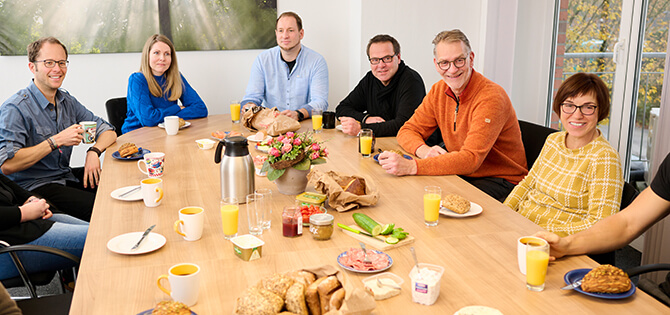
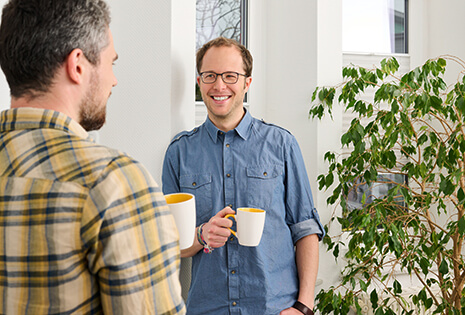
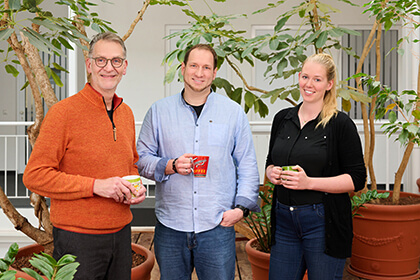
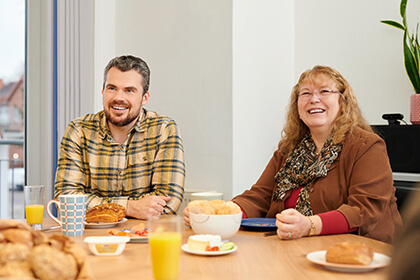
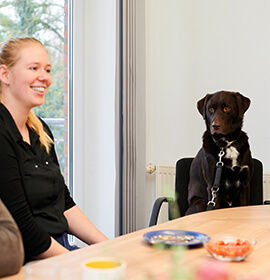
Are you an engineer or designer looking for new challenges? With us you can expect a familiar atmosphere and exciting tasks!
View Job Ads Now!