What is piping?
A pipeline, often referred to as a pipe system or line, is a system of pipes and fasteners that is used to transport materials such as liquids, gases and free-flowing solids. It can also transfer mechanical and thermal energy. Pipelines are essential components in a wide range of industries and applications, from drinking water supply to complex industrial processes.
Components of a pipeline
Pipelines consist of various components that work together to fulfill the desired transport function. Key components include:
- Tubes: The basic structure of the line that guides the medium to be transported.
- Pipe connections: These include fittings, flanges, fittings, sockets and special seals. Connections are often standardized to make it possible to combine parts from different manufacturers.
- Pipe support systems: These include pipe clamps and support elements that ensure the stability of the line.
- Fittings: Elements such as valves, ball valves and butterfly valves are used to control the medium flow.
- Compensators: They record movements and pressure differences in the line.
- Insulation: Heat or cold insulation protects the pipes and the media to be transported from external influences.
In addition, pumps, heat exchangers, pressure vessels and monitoring and measuring equipment are often integrated into a pipe system. These enable targeted control and monitoring of the entire transport system.
Historical development of pipelines
The history of pipelines goes back a long way. Even in ancient times, they were used for water supply. In cities such as Pergamon and Cologne, the construction of water pipes was an essential part of the infrastructure. Aqueducts were usually built there, which transported water over long distances. Pipelines were often used in these aqueducts to overcome differences in height.
In the Middle Ages, cast-iron pressure pipes were developed, which were used, for example, to supply water to castles and palaces. One example of this is Dillenburg Castle, for which a cast iron water pipe was laid in 1455. This type of pipe had a long tradition, particularly in the Lahn-Dill area, where foundries specialized in the production of such tubes.
Wood pipes, known as drawbars, were also widely used. These were made from tree trunks that were hollowed out and connected together. Such cables were still used up to the 20th century, particularly in rural regions.
An important milestone in the modern history of pipelines was the widespread installation of water pipes in Germany in 1898, where steel pipes were used for the first time and extensive water supply networks were created that supplied households directly. These early systems were often built by craft businesses such as blacksmiths, which played a central role in manufacturing.
Design aspects of pipes
Modern pipelines are technically demanding and must meet a wide range of requirements. Depending on the type of transported medium, operating pressure and external influences, the material and construction method of the pipes are selected. The standardization of fasteners facilitates the compatibility and replacement of parts from different manufacturers.
Compensators are used to protect cables from movement and vibrations. They are particularly necessary for pump connections to ensure a tension-free connection and to protect the pump from the forces in the pipe system.
By using various materials and techniques, pipelines can be adapted to specific requirements. This enables the safe and efficient transport of media in a wide range of applications.
Types of pipes
Closed systems
A closed pipeline system uses longitudinally bonded connections such as flanges and rigid attachments. This design ensures that the longitudinal force resulting from internal pressure is absorbed within the pipe wall and the connections. In this system, fastenings are only stressed by their own weight and dynamic forces. The thermal expansion is compensated for by using elastic pipe guides or joint compensators. The dimensioning of the wall thickness is based on EN 13480-3.
Open systems
Open piping systems use socket connections, loose fittings and axial expansion joints without tie rods. Here, the longitudinal force generated by internal pressure is absorbed as an external force by fixed points that are placed at the start and end of the line and at points of changes in direction or cross-section. Plain bearings and roller bearings are used to stabilize the lines against buckling.
Rigid and flexible pipes
Rigid pipes have a sturdy construction and offer little flexibility when stretching, meaning that they are used in areas with low thermal loads. Flexible pipes, on the other hand, allow greater adaptation to thermal expansions and mechanical loads. They can compensate for movements and vibrations and are often equipped with stretch belts or flexible connections.
Lined pipes
Lined pipes are internally coated with materials such as PTFE, cement mortar or alumina cement. These coatings provide protection against corrosion and chemical influences. For example, cast iron drinking water pipes are often lined with cement mortar to provide a protective layer. Such coatings are particularly important for sewage pipes in order to ensure long-lasting stability at a pH of 4.5 to 9.
Coated pipes
Pipelines can be sheathed to protect them from mechanical or thermal effects. In practice, coatings made of plastic, concrete or insulation materials, for example, are used. District heating pipes often have a plastic jacket, while steel gas pipes are often supplied with a plastic jacket. For special applications such as underwater pipes, concrete sheathing is used to provide stability and additional protection.
Pipelines for solids
These pipes, also known as chutes, transport solids such as granules, flour or dust. They are used in industries such as the cement industry and grain processing. The large radii are characteristic when changing direction in order to avoid blockages. In addition, particularly wear-resistant materials such as artificial basalt are used to increase the lifespan.
Steam pipes
Steam pipes are used to transport water vapor and require particular care when planning. In order to prevent the formation of condensation and the resulting risk of water shock, steam pipes must often be laid with a slope. The slope should be at least 1% in the direction of flow and at least 5% in the case of drainage against the direction of flow. A slope of even 5° is recommended in front of fittings to avoid droplet erosion.
Cryogenic piping
Cryogenic pipes transport materials at extremely low temperatures. The systems must therefore be protected against brittleness and well insulated. The insulation is usually provided by special materials such as expandable foam or granulated perlite. The system must compensate for thermal loads and be flexible enough to compensate for contractions caused by cold. Typical applications include liquefied gas plants such as LNG or cryogenic substances such as nitrogen.
Other types of pipes
In addition to the above, there are other special pipeline types that are designed to meet specific requirements:
- District heating pipelines: These are designed to transport hot water or steam over long distances to heating systems or residential buildings. They are particularly heat-insulated and often delivered pre-insulated.
- Connecting cables: These lead from the supply line to the main shut-off valve and start at the house connection line.
- Drinking water pipes: These pipes must comply with certain hygiene standards and must be installed frost-proof. Special requirements relate to preventing heating and protecting pipes from frost.
- Sewage pipes: They are used to dispose of waste water and are often covered with linings such as cement mortar to increase corrosion resistance.
- Gas pipes: To safely transport gases, these pipes are made of robust materials such as steel and are often coated with plastic to prevent corrosion.
- Circulation lines: These circulating lines circulate hot water using a circulation pump to keep hot water available at all times.
Design: Choose the right pipeline
When designing a pipeline, several decisive factors play a role, which ensure that the system can be operated efficiently, safely and economically.
Pipe class
The pipe class defines the specification of the pipeline and determines important parameters that are decisive for the design and operation of the pipeline. The selection of the pipe class is based on operating conditions and is essential for the selection of pipeline components. Factors such as the medium, temperature, pressure and the required mass flow rate play a role here. Economic aspects and the availability of spare parts are also taken into account. The pipe class therefore forms the basis for determining the material, the pressure resistance and other essential properties of the pipeline.
Nominal diameter
The nominal diameter describes the standardized inner diameter of a pipeline. It is calculated based on the desired mass flow and the maximum accepted pressure loss. The rule is that a larger pipe diameter reduces pressure loss, reduces flow noises and simplifies pipe attachment through larger spans. At the same time, however, a larger nominal size also results in higher investment costs, greater space requirements and higher heat loss. The nominal width is often selected on the basis of a standardized grid in order to reduce the variety of pipeline systems.
Pressure loss plays a decisive role in sizing. Even small changes in the inner diameter of the pipe can lead to significant fluctuations in pressure loss. The pressure loss is proportional to the fourth power of the diameter, which is why precise dimensioning is essential.
Nominal pressure
The nominal pressure indicates the maximum allowable pressure that the pipeline and its components must withstand. The nominal pressure is always selected based on the highest possible operating pressure to ensure safety. The operating temperature is also taken into account during planning, as high temperatures can reduce material strength. As a result, it may be necessary to increase the nominal pressure by several steps to ensure the safe operation of the pipeline. The calculation of wall thickness is based on specific standards and regulations that manufacturers must comply with.
Flow velocity
The flow rate in a pipeline influences pressure loss, noise and the risk of cavitation (in the case of liquids). In order to ensure optimum operation, certain guidelines for the flow rate should not be exceeded, depending on the medium, pipe profile and operating conditions. These guidelines vary for various media such as oil, water, steam or gas. For example, the recommended speed for pressurized water pipes is 1.5 to 5 m/s during continuous operation, while a speed of 5 to 10 m/s is recommended for gas pipes in the low pressure range.
When sizing a pipeline, the choice of an economic speed is crucial. This represents an optimum of the investment costs for the pipeline, the investment costs for pumps or compressors and the energy and maintenance costs over the entire operating period. The flow rate is also an important factor in determining whether laminar or turbulent flow is present.
In summary, the selection of pipe class, nominal diameter, nominal pressure and the consideration of the flow rate are key factors when designing a pipeline. They ensure the efficiency, safety and cost-effectiveness of the entire pipeline system.
Materials: Choose the right material
Plastics
In recent years, plastics have become the most important materials for pipe systems in Europe. With a market share of 54% and an annual volume of 2.5 million tons, they are leading the way. The most important types of plastic for pipes are polyethylene (PE), cross-linked polyethylene (PE-X), polypropylene (PP) and polyvinyl chloride (PVC-U). These materials are widely used in water supply, sewage disposal, gas supply and in the area of heat supply as well as in industrial pipelines.
- Polyethylene (PE): Particularly relevant in the rehabilitation of water supply pipes, resistant to corrosion and chemicals.
- Polyvinyl chloride (PVC-U): Particularly common in the wastewater sector, as it offers high stability and chemical resistance.
- Polypropylene (PP): Suitable for heating systems and waste water installations.
- PE-X: Used primarily for hot water pipes and heating systems, due to its heat resistance.
Copper
Copper pipes in accordance with EN 1057 are available in three degrees of hardness: soft, semi-hard and hard. They are widely used in building technology. The soft pipes are particularly suitable for installation in coils, while hard pipes are delivered in bars up to an outer diameter of 267 mm. Soft pipes are easy to bend and easy to process, but are not approved for gas installations.
- Material properties: Oxygen-free copper (Cu-DHP) with a copper content of at least 99.90%.
- Pipe connections: Copper pipes can be connected with press, solder or clamp fittings. These fittings are often fitted with special sealing rings to ensure tightness.
- Corrosion protection: To prevent corrosion in humid environments, copper pipes are often protected with plastic jackets or bandages. Contact with materials such as gypsum or ammonia-containing environments should be avoided.
Stainless steel
Stainless steel pipes are particularly appreciated in building technology due to their corrosion resistance and hygienic properties. Various stainless steel alloys are used, including grades 1.4401, 1.4404, 1.4520 and 1.4521. Each alloy has specific areas of application and is optimized for different requirements.
- Cr-NiMo steel (1.4401, 1.4404): Universally suitable for drinking water, gas and other media. These alloys offer high corrosion resistance and are resistant to chloride ions up to a certain content.
- Ferritic steels (1.4520, 1.4521): Particularly suitable for closed circuits such as heating systems or solar systems. They contain no nickel and offer an alternative solution to traditional austenitic steels.
- Connections and fittings: Stainless steel pipes are usually connected to press fittings made of the same or similar stainless steel alloy or gunmetal.
Unalloyed steel
Non-alloy steel is often used for piping in building technology. There are two main types of mild steel: threaded pipes, which are often black and are used for heating installations, and galvanized pipes, which are primarily used for drinking water pipes.
- C steel pipes: These are precisely manufactured and often galvanized to ensure corrosion resistance. In humid and corrosive environments, pipes with plastic coatings are also used.
- Sprinkler systems: C steel pipes are usually galvanized internally and externally to ensure long-term protection against corrosion.
Other materials
In addition to the main materials plastics, copper, stainless steel and unalloyed steel, other materials are also used for special applications:
- Nickel and titanium alloys: These materials are used when high chemical resistance and strength are required.
- Cast iron: Traditionally used in pipe manufacturing, particularly in supply and disposal lines.
- Concrete and reinforced concrete: Used in the disposal of waste water and rainwater.
- Ceramics and glass: Particularly suitable in corrosive environments or for wastewater pipes in laboratories.
- Combinations of plastics and metal: Multi-layer composite pipes offer additional stability and corrosion protection.
Each material has its own specific advantages and areas of application. The choice of the right material depends on the requirements for corrosion resistance, temperature resistance, flexibility and chemical load.
Pipe marking according to DIN 2403
Pipeline marking in accordance with DIN 2403 plays a decisive role in the identification and safe operation of pipelines. This standard specifies how pipes are color-coded and labelled in order to quickly identify the substances transported in them and their potential hazards.
Color coding by group
DIN 2403 divides the various flow materials into groups and assigns specific colors to them. This group color is the main characteristic of every label and, in conjunction with the font and additional color, provides clear information about the content of the pipeline.
Groups and group color
Each group refers to a specific type of flow material that is transported within the pipeline. The group colors according to DIN 2403 include:
- Water: Green (RAL 6032) — The pipes for water are marked green and are labelled with white letters.
- Water vapor: Red (RAL 3001) — Pipes that carry water vapor are red with white lettering.
- Air/vacuum: Grey (RAL 7004) — Air and vacuum lines are grey and have black lettering.
- Combustible gases: Yellow (RAL 1003) — For combustible gases, black is used as an additional color and font color.
- Non-combustible gases: Yellow (RAL 1003) — Here, red is used as an additional color, the lettering is black.
- Acidity: Orange (RAL 2010) — Acid lines are orange and are labelled with black letters.
- Laugen: Violet (RAL 4008) — Pretzel pipes have a purple color with white lettering.
- Flammable liquids and solids: Brown (RAL 8002) — Red is used as an additional color, the lettering is white.
- Non-flammable liquids and solids: Brown (RAL 8002) — These pipes have black as an additional color and white lettering.
- Oxygen: Blue (RAL 5005) — Oxygen pipes are blue and have white lettering.
Additional colors and lettering
The additional colors complement the main color to provide additional information about the properties of the flow material. This additional visual differentiation is particularly important with similar group colors to identify potential risks more quickly.
- Black: Additional paint for flammable gases and non-flammable liquids/solids.
- Red: Additional paint for non-combustible gases and flammable liquids/solids.
The font color on the identification tapes is for clear legibility. White is used for water and air, and black is used for acids and combustible gases.
Purpose and areas of application
The DIN 2403 standard aims to standardize the marking of pipes and to ensure safety in industrial plants, power plants, hospitals, the pharmaceutical industry and other areas. The clear color codes and labels make it easy to identify the content and contribute to safety during maintenance work and emergencies.
Where are pipes used?
Pipelines play an essential role in many areas of application. You can find them in the following areas of application:
- Heating, ventilation and air conditioning systems: Here, pipes ensure a pleasant temperature and high air quality in modern buildings.
- Underground pipe systems: These protect cables and supply lines such as water and gas pipes and help prevent damage and leaks.
- Industrial plants: In the food industry, pipelines transport raw materials and ingredients. They are also used in other industrial sectors, such as the chemical and petrochemical industries, to transport liquids, gases and chemical substances.
- Welding work: Flexible pipes are used to extract smoke and thus increase safety and air quality in the workplace.
- Kraftwerke: In steam power plants, pipelines are used to pump and control water vapor to operate turbines and generate energy.
Operation, maintenance and safety
After completion of a pipeline system, a careful inspection is necessary. You usually carry out a leak test to ensure perfect functionality. In particular, pressure-loaded pipes require special testing measures, as they often transport dangerous or corrosive substances.
In accordance with the Industrial Safety Ordinance, pipelines must be regularly inspected if they are under pressure and transport flammable, toxic or corrosive media. In doing so, you will check them by qualified persons or approved monitoring bodies. Test measures may include:
- Visual inspections: Here, you check the pipes for visible damage or corrosion.
- Non-destructive testing: Methods such as ultrasound and X-ray are used to identify potential cracks or weak points without damaging the pipe.
- Pressure tests: These confirm the tightness and stability of the pipe system.
- Support and suspension tests: These ensure the correct attachment and stability of the pipes.
In addition to the test, the Corrosion protection to maintenance measures to extend the lifespan. In addition, the pipes must be cleaned to remove deposits or dirt.
Which planning documents include pipelines?
In order to plan and build a pipeline efficiently, you need a variety of planning documents. These include:
- Basic flow diagram: It shows the basic process steps and connections of the plant.
- Process flow chart: Detailed presentation of technical processes and connections between plant components in process engineering.
- Pipeline and instrumentation flow diagram (P&ID): Links the pipes with the associated measurement and control equipment.
- Pipeline plan and installation plan: They are used for 2D planning and show the exact location of the pipes.
- 3D models: Modern planning software makes it possible to create 3D models that provide a precise overview of the pipeline systems.
- Pipe classes and special parts: It is specified which pipe classes are used and special parts are defined individually.
- Strength calculations: These calculations are carried out in accordance with applicable standards (e.g. DIN EN 13480) and confirm the load-bearing capacity of the pipes.
- Pipeline system analysis: This takes static and dynamic load cases into account and checks the load on the connections.
- Material Take-Off (MTO): It lists all required materials and determines their total dimensions.
- Pipeline isometrics: These include the exact dimensions and angles of the pipes as well as parts lists for production.
- Pipeline design list: Details of the dimensions and the materials to be used are recorded here.
- Test and quality assurance plans: They ensure compliance with all material, processing and testing requirements.
- Welding or joining instructions: They define the specific requirements for welds and connections.
With these planning documents, you can precisely plan and implement even complex pipeline systems, such as those used in large power plants or refineries.
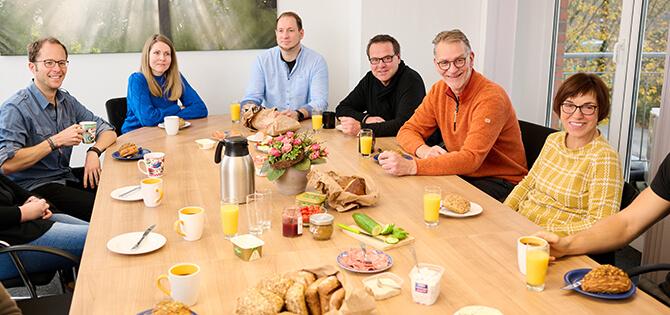
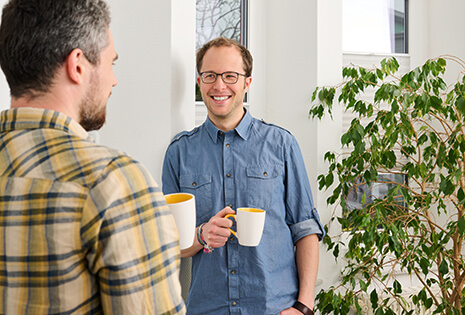
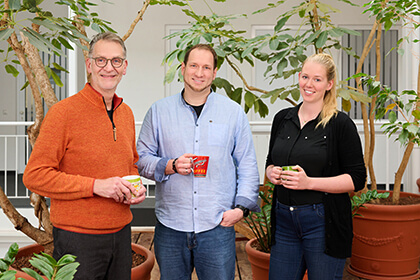
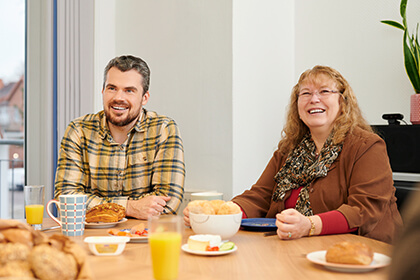
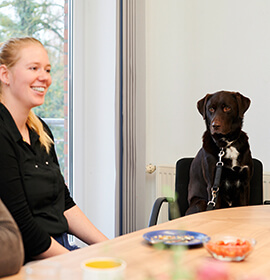
Are you an engineer or designer looking for new challenges? With us you can expect a familiar atmosphere and exciting tasks!
View Job Ads Now!