Pumps are essential machines used by engineers in various fields, including process engineering, to transport incompressible fluids, especially liquids. As working machines, they convert mechanical energy into kinetic energy, creating a pressure difference within the liquid that enables transport through pipes.
Depending on their function, pumps are divided into two main groups: displacement pumps and flow pumps. These groups encompass a wide variety of pump types suitable for different applications and media. But what types of pumps are there exactly, and how do they differ in their operation?
Types of Pumps by Functional Principle
Pumps operate based on two fundamental principles: the displacement principle and the kinetic energy principle. These can be divided into two main groups: displacement pumps and flow pumps.
Displacement Pumps use the displacement principle, where a defined volume of liquid is transported into a closed space and pushed further by mechanical displacement. This allows for uniform and controlled delivery, independent of the back pressure.
Flow Pumps, also known as centrifugal pumps, operate on the principle of kinetic energy. Here, the liquid is accelerated by rotating motion, converting kinetic energy into pressure energy. These pumps are particularly effective for high flow rates and variable pressure conditions.
Additionally, there is another less common operating principle: the hydraulic ram, which uses shock waves to transport liquid.
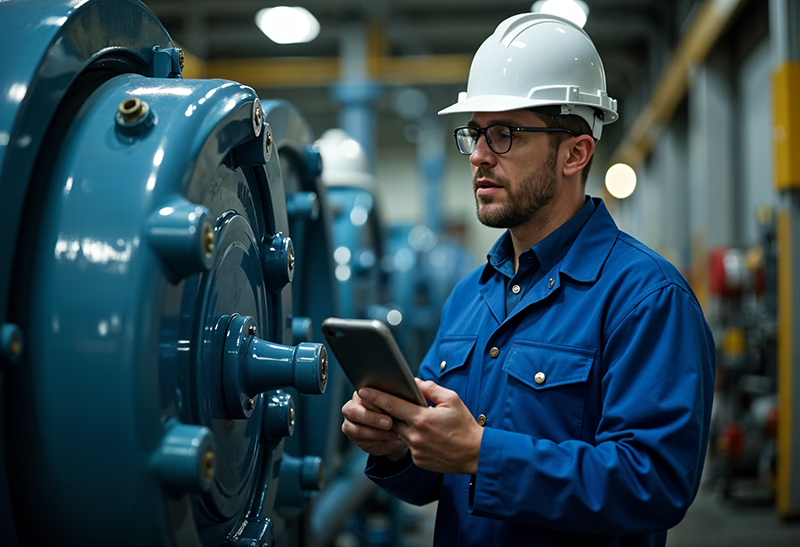
Flow Pumps or Centrifugal Pumps
Flow pumps, also known as centrifugal pumps, are the most commonly used types of pumps and operate based on the principle of kinetic energy. These pumps use the rotational movement of an impeller to set liquids in motion. The liquid is pushed outward by centrifugal force from the center of the impeller, leading to acceleration and flow of the liquid. The pump thus enables continuous liquid transport without the use of flaps or valves.
Centrifugal pumps come in radial, semi-axial, or axial designs, where the specific design of the impeller is crucial for the type of application and the liquid to be transported. Energy transfer occurs exclusively through flow-mechanical processes, meaning that the medium freely flows through the pump, and in a stationary state, backflow of the liquid is possible. To prevent this, sliders, valves, or check valves may be required depending on the application.
A significant aspect of centrifugal pumps is that they are not self-priming. Therefore, the suction line must always be filled with liquid, or a sufficient volume of liquid must be present before the impeller to ensure operation. The maximum suction height of the pump is limited by the local air pressure and any flow resistances.
Centrifugal pumps are virtually maintenance-free due to their simple pump system, which leads to low operating costs. They are used in a variety of applications, including wastewater technology, chemical and pharmaceutical industries, domestic installations, cooling circuits, food industry, and swimming pool technology. Due to their efficiency in transporting large quantities of liquid at relatively low pressures, centrifugal pumps are ideal for water distribution and machine cooling.
The pumps should not be throttled on the suction side during operation as this can lead to cavitation and damage to the impeller blades.
Axial Pumps
Function: Axial pumps transport the medium parallel to the pump shaft, enabling very efficient and uniform delivery. They are classified as flow pumps and utilize pressure differences created by the fluid's movement.
Application: Axial pumps are particularly used where high flow rates at relatively low pressure are needed, such as in irrigation systems, drainage, and large cooling systems.
Advantages:
- High flow rates.
- Gentle handling of sensitive liquids.
- Simple construction, resulting in low maintenance requirements.
Disadvantages:
- Low efficiency at high-pressure requirements.
- Susceptible to cavitation under non-optimal operating conditions.
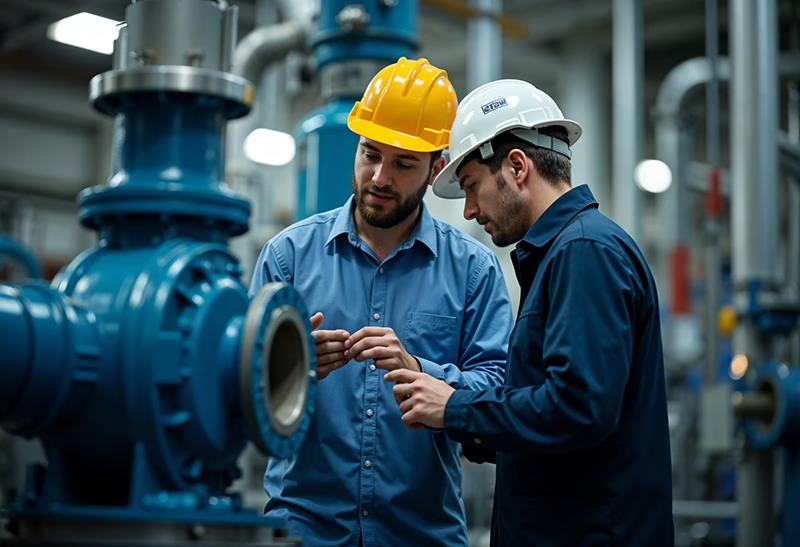
Diagonal Pumps
Function: Diagonal pumps combine features of axial and radial pumps by discharging the medium diagonally to the pump shaft from the impeller. This allows for flexible adjustment of the pump's performance between pressure and flow rate.
Application: They are used in applications requiring both high flow rates and moderate pressure, such as in industrial cooling circuits and water treatment.
Advantages:
- Adjustable delivery characteristics.
- Efficient across a wide operating range.
- High flexibility in application.
Disadvantages:
- More complex construction compared to pure axial or radial pumps.
- Potentially higher costs for acquisition and maintenance.
Radial Pumps
Function: Radial pumps transport the medium radially, i.e., perpendicular to the pump shaft, using centrifugal force to increase the pressure in the medium.
Application: These pumps are commonly used in water supply systems, heating systems, and industrial processes requiring high delivery pressure at lower flow rates.
Advantages:
- High pressure generation at low flow rates.
- Robust and proven technology.
- Versatile for various media and pressure requirements.
Disadvantages:
- Lower efficiency at high flow rates.
- Possible sensitivity to abrasive materials in the medium.
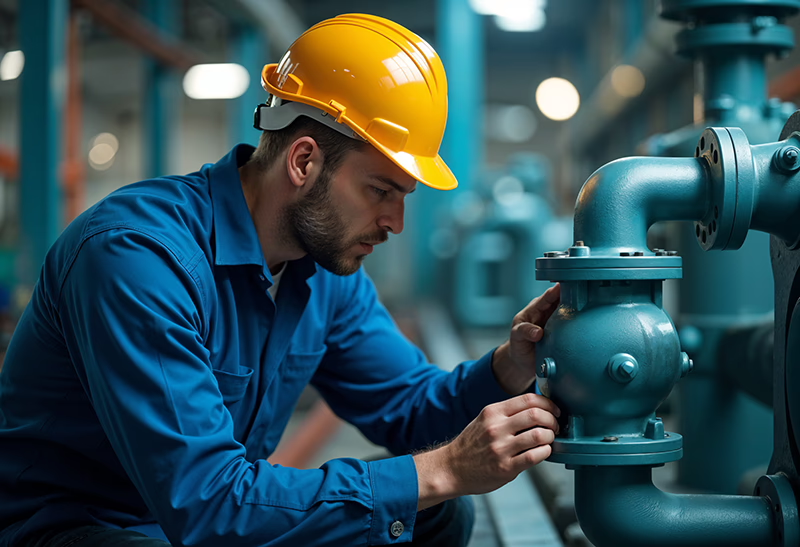
Peripheral Pumps (Turbine Pumps)
Function: Peripheral pumps generate a flow that transports the medium in a peripheral ring channel, enabling high pressure generation at low flow rates.
Application: Particularly suitable for applications with small flow rates and high-pressure requirements, such as in precision engineering or the chemical industry.
Advantages:
- High delivery pressure in a compact design.
- Suitable for media with low flow rates.
- Efficient delivery of liquids with low gas content.
Disadvantages:
- Not suitable for highly viscous or abrasive liquids.
- Limited flow rates compared to other pump types.
Side Channel Pumps
Function: Side channel pumps operate by generating a flow in a lateral channel that draws and compresses the medium into the pump.
Application: These pumps are used in applications requiring self-priming capability, such as condensate pumping, water treatment, and gas compression.
Advantages:
- Self-priming, simplifying startup.
- Low pulsation during operation.
- Can transport liquids with gas content.
Disadvantages:
- Not suitable for highly viscous or abrasive liquids.
- Limited flow rate and pressure compared to other pump types.
Magnetic Coupling Pumps
Function: Magnetic coupling pumps use a magnetic coupling to drive the pump without direct mechanical connection, preventing leaks.
Application: They are used in critical applications such as in the chemical industry, high-temperature processes, and nuclear facilities where no leakage can be tolerated.
Advantages:
- High operational safety due to leak-proof design.
- Suitable for aggressive and hazardous media.
- Long service life due to reduced mechanical wear.
Disadvantages:
- Higher acquisition costs compared to conventional pumps.
- Limited load capacity of the magnetic coupling, which may restrict application possibilities.
Impeller Pumps
Function: Impeller pumps use flexible blades that adapt to the pump housing and move the transport medium. They are self-priming and particularly gentle with sensitive liquids.
Application: Mainly used in cooling boat engines, food processing, and other applications requiring gentle transport without high pressure requirements.
Advantages:
- Self-priming, facilitating handling.
- Gentle transport of sensitive media.
- Easy maintenance and replacement of the impellers.
Disadvantages:
- High wear during dry operation.
- Relatively low efficiency due to high friction in the housing.
- Prone to damage during prolonged dry operation.
Turbomolecular Pumps
Function: Turbomolecular pumps create molecular flow to transport gases in vacuum applications. They operate at extremely high rotational speeds to accelerate gas particles toward the fore-vacuum.
Application: These pumps are used in applications with extremely high vacuum requirements, such as in the semiconductor industry, research laboratories, and nuclear physics.
Advantages:
- Very high vacuum performance.
- Precise and controlled gas transport.
- Low risk of contamination in the vacuum system.
Disadvantages:
- Highly sensitive to high fore-vacuum pressure or atmospheric pressure.
- High cost and complex maintenance.
- Requires a good fore-vacuum for operation.
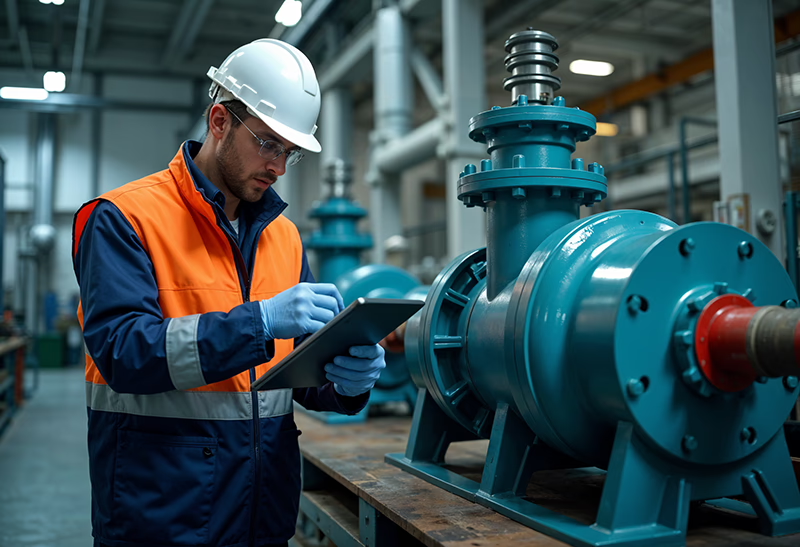
Displacement Pumps
Displacement pumps are a specific type of pump that transports liquids through a closed volume. Their operating principle is based on the fact that a working chamber within the pump is filled with liquid and then mechanically reduced in size. This movement creates pressure on the liquid and pushes it into the pipeline. Subsequently, the working chamber expands again, allowing it to be refilled with liquid from the line.
A key feature of displacement pumps is their ability to self-prime. This means they can pump liquids without external assistance while building up sufficient negative pressure to draw the medium. This property makes them particularly versatile, as they can also pump gases for a limited time.
Displacement pumps are designed to prevent backflow of the transported medium. This is achieved using valves, flaps, or gravity. In a stationary state, the medium cannot flow back through the pump unless there are construction-related leaks.
The pumps can be divided into constant and adjustable pumps. Constant pumps displace the same volume with each revolution, while adjustable pumps can alter the displacement volume. Additionally, displacement pumps can be categorized into rotary and oscillating pumps based on their delivery principle.
Another important characteristic of displacement pumps is their independence from delivery height. They deliver a constant flow rate at a constant speed, regardless of the height to which the medium must be transported. This makes them particularly suitable for applications requiring precise delivery of high-viscosity liquids or media containing solids.
Displacement pumps should not be blocked on the pressure side unless safety measures such as slip clutches or pressure relief valves are installed. Otherwise, the pump, drive, or pipelines could be damaged. The maximum suction height of a displacement pump is limited by the achievable vacuum, local air pressure, the density of the medium, and the flow resistance to be overcome.
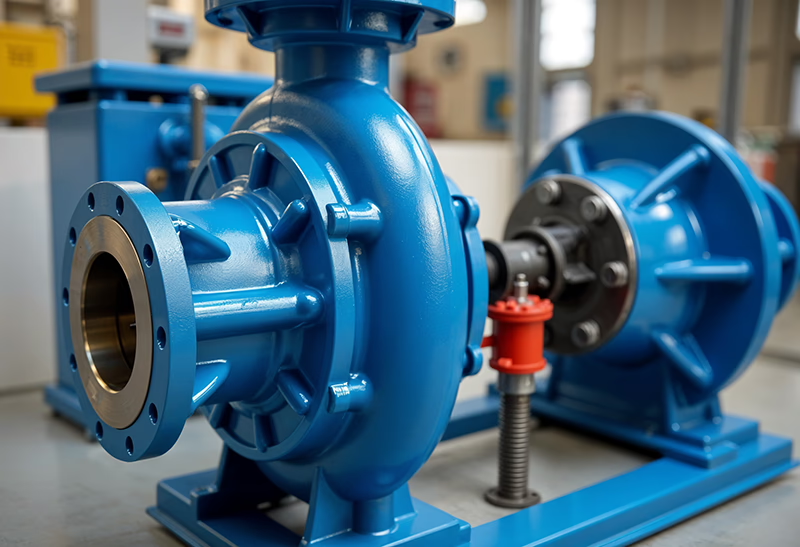
Piston Pumps
Function: Piston pumps operate with one or more pistons moving back and forth within a cylinder. This cyclical movement draws the medium in and pushes it out through the outlet.
Application: Widely used in hydraulic systems, agriculture for irrigation, and in the chemical industry for pumping aggressive liquids.
Advantages:
- High-pressure buildup possible.
- Suitable for abrasive and corrosive media.
- Easy pressure regulation.
Disadvantages:
- Higher sensitivity to solid particles in the medium.
- Periodic maintenance required due to wear parts.
Diaphragm Pumps
Function: Diaphragm pumps use a flexible diaphragm driven by mechanical or pneumatic means to pump the medium. The diaphragm separates the pumped medium from the drive mechanism.
Application: Particularly suitable for pumping abrasive, corrosive, and viscous liquids; often used in the chemical industry and water treatment systems.
Advantages:
- High resistance to chemical and abrasive effects.
- Self-priming and safe to run dry.
- Suitable for highly viscous media and applications with gas content.
Disadvantages:
- Limited delivery pressure compared to piston pumps.
- Possible diaphragm fatigue, leading to failures.
Piston Diaphragm Pumps
Function: A combination of piston and diaphragm pump technology, where a piston moves the diaphragm, allowing the medium to be pumped. This enables pressure-stable and leak-tight delivery.
Application: Commonly used in the chemical industry and high-pressure applications requiring the transport of abrasive or corrosive media.
Advantages:
- High efficiency.
- Low leakage rate due to the diaphragm.
- Suitable for high pressures and abrasive media.
Disadvantages:
- More complex construction, leading to higher costs.
- Regular maintenance required to prevent diaphragm wear.
Wobble Plate Pumps
Function: These pumps use a ring-shaped piston that moves in a wobbling motion within a spherical working chamber to transport the medium.
Application: Used in applications requiring pulsation-free delivery, especially when transporting viscous or sensitive liquids.
Advantages:
- Even flow without pulsations.
- Suitable for viscous media.
- High operational safety.
Disadvantages:
- Higher construction effort and associated costs.
- Susceptible to wear when handling abrasive media.
Peristaltic Pumps
Function: Peristaltic pumps move the pumped medium through an elastic hose deformed by rollers or sliding pieces. The medium is transported through peristaltic movement.
Application: Particularly suitable for use in the chemical industry, medical technology, and laboratory applications where contamination-free delivery is necessary.
Advantages:
- No direct contact between the medium and mechanical parts.
- Self-priming and safe to run dry.
- Easy to clean and maintain.
Disadvantages:
- High wear on the hose during continuous use.
- Limited flow rates and pressures.
Screw Pumps (Progressive Cavity Pumps - PCP)
Function: Screw pumps transport the medium using a rotating screw within a fixed housing. This creates a continuous and even flow.
Application: Ideal for highly viscous, abrasive, or sensitive media such as sludges, crude oil, slurry, or food.
Advantages:
- Constant, even flow.
- High pressure stability.
- Suitable for abrasive and viscous media.
Disadvantages:
- High wear when handling abrasive media.
- Larger construction and higher energy consumption.
Air-Operated Diaphragm Pumps
Function: These pumps use compressed air to move two flexible diaphragms that pump the medium. The diaphragms work alternately to draw in and expel the medium.
Application: Commonly used in the chemical and petrochemical industries, particularly for pumping aggressive or viscous media.
Advantages:
- High chemical resistance.
- Explosion-proof design possible.
- Easy control through compressed air.
Disadvantages:
- Limited efficiency.
- Loud operation and high air consumption.
Bellows Pumps
Function: Bellows pumps work with a flexible bellows that is deformed by mechanical action to pump the medium. They function similarly to diaphragm pumps but use a bellows instead of a diaphragm.
Application: Used in applications requiring precise dosing of small amounts, such as in medical technology or laboratories.
Advantages:
- Simple construction.
- High chemical resistance.
- Low maintenance requirements.
Disadvantages:
- Limited flow rates.
- Bellows wear during intensive use.
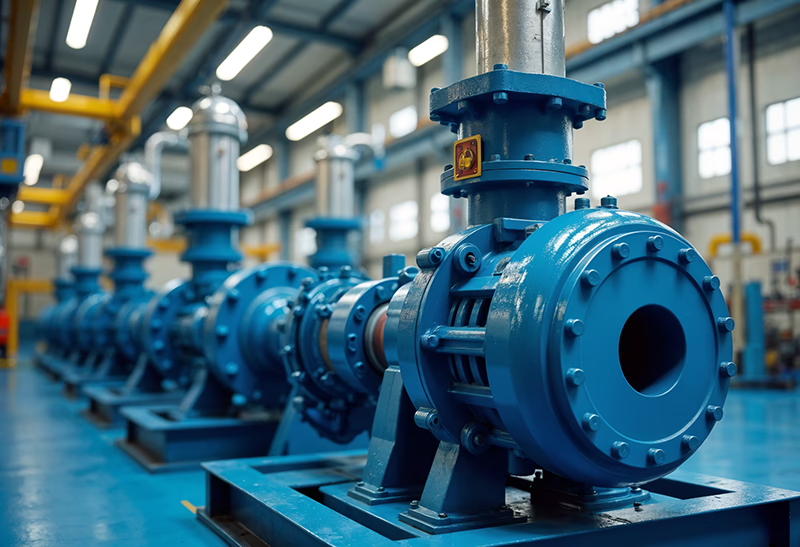
Rotary Lobe Pumps
Function: Rotary lobe pumps use rotating lobes to transport the medium between the housing and lobes. The lobes move in opposite directions, transporting the medium.
Application: Widely used in the food and chemical industries, particularly for transporting viscous or sensitive liquids.
Advantages:
- High efficiency.
- Gentle transport of the medium.
- Suitable for highly viscous and abrasive media.
Disadvantages:
- Susceptible to solids in the medium.
- Regular maintenance required to minimize lobe friction.
Rotary Vane Pumps
Function: Rotary vane pumps use rotating vanes within a cylindrical housing to pump the medium. The vanes seal the pumped medium and move it forward.
Application: Commonly used in vacuum systems, air conditioning technology, and the automotive industry.
Advantages:
- Very good efficiency.
- High vacuum performance.
- Robust and durable.
Disadvantages:
- Sensitive to contamination and solids.
- Regular lubrication required.
Circumferential Piston Pumps
Function: These pumps work with rotating pistons that operate within a circular housing, enclosing and pumping the medium.
Application: Mainly used in the food and chemical industries where sensitive or highly viscous media need to be pumped.
Advantages:
- High flow rate and even flow.
- Gentle transport, ideal for sensitive media.
- Good efficiency with viscous liquids.
Disadvantages:
- More complex construction leading to higher costs.
- Susceptible to abrasive media.
Gear Pumps
Function: Gear pumps operate with two or more gears that mesh together, displacing and moving the medium through the gear teeth.
Application: Widely used in hydraulic systems, lubrication technology, and the chemical industry.
Advantages:
- High precision and delivery accuracy.
- Robust and durable construction.
- Suitable for highly viscous media.
Disadvantages:
- Sensitive to solids in the medium.
- Noisy at high speeds.
Archimedean Screw (Screw Conveyor)
Function: Archimedean screws use a rotating screw to move the medium along the screw axis. They are particularly suitable for pumping liquids and sludges.
Application: Used in agriculture, wastewater treatment, and the food industry.
Advantages:
- Very robust and simple construction.
- Large flow rates possible.
- Suitable for abrasive media.
Disadvantages:
- High space requirement due to design.
- Lower pressure generation compared to other pump types.
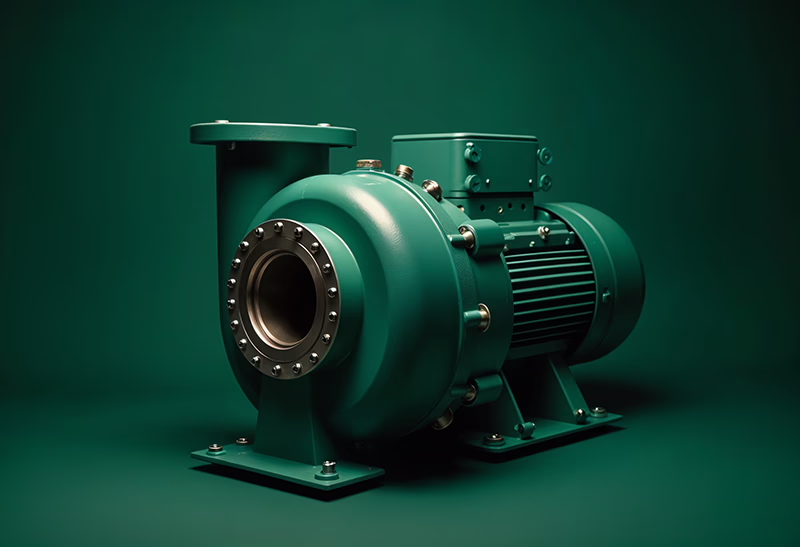
Axial Piston Pumps
Function: Axial piston pumps operate with several pistons arranged parallel to the drive shaft. These pistons are moved by a swashplate to pump the medium.
Application: Mainly used in hydraulic systems and high-pressure applications where precise control and high pressure are required.
Advantages:
- High efficiency.
- High pressure build-up possible.
- Compact design.
Disadvantages:
- Complex construction requires regular maintenance.
- Sensitive to contamination in the medium.
Reciprocating Piston Pumps
Function: Reciprocating piston pumps use one or more pistons that move linearly within a cylinder, displacing the medium through the stroke motion.
Application: Used in water treatment, dosing systems, and hydraulic presses.
Advantages:
- High pressure build-up possible.
- Suitable for viscous and abrasive media.
- Easy pressure regulation.
Disadvantages:
- Susceptible to wear when handling abrasive media.
- Regular maintenance required.
Radial Piston Pumps
Function: Radial piston pumps work with several pistons arranged radially around a central drive shaft. These pistons are set into a stroke motion by the rotation of the shaft, pumping the medium.
Application: Used in hydraulic systems, particularly where high pressure and uniform delivery are required.
Advantages:
- Very high pressure performance.
- Low pulsation in the delivery flow.
- High efficiency.
Disadvantages:
- High maintenance effort due to complex construction.
- Sensitivity to solids in the medium.
Ring Piston Pumps
Function: Ring piston pumps use an eccentrically mounted piston that rotates within a ring-shaped housing to pump the medium.
Application: Used in applications requiring uniform and pulsation-free delivery, such as in the food and chemical industries.
Advantages:
- Uniform delivery without pulsations.
- Suitable for viscous and sensitive media.
- Compact design.
Disadvantages:
- Higher wear when handling abrasive media.
- More complex maintenance due to special design.
Screw Spindle Pumps (Screw Pumps, Helical Piston Pump, or Screw Compressors)
Function: Screw spindle pumps work with two or more rotating screw spindles that pump the medium along the spindle axes.
Application: Frequently used in the oil and gas industry, chemicals, and the food industry.
Advantages:
- Very high flow rates.
- High pressure stability.
- Suitable for viscous and abrasive media.
Disadvantages:
- Complex construction leads to higher maintenance costs.
- High energy consumption for large flow rates.
Sinusoidal Pumps
Function: Sinusoidal pumps use a sinusoidal curve as a rotating element to enclose and transport the medium in chambers, providing gentle and pulsation-free delivery.
Application: Particularly suitable for the food industry, cosmetics, and chemical processes where gentle handling is important.
Advantages:
- Pulsation-free delivery.
- Gentle handling of sensitive media.
- High efficiency with viscous media.
Disadvantages:
- Higher acquisition costs.
- Sensitivity to abrasive particles.
Toothed Belt Pumps
Function: Toothed belt pumps use a toothed belt guided over pulleys to transfer mechanical energy and move the pumping medium. These pumps operate similarly to gear pumps, but the movement is enabled by a flexible toothed belt rather than rigid gears.
Application: Toothed belt pumps are primarily used in applications where water needs to be pumped or air needs to be moved through a water channel, such as in water treatment, cooling circuits, or special industrial applications requiring flexible pumping solutions.
Advantages:
- Flexibility in positioning and installation due to the flexible toothed belt.
- Lower wear compared to rigid gears, as the belt is elastic and better absorbs shocks.
- Quieter operation compared to rigid gear mechanisms.
Disadvantages:
- Limited flow rates and pressures compared to other pump types.
- Higher maintenance requirements as the toothed belt must be regularly checked for tension and wear and replaced if necessary.
- Potential slippage under heavy load or poorly tensioned belts, which can affect pumping performance.
Shaker Pumps
Function: Shaker pumps, also known as vibration or hand pumps, operate through manual shaking movements. This movement creates a vacuum that draws the medium in and transports it through a simple valve technique.
Application: Often used for transferring small quantities of liquids, such as in household technology, workshops, or outdoor activities to transfer liquids from one container to another.
Advantages:
- Simple and inexpensive construction.
- No external power source required, as they are manually operated.
- Lightweight and portable, ideal for use on the go or in emergencies.
Disadvantages:
- Limited flow rate and delivery height.
- Not suitable for viscous or abrasive media.
- Fatiguing over extended use, as they must be manually operated.
Horsehead Pump (Submersible Pump)
Function: Horsehead pumps, also known as submersible pumps, use a mechanical lever arm to move a piston deep in the ground to pump liquids.
Application: Mainly used in the oil industry to extract crude oil from great depths.
Advantages:
- Effective pumping from great depths.
- Robust and durable construction.
- High-pressure build-up possible.
Disadvantages:
- Low flow rates compared to other pump types.
- High maintenance effort due to mechanical stresses.
Chain Pumps
Function: Chain pumps operate with an endless chain to which buckets or pistons are attached, transporting the medium upward.
Application: Used in agriculture for irrigation and in the mining industry for drainage.
Advantages:
- Simple and robust construction.
- Suitable for transporting liquids with solid content.
- High operational safety.
Disadvantages:
- Limited flow rate and height.
- High maintenance effort during continuous use.
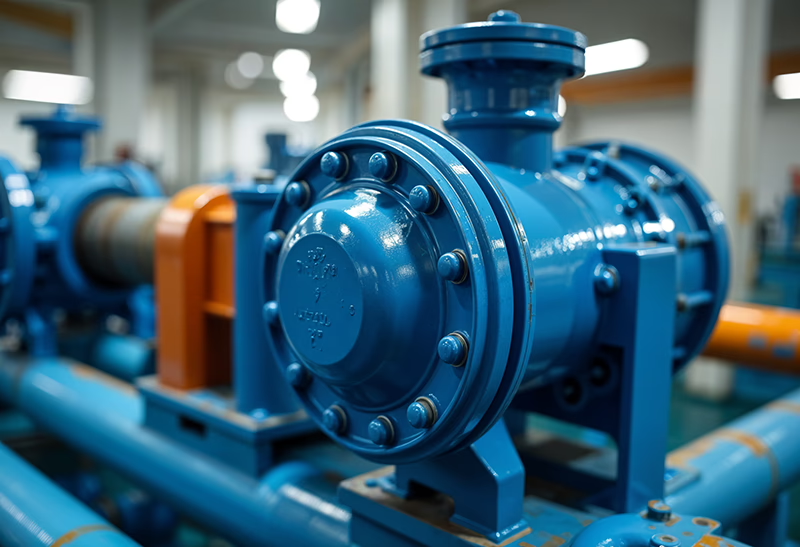
Other Designs
Jet Pumps
Jet pumps are characterized by the fact that they accelerate the pumped medium through a gas, steam, or liquid jet. Although they use fluid dynamics, they are often classified as displacement pumps. This type of pump is useful in various applications depending on the type of jet used.
Water Jet Pump
Function: The water jet pump uses a water jet to pump air or other liquids. The movement of water creates a vacuum that draws the medium to be pumped.
Application: These pumps are often used for extracting liquids, creating a vacuum in laboratories, venting tanks, and similar applications where a simple and robust pumping system is needed.
Advantages:
- No moving parts, resulting in less wear.
- Simple construction and low maintenance costs.
- Can be used in environments with explosive or aggressive media since no electrical components are needed.
Disadvantages:
- Relatively low efficiency, as a large part of the energy is lost in the driving jet.
- Requires a constant and sufficient water pressure to work effectively.
Steam Jet Pump
Function: A steam jet pump uses high-pressure steam to pump air, water, or other gases. The steam jet creates a vacuum that draws in the pumped medium.
Application: Steam jet pumps are often used in steam power plants and steam locomotives, particularly as feed pumps for steam generators. They are also used in chemical processes requiring high vacuum.
Advantages:
- High resistance to aggressive media.
- No moving parts, simplifying maintenance.
- Can operate at very high temperatures.
Disadvantages:
- High energy consumption due to the required steam pressure.
- High water consumption if condensers need to be used.

Additional Pump Principles and Exotic Designs
Besides jet pumps, other pump types utilize unique principles. These designs often rely on specific physical properties of the pumped medium or the environment and are used in niche applications.
Airlift Pump (Bubble Pump)
Function: The airlift pump uses rising gas bubbles to transport liquids. The gas (usually air) is introduced into the liquid, and the rising bubbles pull the liquid upwards.
Application: This pump is often used for pumping liquids with solid content, such as in the mining industry or dewatering construction sites.
Advantages:
- Can transport solid-laden liquids without clogging the pump.
- No moving parts in the pumped medium, reducing maintenance.
Disadvantages:
- Relatively low efficiency.
- Limited delivery height, dependent on gas volume and bubble size.
Hydraulic Ram
Function: The hydraulic ram uses the kinetic energy impulse of a flowing water quantity to pump a smaller amount of water to a higher level.
Application: Typically used for water pumping in rural areas where continuous water flow is available, such as from a stream or river.
Advantages:
- No external power source needed, just flowing water.
- High reliability and long lifespan.
Disadvantages:
- Relatively low efficiency (only a small portion of the flowing water is pumped).
- Works only with sufficient and constant water flow.
Ion Getter Pump (Sorption Pump)
Function: An ion getter pump uses an electric field to extract ions from a gas and adsorb them onto a surface, removing the gas from the space.
Application: These pumps are widely used in high vacuum technology, particularly in semiconductor manufacturing, research laboratories, and particle physics.
Advantages:
- Very high vacuum performance.
- No moving parts, making it extremely durable.
- Operates in extreme environments, such as space.
Disadvantages:
- High costs and complicated installation.
- Requires special materials and surfaces for adsorption.
Titanium Sublimation Pump
Function: The titanium sublimation pump evaporates (sublimates) titanium, which then deposits on surfaces and chemically binds gases like hydrogen or oxygen, improving the vacuum.
Application: These pumps are often used in combination with other vacuum pumps in high vacuum technology, especially in metallurgy and vacuum tube manufacturing.
Advantages:
- High efficiency in removing residual gases in a vacuum system.
- Relatively simple technology compared to other high vacuum pumps.
Disadvantages:
- Works only at very low pressures (high vacuum).
- Consumption of titanium material, which must be regularly replenished.
Electrochemical Gas Pump
Function: The electrochemical gas pump uses electrochemical reactions to transport gases such as oxygen or hydrogen. It is based on the conversion of electrical energy into chemical energy and vice versa.
Application: Used in fuel cell technology, gas analysis, or medical technology for controlled gas pumping.
Advantages:
- High precision in gas transport.
- Can dose small amounts of gas very accurately.
- Compact and energy-saving.
Disadvantages:
- Complex control and high manufacturing costs.
- Sensitive to contamination in the gas.
Types of Pumps by Application

- Suction Pump: Removes liquids or gases from a container or system.
- Sewage Pump: Pumps sewage, typically in sewers or treatment plants.
- Barostat in Neuro-Gastroenterology: Controls pressure in the gastrointestinal tract to investigate functional disorders.
- Artificial Blood Pump: Supports or replaces heart function to maintain blood circulation.
- Drill Pump: Used in drills for small amounts of liquid delivery.
- Dosing Pump: Precisely delivers and doses liquids or chemicals in controlled amounts.
- Injection Pump (Gasoline, Diesel): Injects fuel into the combustion chamber of an engine for combustion.
- Barrel Pump: Extracts liquids from barrels, typically for chemical or industrial applications.
- Fire Fighting Pump: Provides water or extinguishing agents under high pressure for firefighting.
- Manure Pump: Transports liquid manure in agricultural applications.
- Hand Pump: Manually pumps liquids, often in emergencies or simple systems.
- Hydraulic Pump: Generates hydraulic pressure to operate machines or hydraulic systems.
- Boiler Feedwater Pump: Supplies water to steam boilers in power plants or industrial applications.
- Fuel Pump: Transports fuel from the tank to the engine in vehicles or machines.
- Cooling Water Pump: Circulates cooling water for heat dissipation in engines or industrial systems.
- Bilge Pump: Pumps water out of ship hulls or boats.
- Air Pump: Compresses and pumps air, often in tires, ventilation systems, or for tools.
- Micropump: Used in microfluidic systems for small flow rates, e.g., in medical applications.
- Oil Pump: Circulates lubricating oil in engines or machines to reduce friction and wear.
- Pipeline Pump: Pumps oil, gas, or other liquids over long distances through pipelines.
- Acid Pump: Specifically designed for transporting aggressive chemicals like acids.
- Dirty Water Pump: Pumps heavily contaminated water with solids, often in construction or wastewater applications.
- Syringe Pump: Precisely doses and delivers liquids in medical or laboratory applications.
- Rinse Pump: Used in sanitary systems or medical devices for cleaning or rinsing.
- Tandem Pump: Combines two or more pumps for higher performance or redundancy.
- Submersible Pump: Operates fully submerged in liquid, often for drainage or wells.
- Circulation Pump (General): Circulates liquids in closed circuits, e.g., in heating systems.
- Water Pump: General pump for transporting water in various applications.
- Vacuum Pump: Generates a vacuum, often for industrial processes or laboratory applications.
- Dosing Pumps: Precisely delivers chemicals, liquids, or gases in controlled amounts.
- Stainless Steel Pumps: Pumps made of stainless steel for use in corrosive or hygienic environments.
- Water Pumps: General category of pumps for transporting water, often in households, agriculture, or industry.
- Garden Pumps: Water pumps for use in garden irrigation systems or for pumping rainwater.
- Pumping Stations: Large pumping systems for draining areas or transporting water in canals.
- Pneumohydraulic Pressure Intensifier (Pressure Multiplier): Increases hydraulic pressure in systems through pneumatic assistance, often used in hydraulic controls.
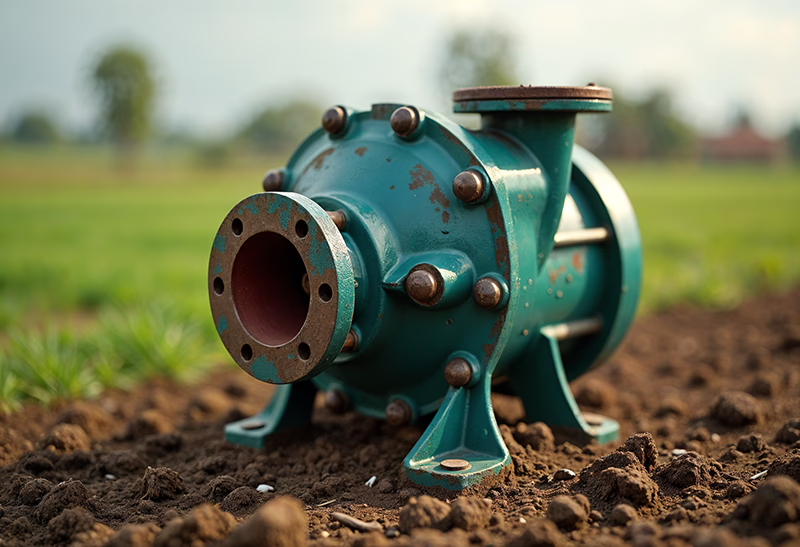
Important Technical Parameters for Pumps
When operating pumps, certain technical parameters are crucial for performance and efficiency. The most important parameters include the delivery pressure, flow rate, net positive suction head (NPSH), and other specialized values.
Delivery Pressure
The delivery pressure describes the pressure the pump must generate to move the pumped medium through the pipeline system. The delivery pressure depends on the delivery height, the viscosity of the medium, and the characteristics of the pipe system. Higher delivery pressure is required when the medium must be transported over greater heights or through complex pipe systems.
Flow Rate
The flow rate indicates the volume of a medium that the pump can move per unit of time. It is typically measured in liters per minute (l/min) or cubic meters per hour (m³/h). This parameter depends on the pump's design, motor speed, and the properties of the pumped medium.
Net Positive Suction Head (NPSH)
The net positive suction head (NPSH) is a critical parameter that indicates the minimum pressure head above the saturation pressure of the pumped medium required to avoid cavitation. Cavitation, the formation and collapse of vapor bubbles, can cause severe damage to the pump.
NPSH is divided into two essential values:
- NPSH(R) (Required): This is the minimum pressure specified by the manufacturer that is required at the suction side of the pump to prevent cavitation.
- NPSH(A) (Available): This is the actual pressure available in the system to supply the pump with the pumped medium.
To avoid cavitation, the NPSH(A) value must always be higher than the NPSH(R) value. In practice, this means that the suction capacity of the system must be carefully designed to ensure the pump operates smoothly.
Importance of NPSH in Various Applications
The NPSH value plays a central role in various industries:
- Shipbuilding: Here, avoiding cavitation is essential to protect both the pumps and the ship's structure.
- Power Plants: In steam power plants, the NPSH value must be maintained under extreme temperature conditions to protect the pumps from cavitation.
- Chemical Industry: Especially in processes under vacuum, precise NPSH calculation is crucial to ensure the smooth operation of pump systems.
Frequently Asked Questions About Pumps
What are the differences between pumps and fans?
Pumps and fans primarily differ in the medium they move and their application. Pumps transport liquids, while fans move air or gases. Pumps generate higher pressure and are suitable for applications such as water or oil transportation. Fans, on the other hand, mainly generate airflow and are used for ventilation or cooling. Another difference is that pumps often operate in closed systems, while fans ventilate open systems.
What are the differences between pumps and compressors?
Pumps and compressors differ in the type of medium and pressure increase. Pumps transport liquids (such as water or oil) and increase the pressure of these liquids. Compressors, on the other hand, compress gases and significantly increase their pressure. Pumps are mostly found in hydraulic systems, while compressors are used in pneumatic systems. Compressors are generally designed for higher pressure ratios than pumps.
What are the differences between pumps and blowers?
Pumps and blowers differ in their function and application. Pumps move and transport liquids, while blowers compress gases and increase their pressure. The main difference lies in handling the media: pumps work with incompressible liquids, while blowers handle compressible gases. Blowers are a specialized type of compressor designed specifically for high-pressure ratios.
How do you check pumps for functionality?
To check the functionality of pumps, proceed as follows:
- Visual Inspection: Check the housing for leaks or damage.
- Pump Noises: Listen for unusual noises during operation.
- Pressure and Flow Measurement: Measure the output pressure and flow to ensure they meet specifications.
- Electrical Check: Inspect the motor for proper current flow and overheating.
- Vibrations: Check for unusual vibrations that may indicate a mechanical problem.
What should you do if air is present in the pump hydraulics?
If air is present in the pump hydraulics, you should bleed the pump. Turn off the pump, open the bleed valves, and allow the air to escape until only liquid comes out. Then close the valves and restart the pump. Air in the hydraulics can significantly impair the pump's performance and lead to cavitation.
Can a dirty water pump run in reverse?
Yes, a dirty water pump can theoretically run in reverse if the electrical wiring is incorrect, leading to a reversal of the rotation direction. However, this can drastically reduce the pump's efficiency or even cause damage. Check the motor's direction of rotation and ensure it is correct.
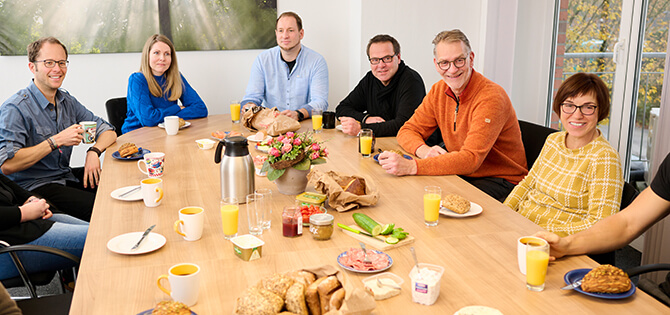
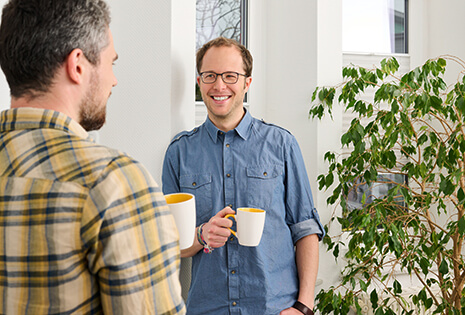
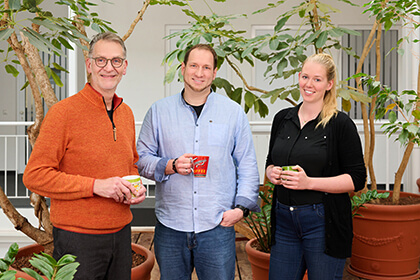
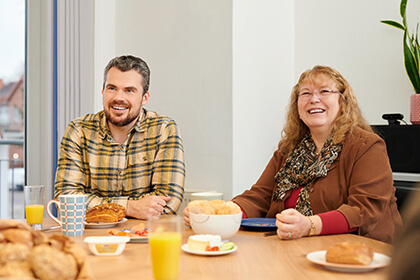
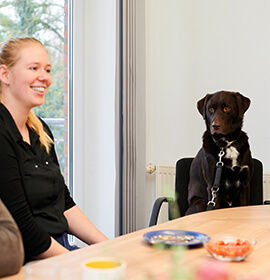
Are you an engineer or designer looking for new challenges? With us you can expect a familiar atmosphere and exciting tasks!
View Job Ads Now!