What Are Compressed Air Systems?
A compressed air system is a technical device that compresses air to a higher pressure than atmospheric pressure and makes it available for various applications. It makes it possible to generate, store, transport and release compressed air when needed. Compressed air systems are an essential part of the technical supply infrastructure in industry.
A compressed air system consists of several components that work together to provide compressed air. Important areas of application include use in compressed air tools, pneumatic drives and in process plants that require compressed air.
Compressed air is often used to perform mechanical work or to control machinery. These systems can be found in almost all manufacturing companies and play a central role in industrial production.
Why Are Compressed Air Systems So Important?
Compressed air has established itself as a universally applicable energy source in numerous industrial sectors and offers a wide range of applications:
- Drive tools and machines: Many tools, such as pneumatic drills, grinders and riveting tools, work more efficiently with compressed air. These systems offer high performance and reliability, resulting in increased productivity.
- Control and regulation technology: Compressed air systems are crucial in automation. They perform control and regulation tasks, such as in pneumatic actuators, which enable precise movements. This makes them particularly valuable in production environments where accuracy and efficiency are important.
- Cleaning processes: compressed air is often used for cleaning purposes, particularly in areas where traditional cleaning methods are not applicable. It can remove dust and dirt from machines, workpieces and surfaces quickly and thoroughly.
Another aspect that makes compressed air systems so important is their efficiency and reliability. They are known for allowing long operating times without major maintenance. This directly contributes to maximizing productivity in production processes and thus supporting the economic success of your company.
Physical Properties of Compressed Air
Compressed air is a compressed form of atmospheric air whose physical properties are closely related to pressure and volume. The most important physical properties include:
- Printing: Pressure rises when air is compressed. This is measured in bars or pascals.
- Volume: The higher the pressure, the smaller the volume of compressed air (at a constant temperature).
- Temperature: When the air is compressed, the temperature rises. Cooling systems are therefore often part of compressed air systems.
- Moisture: Air always contains a certain amount of water vapor. When compressed, this moisture is concentrated, which leads to condensation. Therefore, dryers are necessary to remove water from the system and prevent corrosion.
A compressed air system is based on sucking air from the atmosphere and compressing it with a compressor. As a result of compression, the pressure of the air rises while its volume decreases. This follows physical principles, in particular the Boyle-Mariotte law, which states: If the temperature remains constant, the product of pressure and volume remains constant. The sizing of a compressed air system is essential for its efficiency. It must be designed to meet the required compressed air requirement, which is expressed in liters per minute (L/min) or cubic meters per hour (m³/h).
Advantages and Disadvantages of Compressed Air Compared to Other Energy Sources
Advantages:
- Easy transfer of energy: Compressed air can be converted quickly and easily into various forms of mechanical work.
- Flexibility: Compressed air systems can be used for a wide range of applications, whether in industry, in workshops or in the medical sector.
- Surety: Compressed air is non-toxic and can be safely used in humid, explosive, or sensitive environments where electrical or hydraulic systems would be more risky.
- Quick response: Pneumatic systems respond quickly to control commands, making them ideal for applications that require rapid movement.
- Long lifespan: When properly maintained, compressed air systems are durable and reliable.
Disadvantages:
- High energy consumption: Operating compressors requires more energy than other types of drives. As a result, compressed air systems can be more expensive to operate.
- Leakage losses: Leaks in the system lead to significant energy losses and impair profitability.
- Maintenance costs: Compressed air systems require regular maintenance to prevent loss of efficiency and damage due to moisture or contamination.
- High start-up costs: Installing a compressed air system can involve high investment costs.
- Condensation: When air is compressed, the water vapor concentration increases, which can lead to condensate. This condensate can cause corrosion if not adequately removed.
Main Components of a Compressed Air System
The main components of a compressed air system are essential to keep operations smooth, efficient and safe. Each of these components performs a specific function within the system and contributes to the generation, treatment, storage and distribution of compressed air.
Compressors
The compressor is at the heart of a compressed air system by sucking in ambient air, compressing it and thus generating the required pressure for the application. There are different types of compressors, which are selected depending on the application and requirements:
- Reciprocating compressors: These work with a piston, which compresses the air in a cylinder. They are robust and durable, particularly suitable for applications with intermittent operation and higher pressures.
- Screw compressors: Here, the air is compressed between two rotating screws. They are particularly suitable for continuous operation and industrial applications where large volumes of air are required at medium pressure.
- Scroll compressors: These work with two spiral-shaped elements that interlock. They offer quiet and low-vibration compression and are suitable for smaller applications.
- Rotary compressor: In these compressors, compression is carried out by rotating blades or discs. They are ideal for continuous applications as they provide a steady supply of air.
- Turbo compressors: These high-speed compressors use a radial impeller to provide large volumes of air at low to medium pressure. They are often used in large industrial plants.
Selection criteria for the right compressor:
- Air requirement: The amount of compressed air required determines the choice of compressor. Screw compressors are ideal for large, continuous requirements, while reciprocating compressors are suitable for smaller, discontinuous applications.
- Printing requirements: The desired pressure is decisive. Reciprocating compressors are suitable for higher pressures, while screw or scroll compressors are used for medium pressures.
- Energy efficiency: An energy-efficient compressor can reduce operating costs in the long term. Screw compressors are often the most efficient choice for continuous operation.
Compressed Air Treatment Systems: Filters and Dryers
Compressed air filters remove contaminants such as dust, oil, and other particles from compressed air. Clean compressed air protects the following components from wear and failure.
- Prefilter: Remove coarse particles and protect subsequent filter stages.
- Fine filter: Eliminate minor particles and oil vapors.
- Activated carbon filter: Adsorb oil vapors and other hydrocarbons.
Compressed air dryers are necessary to remove moisture from compressed air and prevent corrosion and damage to machines.
- Refrigeration dryer: Cool the air to condense and separate moisture.
- Adsorption dryer: Remove moisture through chemical adsorption and are suitable for extremely dry air.
- Membrane dryer: Use a semi-permeable membrane to separate water molecules and are compact but less effective with high volumes of air.
Compressed Air Tanks and Accumulators
Compressed air tanks are used to store compressed air and provide a buffer that compensates for pressure fluctuations and absorbs peak loads. The size and pressure range of the container depend on the air requirement and the operating pressure of the system. A suitably sized container can extend the life of the compressor by reducing start-up cycles.
Distribution Systems: Compressed Air Lines, Pipes, Hoses and Valves
Distribution systems transport compressed air from compressors and reservoirs to end devices. A well-planned distribution system minimizes pressure losses and prevents leaks, which increases the efficiency of the system.
- Compressed air lines and piping: Made of materials such as steel, stainless steel, aluminum or plastic, they ensure the stable and long-lasting distribution of compressed air.
- Hoses: Flexible cables that are used where mobility or flexibility is required.
- Valves: Used to control the airflow and to regulate the pressure in the pipes.
Control and Regulation Technology
The control and regulation technology monitors pressure and air flow throughout the system. It ensures that the compressor and other components only work when needed, which enables energy savings.
- Pressure regulator keep the desired pressure in the pipes constant.
- Sensors and control devices monitor the system pressure and adjust the compressor output to current requirements, which contributes to the energy efficiency of the entire system.
Maintenance Units
Maintenance units include components such as steam traps and oil-water separation systems, which ensure that the system remains free from unwanted liquids and contaminants. Regular maintenance of these units is critical to maximize the life of the compressed air system and ensure consistently high air quality.
How a Compressed Air System Works
A compressed air system converts mechanical energy into compressed air and makes it available for a wide range of applications. The system essentially consists of the generation, treatment, storage, distribution and control of compressed air.
Compression Process: Production of Compressed Air
The production of compressed air starts with the compression process in a compressor. The compressor sucks in ambient air, compresses it and increases air pressure. The mechanical energy of the drive is converted into compressed air. Depending on application requirements, different pressure levels and flow rates (in bar or psi as well as m³/min or cfm) can be provided.
It is important to note that moisture and dirt particles are sucked in from the ambient air during this compression process. These can influence downstream applications, which is why compressed air treatment is essential.
Compressed Air Storage and Pressure Regulation
After compression, the compressed air generated is stored in compressed air tanks. These containers buffer compressed air to compensate for pressure peaks and ensure a continuous supply. Storage helps relieve the compressor by not having to work constantly, which in turn improves energy efficiency.
The pressure in a compressed air system must be precisely regulated to meet the requirements of the terminal equipment. Pressure regulators perform this task and ensure that the compressed air is available at the desired pressure.
Compressed Air Purification and Treatment
After compression, compressed air often contains contaminants such as oil, dirt particles or moisture. Compressed air is prepared to prevent damage to tools and equipment.
The processing is divided into:
- Filtering: Filters remove suspended solids, oil, and other particles. Depending on the purity requirement, coarse, fine and activated carbon filters are used.
- Drying: Moisture is removed using refrigeration dryers or adsorption dryers. Refrigeration dryers cool the air so that the water condenses and can be removed, while adsorption dryers chemically bind the water.
These processes are necessary to make compressed air of high quality and free from harmful contaminants.
Distribution and Management Systems
The treated compressed air is transported to the end applications through a piping system. Pipelines and hoses play a decisive role here.
Pipelines made of materials such as aluminum, stainless steel or plastic are ideal due to their corrosion resistance and low weight. They should be optimally sized to minimize pressure losses. Flexible hoses are used where mobility is required or connections to terminal devices need to be established.
A well-planned distribution system avoids unnecessary bends and branches that could impede airflow and cause energy loss.
Control and Monitoring of the System
A compressed air system is monitored and regulated by a control unit. This control system dynamically adapts air production to actual demand and thus optimizes energy consumption. Monitoring mechanisms ensure that the operating status of the system is known at all times and that possible faults can be reacted to at an early stage.
Advanced control systems also provide automatic fault diagnostics and energy consumption analyses, which ensure efficient use of the compressed air system.
Compressed Air System Maintenance
Regular maintenance of compressed air systems is essential to ensure their durability and efficiency. A well-maintained compressed air system avoids unnecessary downtime, saves energy and reduces repair costs. In addition to the inspection and replacement of wearing parts, safety precautions play a central role in protecting both the system and the user.
Regular Inspections and Maintenance Plans
The inspections and maintenance of compressed air systems should be based on a clear maintenance plan. Regular tests enable problems to be identified and resolved in good time before they lead to serious faults. Important points include:
- Leakage tests: Check all hoses and pipes regularly for leaks. Even small leaks can cause major energy losses.
- Filter maintenance: Replace air and oil filters regularly to prevent contamination and ensure system efficiency.
- Draining compressed air tanks: Condensation in compressed air tanks and filters can cause corrosion and lead to malfunctions. Dehydrate them regularly to avoid problems.
- Check the oil level: Make sure that the oil level in the compressor is correct. Poor lubrication results in increased wear and inefficient operation.
- Calibration of control and regulation systems: Regular calibration ensures that the compressor is working optimally and that the pressure in the system remains constant.
Typical Faults and How to Fix Them
Typical faults in compressed air systems can lead to expensive failures if they are not identified in time. Some common issues and their solutions include:
- Leakages: They often occur in hoses, connections, and pipelines. Check the connections and replace damaged parts. A leak test can be carried out regularly to minimize undetected losses.
- Pressure loss: A continuous loss of pressure often indicates leaks or clogged filters. Replace the filters and check the system for leaks.
- Compressor overheating: This is often the result of a low oil level or a clogged air or oil filter. Check the oil level and clean or replace the filters.
- Corrosion: Condensation in the system that is not regularly removed leads to corrosion. Make sure that the compressed air tanks are dewatered regularly.
- Inadequate pressure: An insufficient pressure supply may indicate a problem in the control systems. Calibrate the systems regularly and ensure that all components are working properly.
Extend the Life of Components
The lifetime of compressed air systems and their components can be significantly extended by simple measures:
- Regular cleaning: Keep compressors and filters clean to remove dust and contaminants that could affect the system.
- Proper lubrication: Make sure moving parts are lubricated regularly to minimize wear.
- Maintain operating pressures: Never exceed the recommended system operating pressures to avoid unnecessary stress and damage.
- Careful handling of compressed air: Avoid unnecessary energy consumption due to leaks and excessive pressure to increase system efficiency and reduce component stress.
Maintenance Safety Precautions
Safety is paramount when maintaining compressed air systems. Compressed air poses a high risk potential if handled improperly. Therefore, please note the following safety measures:
- Reducing the burden on the system: Before you carry out maintenance, make sure that the compressed air system is completely relieved. In this way, you prevent injuries caused by suddenly escaping compressed air.
- Wearing protective equipment: Always wear the required protective equipment, such as goggles and gloves, to protect yourself from unexpected dangers.
- Check safety valves: The safety valves prevent dangerous overpressure in the system. Check regularly whether they work correctly.
- Emergency outlets: In the event of a pressure drop or overpressure, make sure that there are emergency outlets that safely reduce the pressure.
- Trainings: Make sure that personnel working with the compressed air system receive regular training and are familiar with safety precautions.
By observing these maintenance and safety measures, you ensure the smooth operation of your compressed air system and increase its longevity.
Planning and Design of a Compressed Air System
Planning and designing a compressed air system requires several essential steps to ensure an efficient and reliable plant. A well-thought-out approach helps to minimize energy consumption and control costs while meeting performance requirements.
Identify Requirements and Specifications
The first step is to identify the specific requirements. This includes:
- Method of application: Which machines or tools should be operated with compressed air?
- Air quality: Does the air have to be oil-free, dry or filtered?
- Pressure level: How high must the operating pressure be?
- volumetric flow: How much compressed air is required per minute or hour?
It is important to precisely define all parameters in order to optimally design the system.
Cost Planning and Profitability Analysis
Cost planning is crucial. The following factors must be considered:
- Acquisition costs for compressors, lines, filters and accessories.
- Operating costs such as electricity, maintenance and potential repairs, as compressed air systems are energy-intensive.
- Life cycle costs, including component replacement intervals and downtime.
An economic analysis helps to make the system profitable in the long term.
Calculate Pressure Requirements and Pressure Losses
Pressure requirements and pressure losses are important parameters. You must determine the actual pressure requirement of all devices and consider the following points:
- Printing requirements: Calculate the pressure that each device requires.
- Pressure losses: They are caused by flow resistances in pipes, filters and connections. These losses should be minimized, for example due to smooth pipes and short distances.
Dimensioning of Cables and Components
The dimensions of pipes and components such as filters, dryers and compressors are crucial:
- Pipe diameter: Lines that are too small cause high pressure losses; oversized pipes unnecessarily increase costs.
- Material of the pipes: Aluminum or plastic are lightweight and corrosion-resistant, steel is suitable for robust applications.
- Compressor: Select the compressor according to pressure and volume requirements. Energy efficiency is particularly important here, as the compressor consumes the majority of the energy.
Safety Aspects
Safety aspects are also important:
- Overpressure protection: Install safety valves that open when there is dangerous pressure.
- Leakage monitoring: Leaks lead to pressure losses, which is why detection systems are helpful.
- Safety sign: All components should be correctly marked.
- Noise protection: Provide protective equipment and soundproofing measures.
Through careful planning, you can implement an efficient, safe and economical compressed air system.
Energy Efficiency of Compressed Air Systems
Compressed air systems are widely used in industrial production, but they are among the most energy-intensive applications. The efficiency of a compressed air system can be significantly increased, resulting in high cost savings and a reduced environmental footprint. Optimizing compressors, reducing leaks and recovering waste heat are some of the most effective measures to reduce energy consumption.
Causes of Energy Loss
Energy losses in compressed air systems are often due to several factors:
- Leakages: Leaks are one of the biggest sources of energy loss in compressed air systems. They can consume up to 30% of the compressed air volume generated without being used productively.
- Oversized compressors: When compressors are too large for actual use, the system runs inefficiently and uses an unnecessary amount of energy.
- Pressure losses: Inadequate piping or poorly designed compressed air distributions can cause significant pressure losses.
- Inadequate maintenance: Unmaintained filters or valves result in additional energy losses and reduce system performance.
Energy Saving Potential
Reducing energy consumption in compressed air systems offers significant savings potential:
- Using efficient compressors: Compressors with high performance efficiency and speed-controlled drives adapt energy consumption to actual requirements, thus saving up to up to 35% of energy costs.
- Optimized compressed air distribution: An intelligent compressed air distribution design reduces pressure losses and prevents unnecessary energy consumption.
- Leakage prevention: Eliminating leaks can save up to 20% of the total energy costs of a compressed air system.
- Use of energy management systems: Automated controls that adapt compressor operation to real requirements increase efficiency and reduce energy losses.
Heat Recovery in Compressed Air Systems
When compressing air, compressors generate significant amounts of heat, which often remains unused. Efficient heat recovery can make this energy usable, for example for heating purposes:
- Up to 93% of the energy, which is consumed by a compressor, is released in the form of heat. This heat can be used through suitable recovery systems to heat water or to heat buildings, which further reduces energy costs.
- The use of heat exchangers makes it possible to feed waste heat directly into heating systems or water heaters.
Detect and Fix Leaks
Leaks are one of the main causes of energy loss in compressed air systems. Regular inspection and rapid repair of leaks is therefore essential:
- Leakage detection: With the help of ultrasonic detectors, leaks are easy to detect, so even the smallest leaks can be detected.
- Eliminate leaks: Defective seals, pipe connections, or valves should be repaired or replaced immediately. Regular maintenance intervals prevent leaks from recurring.
- Monitoring systems: The use of compressed air monitoring systems helps to continuously monitor air pressure and flow rate and to identify abnormalities at an early stage.
Consistent care and maintenance of compressed air systems not only prevents energy losses, but also ensures stable and efficient operation.
Compressed Air Quality
The quality of compressed air plays a decisive role in numerous industrial processes that use compressed air systems. It relates to the degree of purity of air and is largely determined by the content of impurities such as particles, water and oil. These contaminants can significantly affect the functionality of machines and processes.
Importance of Compressed Air Quality
High compressed air quality is essential to ensure trouble-free and long-lasting operation of compressed air systems. Compressed air is an energy source that is often used directly in machines, control systems and to manufacture products. Contamination in compressed air can not only damage machinery but also affect the quality of the final product. In sectors such as the food and pharmaceutical industries, this can have devastating effects.
- Machine protection: Contaminants such as water, dirt or oil particles can cause corrosion and mechanical wear, which drastically shortens the life of machines.
- Ensuring product quality: Contaminated compressed air can interfere with production processes and reduce the quality of end products. This is particularly critical in the food, medical and electronics industries.
- Minimize downtime: Contaminated compressed air more frequently leads to operational disruptions and failures, which can be associated with high costs.
- Optimizing energy efficiency: Clean compressed air contributes to the efficiency of the entire system by using less energy to supply machines with the compressed air they need.
Contaminants in Compressed Air and Their Effects
The most common contaminants in compressed air systems include oil, water and dirt particles. These contaminants get into compressed air in various ways and can have massive effects on machines and processes:
- Oil: Compressors often require lubricants that can get into compressed air. Oil residues are a major problem as they can contaminate both machines and products. This is particularly critical in sensitive industries such as the food industry, where even small amounts of oil can make products unusable.
- Water: Condensate is produced by compressing the air, which causes water to enter the compressed air line. This water causes corrosion in pipes and machines, which impairs material strength and shortens the life of the systems. Water can also damage electrical controls and increase maintenance costs.
- Dirt particles: Dust and other solid particles from ambient air or compressors can be deposited in valves, cylinders and seals. These deposits cause malfunctions, increase mechanical wear and can block lines, which in turn causes downtime and repair costs.
Air Pollution and Environmental Effects of Compressed Air Systems
Although compressed air systems offer a flexible and reliable source of energy, they also have an impact on the environment and contribute to air pollution, which is often overlooked.
Air Pollution From Compressed Air Systems
Energy consumption is a central problem of compressed air systems. To generate compressed air, electric compressors are often used, which require large amounts of energy. When this energy comes from fossil fuels, it results in high CO₂ emissions, which worsen air quality and drive climate change. Although compressed air appears clean, the process of generating compressed air is often not environmentally friendly.
In addition, leaks in compressed air systems can result in unnecessarily high energy consumption. Even minor leaks mean that compressors have to work harder to maintain the necessary pressure. This further increases energy consumption and increases air pollution through indirect CO₂ emissions.
Another problem is compressed air contamination. When compressors are operated without suitable filters, oil vapors, dust particles, and other contaminants can enter the compressed air and be released into the environment. This not only affects air quality, but can also have negative effects on machines and end products.
Environmental Impacts of Compressed Air Systems
The environmental impact of compressed air systems goes beyond air pollution. Due to their high energy consumption, they often have a considerable ecological footprint. This is particularly problematic when energy efficiency measures are not taken.
- Energy loss due to inefficient systems: Older or poorly maintained compressed air systems often use more energy than necessary. This not only pollutes the environment, but also causes higher operating costs.
- Water consumption and pollution: Many compressors require water for cooling. If this water is not used or recycled efficiently, this can result in increased water consumption. If the cooling water is not properly treated, pollutants can also enter the waste water and pollute the environment.
- Noise pollution: Compressed air systems, in particular compressors, generate noise that can lead to noise pollution in the surrounding area. Wearing hearing protection is often necessary, but noise can still have a negative impact on the quality of life around industrial plants.
Applications of Compressed Air Systems
Compressed air systems play a central role in many industrial and commercial applications. They make it possible to use powerful tools and machines, support the automation and ensure efficiency across a wide range of industries. The following gives you an overview of the most important areas of application for compressed air systems.
Tools and Machines
Compressed air systems are essential for the operation of many pneumatic tools and machines, which dominate industry and crafts due to their reliability and power. Commonly used tools include:
- Impact wrenches, drills and pneumatic hammers: They are used primarily in metalworking, construction and automotive engineering. These tools offer higher performance and durability compared to electrical alternatives.
- Spraying and painting technology: Compressed air is used in spray guns to evenly apply paints and varnishes. This is particularly important for surface finishing in the automotive, furniture and metal industries.
- Cleaning equipment: Compressed air allows machines and workpieces to be cleaned using high-pressure air jets, which remove dirt and debris.
Industrial Manufacturing and Automation
In industrial manufacturing and automation, compressed air systems are a key solution for controlling and driving machines. Compressed air plays a particularly important role in automation:
- Pneumatic cylinders and actuators: These devices move parts in production processes and contribute to the precise positioning and handling of workpieces. They are an integral part of assembly robots and other automated systems.
- Conveyors: Compressed air transports media such as bulk material, liquids or powder in industrial manufacturing processes. Examples include sandblasting and painting systems as well as systems for transporting bulk materials.
- Drying and cooling: In many production processes, such as the plastics or food industries, compressed air is used to dry products or to cool sensitive materials.
Crafts and Construction
Pneumatic tools are widely used in crafts and construction because they are robust and powerful:
- Construction machines such as pneumatic hammers, nail guns or pneumatic drills offer a high degree of mobility and efficiency. Compressed air systems are lighter than electric alternatives, which makes them easier to handle on construction sites.
- Grinding and polishing machines: These tools are used for precise work on surfaces, such as in wood or metal processing.
Food and Pharmaceutical Industries
The food and pharmaceutical industries place high demands on cleanliness and precision. Compressed air is widely used here in specific applications:
- Packaging machines: Compressed air ensures precise control of packaging processes, such as sealing, filling or labeling products. It is also ideal for systems that require sterile work.
- Transporting food: Compressed air is used to transport sensitive products, such as powders or liquids, through pipes without causing contamination. This is particularly important in the manufacture of pharmaceutical products to ensure purity.
- Ventilation and drying: In food production, compressed air plays a central role in drying products or in processes that require a sterile environment.
Transport and Logistics
In the transportation and logistics sector, compressed air systems make it possible to operate systems for controlling and moving goods:
- Pneumatic conveyors are used to transport materials to warehouses, production facilities or transshipment points.
- Truck brake systems: Many trucks use compressed air for their brake systems because they are robust and reliable.
Medical Applications
Compressed air systems are also used in a variety of ways in the medical sector:
- Ventilators and surgical instruments are often powered by compressed air to ensure precise control and reliable performance.
- Sterilization and ventilation: In hospitals and laboratories, compressed air is used to sterilize equipment or to ventilate clean rooms to create a safe working environment.
Standards and Legal Requirements for Compressed Air Systems
For compressed air systems, there are several relevant standards and legal regulations that you should follow to ensure the safety and quality of compressed air. The most important regulations include the classification of compressed air purity, safety requirements and energy efficiency regulations.
ISO 8573-1 — Compressed Air Purity Classes
The ISO 8573-1 standard defines purity classes for compressed air and is one of the central standards in the area of compressed air systems. It categorizes the quality of compressed air based on three main factors:
- Solid particles,
- Water and
- Oil.
There are different purity classes for each of these factors. An example would be ISO 8573-1:2010 [4:3:3], which means:
- Solid particles class 4,
- Water class 3,
- Oil class 3.
Compressed air, which is used in particularly sensitive areas such as the food industry, medical technology or electrical engineering, must be oil-free and comply with class 0. This class requires 100% oil-free compressed air.
For quality class 1 compressed air, the limit values are defined as follows:
- Oil content: less than 0,01 mg/m³,
- Maximum particle size: no larger solid particles than 0.1 µm,
- Particle concentration: the mass concentration must not exceed 0.1 mg/m³,
- Water percentage: The pressure dew point of the steam must be ≤ -70 °C.
Pressure Equipment Directive (DGRL) 2014/68/EU
The Pressure Equipment Directive (DGRL) 2014/68/EU ensures that compressed air systems are operated safely in the European Union. It regulates the placing on the market and putting into service of pressure equipment and components that are subject to a maximum allowable pressure of more than 0.5 bar. Compressed air systems must comply with this directive, particularly when it comes to boilers, compressors and pressure vessels.
Key requirements include:
- Safety requirements for construction and manufacturing,
- Choice of material,
- Testing and marking of pressure equipment,
- Safety valves and rupture discs to relieve pressure.
Industrial Safety Ordinance (BetrSichV)
In Germany, the Industrial Safety Ordinance (BetrSichV) is decisive for the safe operation of compressed air systems. This regulation governs:
- Maintenance and regular testing the pressure vessel,
- Safety measures when operating compressed air systems,
- Risk assessmentsto identify and minimize risks.
VDI 2290 — Emissions From Compressors
According to VDI guideline 2290, compressed air systems must also comply with certain limit values with regard to emissions such as noise and escaping substances. The guideline specifies how systems are to be operated in such a way that no harmful effects on the environment arise.
Energy Efficiency — ISO 50001
In addition to safety, energy efficiency also plays an important role in compressed air systems. The ISO 50001 standard provides a framework for the efficient operation of compressed air systems and helps you to reduce energy consumption. This is particularly relevant as compressed air systems often account for a significant proportion of a company's total energy consumption.
You should regularly:
- Check and fix leaks,
- Size compressors correctly,
- Maintain maintenance intervals.
Optimizing energy efficiency not only leads to cost savings, but also meets legal sustainability requirements.
Compressed Air Systems FAQ
What Are Compressed Air Systems?
Compressed air systems are systems that compress and store air and then pressurize it for various applications. These systems consist of a compressor, which compresses the air, and a storage tank in which the compressed air is stored. Compressed air systems are used in many industrial and commercial applications.
What Is the Purpose of a Compressed Air System?
The purpose of a compressed air system is to provide compressed air as an energy carrier. This energy can be used for machines, tools and processes to operate drives, control valves, or drive pneumatic tools. Compressed air is particularly popular in industry because of its flexibility and reliability.
Which Components Are Crucial for a Compressed Air System?
Important components of a compressed air system are:
- Compressor (Generates compressed air)
- Compressed air tank (stores compressed air)
- Filters (Removes impurities)
- Dryers (Reduces moisture)
- Regulator (Adjusts pressure)
- Distribution system (line system for distributing compressed air)
How Does an Air Compressor Work?
An air compressor compresses air by forcing it into a cylinder. Piston compressors use a piston to compress the air, while screw compressors use two interlocking screws to reduce the volume of air. This compression increases the pressure, allowing the air to be used as an energy source.
Why Is Compressed Air Treatment Important?
Preparing compressed air is important to remove contaminants such as moisture, oil, or dust that can affect the efficiency and lifetime of the system. Unclean compressed air can damage machines and disrupt the production process. Filters, dryers and oil separators are crucial to ensure high-quality compressed air.
Which Measures Contribute to the Efficiency of Compressed Air Systems?
The following measures contribute to increasing the efficiency of a compressed air system:
- Leakage control: Regular testing and sealing of leaks.
- Needs-based pressure setting: Only generate as much pressure as is required.
- Optimizing lines: Avoid cables that are too long or too narrow.
- Heat recovery: Using the compressor's waste heat for other processes.
- Regular maintenance: Maintain filters, dryers and compressors regularly.
What Are the Differences Between Compressed Air and Pneumatics?
- Compressed air: Compressed air, which is used as an energy source.
- Pneumatics: Use of compressed air to control and operate machines.
What Are the Differences Between Pneumatic and Hydraulic Systems?
- Pneumatic systems: Use compressed air as a means of propulsion, ideal for quick movements and light loads.
- Hydraulic systems: Use oil or liquid, offer higher forces and are better suited for heavy loads.
What Are the Differences Between a Compressed Air System and a Compressed Air Line System?
- Compressed air system: Complete system, consisting of compressor, storage tank, filters and piping system.
- Compressed air piping system: Only the pipe network that transports compressed air from source to consumers.
Which Materials Are Optimal for Compressed Air Lines?
The best materials for compressed air lines are:
- Aluminum: Lightweight, rust-proof, easy to install.
- Inox: Robust and resistant to corrosion.
- Copper: Good conductive material, resistant to corrosion.
- Plastic (e.g. polyethylene): Flexible and cost-effective, but only suitable for smaller applications.
Which Diameter Is Suitable for Compressed Air Lines?
The diameter depends on the required air volume and the line length. In general, the following applies:
- Smaller diameters for short distances and low air volumes.
- Larger diameters for long pipes and high air requirements to minimize pressure losses.
What Are the Requirements for a Compressed Air Network?
A compressed air network must:
- Leak-free to avoid energy losses.
- Efficiently dimensioned be to minimize pressure losses.
- Corrosion resistant to ensure longevity.
- Flexible be expandable to respond to future changes.
What Are the Disadvantages of Compressed Air?
Compressed air has several drawbacks:
- Energy-intensive: High power consumption to generate compressed air.
- Noise pollution: Compressors are often loud.
- maintenance costs: Requires regular maintenance to prevent leaks and contamination.
- Pressure losses: Significant pressure losses can occur over long distances.
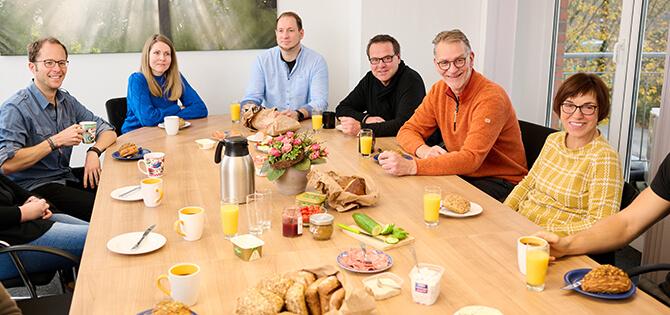
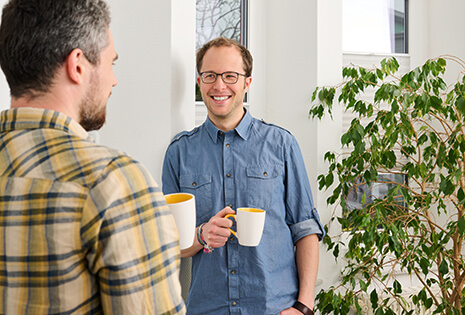
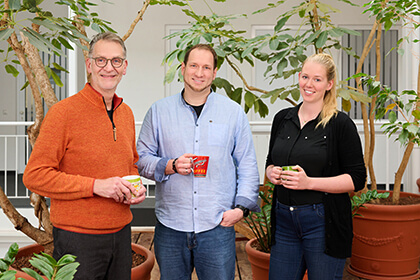
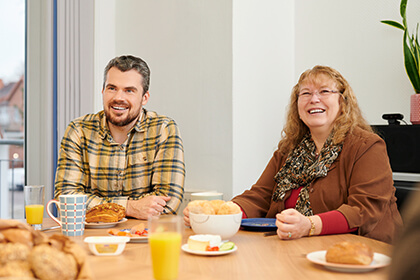
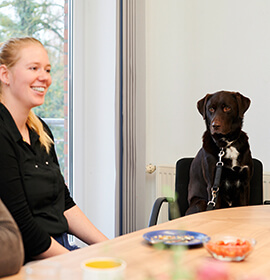
Are you an engineer or designer looking for new challenges? With us you can expect a familiar atmosphere and exciting tasks!
View Job Ads Now!