Explosion protection (Ex protection) comprises measures to prevent explosions and their consequences. It is crucial in areas where explosive atmospheres are caused by flammable substances such as gases, vapors or dust, e.g. in the chemical industry or when handling hazardous substances.
What Is Explosion Protection?
Explosion protection is a central area of safety technology that aims to prevent explosions from occurring and their consequences. It is particularly important in industrial processes in which flammable substances such as gases, vapors or dust occur. Such potentially explosive atmospheres occur, for example, in the chemical industry or when handling flammable liquids, gases or dust. These substances can be released during normal operation or in the event of faults and thus create an explosive atmosphere.
The aim of explosion protection is to protect people and property from the dangers of an explosion. An explosion can have serious consequences, such as serious injuries, death, or significant property damage. Causes of explosions can be human error or technical defects that lead to ignition of the explosive atmosphere.
Why Is Explosion Protection So Important?
Explosion protection is essential because the consequences of an explosion can be catastrophic — both for the people affected and for the entire infrastructure. The destructive power of an explosion differs fundamentally from an ordinary industrial accident. While minor accidents such as cuts or falls are often localized and relatively easy to deal with, an explosion has the potential to claim lives and cause immense damage to technical equipment.
There are numerous sources of danger in industry that can trigger explosions, which is why a careful pre-engineering phase and basic engineering are of great importance. These affect not only mining or the chemical industry, but also other sectors such as textile and wood processing, mills and warehouses. Higher processing speeds and increased mechanization result in more friction and dust formation, which further increases the risk of an explosion. You have to imagine that dust particles in the air, when ignited by a spark, can develop a tremendous explosive force.
The possible consequences of an explosion are often fatal: People can suffer serious injuries or even be killed. The recent explosion disasters in Tianjin (2015) and Beirut (2020) have also shown that explosions not only remain localized, but can also destroy large parts of a city and claim many lives.
The fear of an explosion often means that the issue of explosion protection is neglected, although technological innovations in the area of explosion protection are constantly advancing. People don't want to deal with it because they fear the possible consequences. But it is precisely this negligence that increases the risk. If you do not actively deal with explosion protection, dangerous situations can quickly occur that could have been avoided. The correct handling of explosion hazards, employee training, professional consulting services and regular maintenance of systems are therefore crucial to minimizing the risk.
Industrialization and the trend towards ever larger production facilities in modern plant engineering have increased the risk even further. Larger systems also mean greater sources of danger. A single spark can wreak havoc in such an environment.
How Does an Explosion Occur?
An explosion occurs when a combustible substance, oxygen, and an ignition source are present. This concept is known as an explosion triangle. If any of these components are missing, there will be no explosion.
Combustible Substance
Combustible substances are the basic component of an explosion and can be present in the form of gases, vapors, mists or dust. Each of these substances has specific properties that determine the risk of explosion. For ignition, these substances must be present in sufficient concentrations.
Explosive Atmosphere
An explosive atmosphere is created when flammable gases, vapors, fog, or dust mix with oxygen and the mixture is in a specific concentration range. These conditions are typically present in a temperature range between -20 °C and +60 °C and a pressure range of 0.8 to 1.1 bar. After ignition, an explosive atmosphere transfers the combustion process to the entire unburnt mixture.
Explosion Points and Flash Point
The flash point is the lowest temperature at which an ignitable vapor-air mixture forms over a combustible liquid. It is crucial for evaluating the explosion risk of liquids. If the temperature of a liquid is below its flash point, an explosive atmosphere cannot be created.
Explosion Limits
A mixture of air and combustible material only explodes when the fuel is present in a specific concentration range:
- Lower explosion limit (LEL): The minimum concentration of the combustible substance in the air above which an explosion is possible.
- Upper explosion limit (OEG): The maximum concentration at which an explosion is still possible. If the concentration is too high or too low, the mixture can no longer explode.
Sources of Ignition
An explosion is triggered by an ignition source when the conditions for an explosive atmosphere are met. Ignition sources can take many forms:
- Hot surfaces
- Sparks
- Static electricity
- Lightning strike
- Mechanical friction
- Flames and hot gases
Minimum Ignition Energy
The minimum ignition energy is the smallest amount of energy required to ignite an ignitable mixture. This energy can be extremely small, especially for gases such as hydrogen, which has a minimum ignition energy in the range of 10 joules. The ignition energy can be higher for dust.
Minimum Ignition Pressure
The minimum ignition pressure is the minimum pressure at which an ignitable mixture can be ignited. This value varies depending on the substance and is crucial for explosion protection, particularly in pressurized systems.
How Does a Dust Explosion Occur?
A dust explosion occurs when combustible dust particles are stirred up in the air and reach an explosive concentration. Similar to gas explosions, oxygen, combustible dust and an ignition source must be present at the same time. Dust explosions are often more dangerous than gas explosions because they can result in secondary explosions when the initial blast pressure raises even more dust.
What Are Ex-zones?
Ex zones play a central role in explosion protection (Ex protection), in particular within the framework of ATEX guidelines. These zones identify areas where explosive atmospheres can occur and are used to minimize the risk of an explosion by implementing appropriate protective measures.
ATEX Zone Division for Gases and Vapors
The ATEX zones for gases and vapors are divided into three zones based on the frequency and duration of occurrence of an explosive atmosphere:
- Zone 0: This is the area where explosive atmospheres (mixtures of air and combustible gases, vapors, or mists) exist constantly, frequently, or over long periods of time. Example: The interior of a container in which flammable liquids are stored above their flash point.
- Zone 1: In this zone, an explosive atmosphere occasionally occurs during normal operation. This zone comprises areas that are directly adjacent to zone 0, in which explosive mixtures can occur during regular operation.
- Zone 2: This zone describes areas in which an explosive atmosphere does not normally occur or only occurs for a short time, for example in the event of unforeseen events or operational failures.
ATEX Zone Division for Dust
Dusts that can form explosive mixtures with air are subject to a similar zoning:
- Zone 20: Here, an explosive atmosphere in the form of a dust cloud exists continuously, frequently or over longer periods of time. Example: Areas directly in or around equipment that release combustible dust.
- Zone 21: This zone occurs when a cloud of dust occasionally forms during normal operation. These areas are in close proximity to devices that release dust, but not continuously.
- Zone 22: An explosive dust cloud is normally not expected in this zone and only occurs rarely or briefly, usually as a result of operational failures or malfunctions.
Important Aspects of Ex-zoning
- The division of zones is based on the probability of an explosive atmosphere occurring.
- The devices and machines used must meet the respective requirements of the zone in order to prevent sources of ignition. In zone 0/20, the strictest requirements must be met.
- Zoning helps to implement appropriate explosion protection by taking into account the type of operating materials and the technical conditions.
Explosion Protection Measures
Explosion protection measures can be divided into primary, secondary and tertiary protective measures. Each of these categories has a different goal to prevent an explosion or minimize its effects.
Primary Explosion Protection
Primary explosion protection aims to prevent the formation of an explosive atmosphere from the outset or to severely restrict it.
- Substitution: The best way to avoid the risk of explosion is to replace explosive substances with less hazardous materials. For example, solvent-based paints could be replaced by water-soluble ones.
- Removal and dilution of explosive substances: Explosive dust or gases must be removed or diluted by ventilation. Regular cleaning of dust or technical ventilation can help here.
- Passivation of explosive substances: This involves converting the substances into a non-explosive state through conditioning, e.g. by moistening dust with hygroscopic substances such as magnesium chloride solution.
- Inertization: Inert gases such as nitrogen prevent oxygen from reaching flammable substances, thus avoiding an explosive atmosphere.
- Isolation: Explosive substances are hermetically sealed or processed in the absence of air to prevent the formation of an explosive atmosphere.
Secondary Explosion Protection
When it is not possible to completely prevent the formation of an explosive atmosphere, secondary explosion protection aims to avoid sources of ignition.
- Types of ignition protection: There are various technical approaches here:
- Intrinsic safety “i”: Limiting current and voltage in electrical systems to prevent ignition.
- Flameproof enclosure “d”: housing around electrical devices that safely contain a possible internal explosion.
- Increased safety “e”: Exclusion of sources of ignition through special design methods.
- “px” or “py” overpressure encapsulation: The interior of housings is kept under pressure with ignition protection gas to prevent the entry of an explosive atmosphere.
- Potting, oil and sand encapsulation “m/o/q”: Electrical equipment is embedded in material such as sand or oil to minimize ignition risks.
- Avoiding effective sources of ignition: According to the technical rules for operational safety (TRBS 2152), there are 13 possible sources of ignition that must be avoided. These include hot surfaces, mechanically generated sparks, static electricity, and electrical systems. Appropriate ventilation, the use of explosion-proof devices and the limitation of explosion zones help to minimize sources of ignition.
Tertiary or Structural Explosion Protection
If primary and secondary measures are not sufficient, structural explosion protection is used to control the effects of a possible explosion.
- Explosion-resistant construction: Systems are designed to withstand explosion pressure without bursting.
- Flame arresters: These prevent flames from being passed on by cooling the flame front.
- Explosion suppression: Explosion suppression systems, such as foam extinguishers, detect the explosion early on and suppress it before it can unfold.
- Pressure relief: Devices such as pressure relief valves and rupture discs divert the explosion pressure in a controlled manner to prevent damage.
Integrated Explosion Protection
Integrated explosion protection is based on a methodological approach that combines the three types of protection — primary, secondary and tertiary. These measures must be planned and implemented in such a way that they complement each other and are used in line with the respective explosion risks. Primary protection always has priority, as it directly prevents the formation of an explosive atmosphere. An engineer at an engineering office should therefore never neglect primary explosion protection.
Ex Protection Regulations and Guidelines
Explosion protection (Ex protection) is of central importance in industry to ensure safety in areas where explosive atmospheres can occur. The directives that apply in the EU and Germany, as well as international standards, such as the IECEx system, provide clear regulations for manufacturers, operators and testing centers.
ATEX Directive
The ATEX Directive forms the basis for explosion protection in the EU. It is divided into two parts:
- ATEX Product Directive 2014/34/EU: This directive applies to devices and protective systems that are used in potentially explosive areas. It regulates the basic health and safety requirements (ESHR) that products must meet to eliminate the risk of sources of ignition. The categories of devices are based on the degree of risk (1, 2, 3) and compliance is demonstrated by appropriate test methods and certifications.
- Category 1/M1: Highest safety requirements. Conformity is proven through type testing and regular production monitoring.
- Category 2/M2: Devices in this category must be tested and certified by notified bodies.
- Category 3: Internal production control by the manufacturer is sufficient here.
- ATEX operating directive 1999/92/EC: This directive is aimed at operators of plants in potentially explosive areas. It requires the preparation of an explosion protection document, which includes, among other things, a risk assessment and a protection concept. In addition, the operator must ensure that all systems are regularly tested and that protective measures comply with the state of the art.
IECEx System
The IECEx system is an international certification system for explosion protection that is used worldwide. It serves to harmonize testing and certification processes in order to facilitate the free trade of ex-products.
The most important components of the IECEx system are:
- IECEx Equipment Scheme: Certification of equipment for use in potentially explosive areas. The devices must go through a type test and prove compliance with the requirements.
- IECEx Certified Service Facilities Program: Certification of service providers working in potentially explosive areas (e.g. maintenance and repair of Ex equipment).
- IECEx Certification of Personnel Competencies: Certification of professionals working in potentially explosive areas to ensure that they have the necessary qualifications.
An IECEx certificate provides international recognition and facilitates global trade by supplementing or replacing national approval procedures.
Local Regulations in Germany
In Germany, explosion protection requirements are regulated by national regulations such as the Industrial Safety Ordinance (BetrSichV). This implements the ATEX operating guideline into national law and defines the requirements for the safe installation, maintenance and testing of systems in potentially explosive areas.
Important additional technical rules include:
- TRBS 1111: Risk assessment and safety-related assessment.
- TRBS 1201: Tests of work equipment and systems requiring monitoring, in particular in potentially explosive areas.
- TRBS 2152: Explosion protection measures, divided into various parts, which cover the assessment of the explosion risk and protective measures.
- TRBS 1203: Requirements for qualified persons who carry out tests.
In addition, the Technical Rules for Hazardous Substances (TRGS) are relevant, in particular:
- TRGS 720—727: These rules deal with the assessment and minimization of explosion risks caused by hazardous substances, including measures to avoid ignition risks (e.g. electrostatic charging).
Important Standards for Explosion Protection
Harmonised standards developed by the European Committee for Electrotechnical Standardization (CENELEC) and the international standards organization IEC form the technical basis for explosion protection in the EU. Important standards in the area of explosion protection include:
- IEC 60079 series: This series of standards covers the explosion protection of electrical devices and their installation in potentially explosive areas.
- IEC 60079-0: General requirements for devices.
- IEC 60079-1: Equipment protection by flameproof encapsulation “d”.
- IEC 60079-11: Equipment protection through intrinsic safety “i”.
- IEC 60079-13: Pressure-encapsulated rooms.
- IEC 60079-14: Design, selection and construction of electrical systems.
- IEC 60079-17: Testing and maintenance of electrical systems.
- IEC 60079-19: Equipment repair and overhaul.
- ISO 80079 series: This series of standards covers explosion protection for non-electrical devices:
- ISO 80079-36: Non-electrical equipment for explosive atmospheres — Basics and requirements
- ISO 80079-37: Non-electrical ignition protection types such as structural safety “c”, ignition source monitoring “b”, liquid encapsulation “k”.
These standards ensure that devices and systems can be safely planned, constructed and operated in potentially explosive areas.
Safety Assessment Process
Risk assessment is a central element of explosion protection. This must be carried out by the operator before using a device or plant in potentially explosive areas. The risk assessment includes:
- Identification of sources of danger: This includes a systematic ignition source analysis to identify and exclude potential sources of ignition.
- Classification of potentially explosive areas: Areas are divided into zones according to the probability of occurrence of explosive atmospheres (zone 0, 1, 2 for gases; zone 20, 21, 22 for dust) .
- IEC 60079-10-1: Classification of areas for gas-explosive atmospheres.
- IEC 60079-10-2: Classification of areas for atmospheres at risk of dust explosions.
- Safety measures: Based on the risk assessment, technical and organizational protective measures are defined to minimize explosion risks.
Other Key Guidelines
- EN 50495: Safety devices for the safe operation of equipment with regard to explosion risks.
- TRGS 751/TRBS 3151: Avoiding fire, explosion and pressure hazards at gas stations and filling plants.
Classification Into Device Groups and Device Classes
In Germany and the EU, the classification of explosion-proof devices is regulated by the ATEX Directive 2014/34/EU. This specifies how devices are divided into device groups and device classes in order to ensure safe use in potentially explosive areas. This applies both to explosion protection from gases and from dust. The devices are classified according to the probability and hazard of the occurrence of an explosive atmosphere.
Equipment Group I
Equipment group I comprises equipment that is used in underground mines and their surface facilities, where there may be a risk of mine gas and/or combustible dust.
- Category M1: Devices in this category guarantee a very high level of safety. They may continue to be operated in potentially explosive atmospheres, even in the event of rare equipment faults. An additional, independent protective measure ensures that there is no risk of ignition even if a protective measure fails. These devices are suitable for particularly vulnerable areas.
- Category M2: Devices in this category also offer a high level of safety, but must be switched off as soon as an explosive atmosphere occurs. They are robust and suitable for normal operation in heavily loaded areas, but not for use when there is an active risk of explosion.
Equipment Group II
Equipment group II concerns all equipment used in areas outside mines where explosive atmospheres can occur due to gases, vapors, fog or dust.
The devices are further divided into categories, depending on where they are used and the associated risk:
- Category 1: These devices offer a very high level of safety and are intended for use in areas where an explosive atmosphere can occur constantly, frequently or for extended periods of time. They must not pose a risk of ignition even in the event of rare faults. Examples of areas of application include zone 0 (gas) or zone 20 (dust).
- Category 2: Devices in this category offer a high level of safety and are suitable for areas where explosive atmospheres occasionally occur under normal operating conditions. They are intended for use in zone 1 (gas) and zone 21 (dust).
- Category 3: These devices provide a normal level of safety and are intended for areas where an explosive atmosphere occurs rarely and only for a short time, such as Zone 2 (gas) and Zone 22 (dust).
The letters G (gas) and D (dust) indicate the type of explosive atmosphere for which the device is designed. There are also combinations of G/D when one device is suitable for both types of atmospheres.
In addition, equipment group II devices are further divided into explosion groups, depending on the type of gases and dust to which they are exposed:
- IIA: Devices for less hazardous gases such as propane or butane.
- IIB: Devices for medium-hazardous gases such as ethylene.
- IIC: Devices for the most hazardous gases, such as hydrogen and acetylene.
For areas at risk of dust explosions (equipment group III), a similar distinction is made:
- IIIA: Combustible lint equipment.
- IIIB: Devices for non-conductive dust.
- IIIC: Conductive dust devices.
It is important that a device that meets the requirements of a higher group can also be used in lower groups. For example, an IIC device can also be used in IIA or IIb areas.
Division Into Device Classes
The classification into device classes is based on the so-called equipment protection level (EPL — Equipment Protection Level). This is based on the IEC 60079-0 standard and supplements the ATEX categorization. The classification indicates the safety level the devices must meet in potentially explosive areas:
- EPL Ga/Da: These devices offer a very high level of protection and may also be used in areas where an explosive atmosphere is constantly present (zone 0, zone 20). You must be safe even in the event of rare errors.
- EPL Gb/Db: Devices with a high level of protection that are used in areas where an explosive atmosphere occasionally occurs (zone 1, zone 21). They must not pose a risk of ignition in the event of frequent faults.
- EPL Gc/Dc: These devices offer an extended level of protection and are intended for areas where an explosive atmosphere is rarely present (zone 2, zone 22). In the event of foreseeable errors, safety must continue to be guaranteed.
Labeling of Products
Labeling products in explosion protection (Ex protection) is essential to ensure that devices can be safely operated in potentially explosive areas. In Germany and the EU, there are specific guidelines and standards that describe the requirements for labeling products in detail.
ATEX Directive 2014/34/EU
The ATEX Directive is the central directive for explosion protection in Europe. It regulates the requirements for products that are to be used in potentially explosive areas. Products covered by this Directive must be labelled accordingly if they have a potential source of ignition which may become an effective source of ignition. Products without an ignition source do not have to be marked, even if they are used in hazardous areas.
Important identification elements according to ATEX:
- Ex sign (hexagon with the abbreviation “ex” for explosion).
- Device group:
- I: Mining
- II: All other potentially explosive areas.
- Category: Determines the zone in which the device can be used:
- 1G/1D: zone 0 (gas), zone 20 (dust)
- 2G/2D: zone 1 (gas), zone 21 (dust)
- 3G/3D: zone 2 (gas), zone 22 (dust)
- CE marking with a possible number of the notified body.
- Ignition protection type: For example, “Ex d” for flameproof encapsulation.
Example:
CE 0589 Ex II 2G Ex e IIC T4Gb
(This shows a product suitable for potentially explosive gas atmospheres that can be used in zone 1.)
IEC/EN 60079-0 Standard
The IEC/EN 60079-0 standard defines the labelling requirements for electrical equipment in hazardous areas and is used internationally and in the EU. This standard supplements the ATEX label and contains important technical details.
Important identification elements in accordance with IEC/EN 60079-0:
- Ex mark: “Ex” marks the device as suitable for potentially explosive areas.
- Ignition protection type: For example, “Ex d” (flameproof enclosure) or “Ex e” (increased safety).
- Gas or dust group: IIA, IIB, IIC for gases or IIIA, IIIB, IIIC for dust.
- Temperature class: Defines the maximum surface temperature of the device (e.g. T1 to T6 for gases or specific temperature information in °C for dust).
- Device protection level (EPL): Determines the zone in which the device may be used (Ga, Gb, Gc for gas or Da, Db, Dc for dust).
Example:
Ex d IIB T4Gb
(This device is suitable for gas groups IIB, with a maximum surface temperature class T4, and for use in zone 1.)
International Markings (IEC)
The IEC 60079-0 standard, which is structured in a similar way to the European marking, is frequently used worldwide. It also includes information on the type of ignition protection, the gas or dust group and the temperature class.
Example of an international label:
Ex db eb IIC T4 Gb
(This device is for gas groups IIC, with double ignition protection type “flameproof enclosure” and “increased safety”, suitable for use in zone 1.)
Non-electrical Devices
Non-electrical devices used in potentially explosive areas are also subject to the ATEX Directive. Their identification is similar to that of electrical devices, using the letter “h” for non-electrical devices as the type of ignition protection. An example would be “Ex h IIIB T120°C.”
Labeling in North America
There are other standards and requirements in North America, such as the NEC (National Electrical Code) in the USA and the CEC (Canadian Electrical Code) in Canada. The classification is based on the division into classes and divisions as well as zones in accordance with NEC Article 505 or 506.
Example of a North American label:
Class I, Division 1, Groups C D, T 4
(This shows a device for use in Class I, Division 1 areas, with gas groups C and D and temperature class T4.)
Key Distinctions
It is crucial to differentiate between labeling in accordance with standards such as IEC/EN 60079-0 and legal requirements such as the ATEX Directive. In Europe, both labels are required to provide complete information about the explosion protection of a device.
Practical Explosion Protection Solutions for High-Risk Industries
In certain industries, there is a high risk of explosive atmospheres, which makes explosion protection (Ex protection) essential. The focus is on preventing and managing explosion risks. Explosion protection is of central importance in the following industries:
Industries With High Ex-risk
- Chemical plants: Combustible gases and liquids are often used in chemical production processes. In the event of leaks, explosive gas mixtures can form, which is why explosion protection is implemented by special ventilation systems and monitoring devices.
- Refineries: Large quantities of combustible materials such as oil and gas are processed here. An explosive atmosphere is almost omnipresent. Pressure relief devices and explosion-proof electrical systems are essential measures here.
- Grain silos: Dust explosions are a major risk in grain silos. Dust particles suspended in the air can easily ignite and lead to devastating explosions. Dust extraction systems and regular cleaning are decisive measures here.
- Paint shops: Painting processes produce flammable vapors which, in combination with sparks or hot surfaces, can trigger an explosion. Explosion-proof ventilation systems and ATEX-compliant tools are used here.
Implementing Explosion Protection in Practice
In practice, explosion protection is achieved through a combination of technical measures, organizational measures and the use of Ex-certified devices.
- Avoiding sources of ignition: The most important point in explosion protection is to exclude sources of ignition such as sparks, hot surfaces or electrical discharges. This is achieved, for example, by using explosion-proof machines and tools that are certified in accordance with ATEX guidelines.
- Ventilation and extraction: To prevent an explosive atmosphere, flammable gases, vapors, or dust must be removed from the environment. Ventilation systems and extraction systems are used here, which keep the mixture in the air at a safe level.
- Overpressure systems and protective membranes: In refineries and chemical plants in particular, overpressure systems are used to safely dissipate pressure in the event of an explosion. Explosion-proof membranes and pressure-resistant housings are typical examples of such measures.
- Avoiding flammable substances: In industries where this is possible, there is a switch to less combustible or alternative materials to minimize the risk.
- Organizational measures: Regular training and clear operating instructions ensure that employees know how to act in potentially explosive areas. Maintenance plans for Ex devices and regular inspections are also part of the organizational measures.
In practice, explosion protection therefore means that all sources of risk are identified and minimized through appropriate measures, which requires precise construction site coordination and structured project management.
Risk Analysis and Maintenance
A risk analysis in potentially explosive areas is crucial in order to identify potential hazards at an early stage and to take appropriate measures to prevent accidents. Particularly in process plants that fall under the Accident Ordinance, there is often a significant risk potential. A comprehensive risk analysis, which also takes into account non-intended operation, is essential.
Risk Analysis Methods
- PAAG/HAZOP process: This method has proven particularly effective in identifying safety-relevant deviations during operation. This involves systematically checking whether processes deviate from the desired mode of operation and what risks may arise as a result.
- Risk matrix: A risk matrix is used to assess risks based on the likelihood of their occurrence and the severity of the potential damage. This provides a visual overview and allows you to set priorities when managing risks.
- Layers of Protection Analysis (LOPA): This analyses which protective layers exist in order to minimize the probability of damage. The remaining risk is assessed in accordance with the protective measures already in place.
- Failure mode and impact analysis (FMEA): This method investigates potential sources of error in processes and evaluates their effects. This makes it possible to identify weak points that could possibly lead to operational disruptions.
- Zurich Hazard Analysis (ZHA): This method focuses on systematically uncovering risks in complex processes and their potential effects on operations.
Explosion Protection Maintenance
Regular maintenance is crucial for the safe operation of electrical systems in potentially explosive areas. In order to ensure that this maintenance meets explosion protection requirements, it is necessary that maintenance is carried out by trained personnel under the supervision of a person qualified to carry out the test.
Important maintenance points:
- Safety approval before work: Before maintenance work begins, you must ensure that there is no risk of explosion. Formal written permission from plant management is usually required to guarantee safety during work.
- Documentation of work: After maintenance has been completed, the work carried out must be documented in detail. You should confirm that all relevant regulations have been met.
- Inspection after repair: In Germany, following a repair that could impair explosion protection, an inspection by a competent person recognized by the authority or the manufacturer is required.
- Replacement of components: When you replace components or equipment, you must ensure that the explosion-related and instrument-related characteristics are observed. These tests can also be carried out by an approved monitoring body (ZÜS).
FAQ - Frequently Asked Questions About Explosion Protection
What Is Ex Protection?
Explosion protection, or explosion protection, refers to measures that minimize the risk of explosions in areas where explosive atmospheres can occur. Explosion protection comprises technical, organizational and personnel measures to prevent fires and explosions.
Which Ex Zones Are There?
Ex zones classify areas according to the probability of occurrence of explosive atmospheres:
- Zone 0: Area in which an explosive atmosphere is present continuously or over long periods of time.
- Zone 1: Area where an explosive atmosphere can occasionally occur during normal operation.
- Zone 2: Area where explosive atmospheres occur only rarely and for a short time.
For dust explosion protection, there are:
- Zone 20: Constant or frequent explosive dust atmosphere.
- Zone 21: Occasional explosive dust atmosphere.
- Zone 22: Rare and briefly explosive dust atmosphere.
Is Zoning Mandatory for Explosion Protection?
Yes, zoning is required by law. Employers must classify potentially explosive areas according to the probability of occurrence of explosive atmospheres. This classification is used for risk assessment and protective measures.
Which Laws Regulate Explosion Protection?
In the EU, the following laws regulate explosion protection:
- ATEX Directive 2014/34/EU: For devices and protective systems that are used in potentially explosive areas.
- ATEX Directive 1999/92/EC: For safety requirements in the workplace. In addition, national occupational health and safety laws and international standards such as IECEx are relevant.
What Is an Explosion Protection Document?
An explosion protection document is a mandatory document that documents the risk assessment in potentially explosive areas. It describes the explosion risks, zoning, protective measures and organizational measures to minimize the risk.
When Is an Explosion Protection Document Necessary?
An explosion protection document is required as soon as explosive atmospheres can occur in an establishment. According to ATEX Directive 1999/92/EC, it must be prepared before work starts and be regularly updated as risks change.
What Is Primary, Secondary and Tertiary Explosion Protection?
- Primary explosion protection: Prevents the formation of explosive atmospheres (e.g. by sealing containers).
- Secondary explosion protection: Avoids sources of ignition in potentially explosive areas (e.g. use of explosion-proof devices).
- Tertiary explosion protection: Minimizes the effects of an explosion (e.g. through pressure relief or explosion suppression).
What Are the Differences Between ATEX and IECEx?
- ATEX: Applies to Europe and is based on EU directives. It includes both equipment requirements (2014/34/EU) and workplace safety requirements (1999/92/EC).
- IECEx: Is an international certification system for potentially explosive areas that can be used worldwide. It is based on IEC standards and is more flexible for global use.
In Which Plant Planning Steps Is Explosion Protection Relevant?
Explosion protection is important in all phases of plant planning:
- Risk assessment: Determine whether explosive atmospheres can occur.
- Zoning: Classify areas according to Ex zones.
- Device selection: Select Ex-protected devices in accordance with the zoning.
- Protective measures: Plan measures for primary, secondary and tertiary explosion protection.
- Documentation: Create and regularly update an explosion protection document.
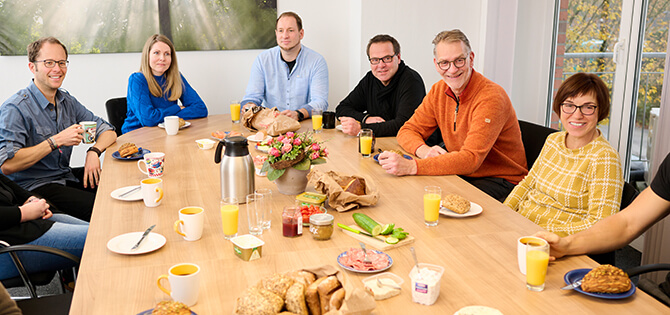
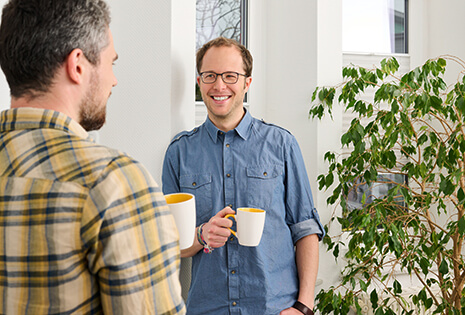
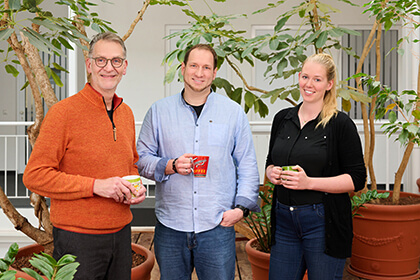
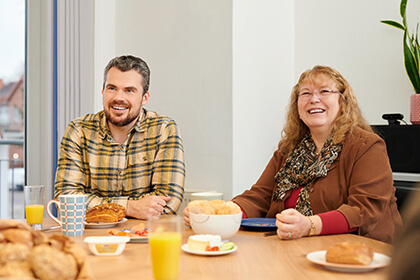
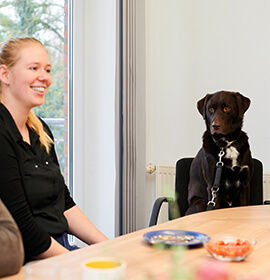
Are you an engineer or designer looking for new challenges? With us you can expect a familiar atmosphere and exciting tasks!
View Job Ads Now!