What is Distillation?
Distillation (lat. destillare, “to drip down”) is a thermal separation process in which mixtures of substances, usually liquids, are separated from each other based on their different boiling points. The process is designed to recover vaporizable liquids or to separate solvents from substances that are difficult to vaporize and then collect them by condensation.
During distillation, the initial mixture is first brought to boiling point. The resulting vapors are made up of the various volatile components of the solution to be separated. These vapors are liquefied again in a condenser by cooling. The condenser is a cooling device, for example a Liebig cooler on a laboratory scale. The liquefied condensate is then collected.
The separation effect is based on the different composition of the boiling liquid and the gaseous vapor. As the boiling points of the substances to be separated are relatively close to each other, they evaporate at different temperatures and condense one after the other, enabling effective separation of the components.
A major advantage of distillation compared to other separation processes is that no additional substances such as adsorbents or solvents generally need to be added.
important: The substances that you want to distill must not decompose at the high boiling temperature. When the boiling point of a substance is critically high, distillation must be carried out under reduced pressure to lower the boiling point.
Distillation is used in a variety of ways. Typical applications are:
- The burning of alcohol,
- The distillation of crude oil in refineries,
- The production of distilled water.
History and Development of Distillation
Distillation has a long history that dates back to the Neolithic period. The first use of the technique was to distill pitch and tar to seal ships, as an adhesive and even as a remedy.
Mesopotamian distillation devices (approx. 5500 years old): The earliest archaeological finds come from Mesopotamia (present-day Iraq). These simple devices consisted of a vessel with a lid. When heated, the distillate condensed on the lid. To prevent the condensed liquid from dripping back into the vessel, sponges or tufts of wool were placed in the lid to absorb the distillate. These were then pressed regularly to obtain the distillate.
Greek navigators and Aristotle (500 BC — 4th century BC): Around 500 BC, Greek navigators used similar methods to obtain drinking water from seawater. In the 4th century BC, Aristotle described the process for distilling seawater and explained that wines and other liquids could also be distilled.
Alexander of Aphrodisias (c. 200 AD): He provided a detailed explanation of how distilled water was produced, which further refined knowledge of the technique.
Arab scientists (800 AD — 10th century): The chemist Abu Musa Jabir ibn Hayyān (around 800 AD) improved distillation techniques. The Persian doctor ar-Razi (865—925) described the distillation of crude oil in the “Book of the Secret of Secrets.” He introduced a simple “crack process” for extracting products such as bitumen and brick oil. The Arabs also invented alembik (distilling helmet), which made it possible to distill alcohol. They also developed gentle heating methods in a water bath and steam distillation, in particular for essential oils and aromatic oils from herbs.
Discovery of sulfuric and nitric acid as well as ethanol (around 1000 AD): With the discovery of these substances, distillation became significantly more important. In the 12th century, scientists in Salerno improved cooling processes to separate liquids according to their boiling points. The technique was increasingly used in medicine.
Early modern period and alchemy (14th — 16th century): From the 14th century, distillation became an important tool in alchemy, particularly for the production of the so-called “quinta essentia”. The necessary equipment was also available in bourgeois households as early as the 15th century. In 1500, the surgeon Hieronymus Brunschwig published his “Little Distillation Book”, which disseminated knowledge about distillation. The use of distillation for the production of alcoholic herbal extracts and other medical applications continued to increase.
Improved appliances and cooling techniques (Middle Ages — 17th century): The alchemists of the Middle Ages improved cooling capacity by developing the “serpente,” a device with a long steam pipe. The “retort”, in which the distiller helmet and the flask were fused into one piece, was also developed. Improvements included longer cooling pipes that were passed through water barrels or water bowls around the still helmet. This apparatus was called “Mohrenkopf” because the cooling bowl looked like a turban.
Freshwater distillation from seawater (17th century): Freshwater distillation technology experienced a renewed upsurge in the 17th century. This allowed ships and seafarers to obtain drinking water from seawater, which was crucial for long sea voyages.
Restrictions and regulations: The distillation of ethanol was controlled and taxed in many states. In Germany, this happened, for example, as a result of the Brandy Monopoly Act.
Meaning of Distillation: Why Do You Distill?
Distillation is an essential separation process that is used in chemistry as well as in industry and research. But why do you distill anyway?
Benefits of Distillation
- No added chemicals: During distillation, you do not need any other solvents or adsorbents (such as porous materials that absorb substances). As a result, the mixture to be separated is no further contaminated and there are no additional costs for additional chemicals.
- Pure separation: Distillation allows the components of a mixture to be separated cleanly based on their physical properties such as the different boiling points. There are no chemical reactions, which makes the method particularly reliable.
- Wide range of applications:Some text
- Separation of liquid mixtures: Distillation is ideal for separating various liquids in a mixture.
- Cleaning and treatment of liquids: If you want to purify or process a liquid, distillation is one of the best methods.
- Analysis and identification: In research, distillation can be used to analyze and identify the components of a liquid.
Meaning Based on an Example in Chemistry
An illustrative example is the Separation of crude oil. Petroleum consists of various hydrocarbons with different boiling points. During distillation, these components are separated and can then be identified. Distillation is therefore often the first step in analyzing complex mixtures.
Principles of Distillation
Simple Distillation
Simple distillation is a thermal separation process based on the evaporation and subsequent condensation of substances. The aim is to separate one substance from another by exploiting its different boiling points. This method is used to separate or purify mixtures, for example to remove dissolved contaminants from a liquid.
In simple distillation, the mixture to be separated is heated in a still flask. The heat source can be a heating hood, a heating bath or a burner. As a result of heating, the temperature of the mixture rises until the boiling point of the target component is reached. This starts to evaporate and rises as a gas. The temperature of the steam can be read using a thermometer, which is located at the top of the apparatus. This so-called “head temperature” helps to identify the desired component and ensure that it evaporates.
The gaseous substance then enters the cooler, usually a Liebig cooler, which is cooled with water. Here, the vapor condenses back into a liquid as it is cooled down. The condensed distillate is then collected in a collecting flask. The end product is a liquid which contains a higher proportion of the lighter boiling component, while the so-called distillation sump, i.e. the remaining liquid, depletes of this component over time.
It is important that simple distillation does not allow perfect separation. The separation is based on the different boiling points of the components of the mixture, more precisely on their different vapor pressures at the same temperature. The composition of the vapor over the boiling liquid is always slightly different from that of the liquid itself. Condensation results in a liquid which has an increased proportion of the low-boiling component.
A classic example of simple distillation is the separation of dissolved salts or other solids from water. These substances cannot be removed by filtration because they are dissolved in the liquid. Simple distillation, on the other hand, makes it possible to evaporate the liquid while the non-volatile impurities remain in the distillation sump.
Multi-Stage Distillation and Rectification
For more precise separation, multi-stage distillation or rectification is used. In simple distillation, highly volatile components with a low boiling point are enriched in the vapor phase. If you condense the steam again and distill it, you get closer and closer to the pure substance. By using a column between the distillation bubble (sump) and the distillation head, a significantly improved separation efficiency can be achieved even after a single distillation. This separation efficiency is referred to as the “theoretical number of soils”, named after the principle of petroleum distillation in so-called bell-bottom columns.
In a column, an equilibrium between the liquid and gaseous phases is constantly established at the surface by repeated condensation and evaporation. In this way, the proportion of the low-boiling component rises, while the higher-boiling component flows back into the sump. By installing special elements such as a Vigreux column, Raschig rings or other structured packings, the surface area within the column is increased, which further increases the efficiency of separation.
If the substances to be separated form an azeotrope, the boiling and dew point curves do not only meet for the pure substances, which means that separation by distillation is only possible up to a certain point. The best-known example is the azeotrope of ethanol and water in a ratio of around 25:1, which results in the commercial “96 percent alcohol” mixture. However, further separation is possible since the azeotropic mixing ratio depends on pressure. By vacuum or overpressure distillation, the azeotrope can be shifted and further separation can be achieved. In addition, azeotrope correction can result in a higher concentration of ethanol.
The large-scale implementation of multi-stage, continuous distillation is referred to as rectification. During rectification, separation takes place in a so-called rectification column. This consists of several levels or floors through which the steam rises and the condensate flows downwards. In the column, the principle of multi-stage distillation is transferred to a continuous process in which products can be continuously withdrawn and starting materials can be refilled.
Fractional Distillation
In fractional distillation, you separate a mixture of several components into individual fractions by distillation. The prerequisite for this is that the components have different boiling temperatures. The process consists of several steps, in which the temperature is gradually increased to separate the various components. The process is often used when the boiling points of the components are close together.
You start by heating the mixture. First, the component with the lowest boiling point evaporates. This time is indicated by a change in temperature in the distillation head. The steam is then condensed and collected in a container, the so-called collection container. As soon as the temperature continues to rise and the next component starts to evaporate, change the collection container. In this way, you separate the different factions.
An intermediate fraction is often formed during the transition between two components, as the substances are still mixing in this area. To keep this intermediate fraction as low as possible, you can interpose a column. The column ensures that the substances are better separated from each other by condensing and evaporating again several times before it reaches the distillation head.
For simple, fractional distillation in the laboratory, you use a grinding apparatus with a so-called “spider” as a template. Several pistons can be attached to this spider. During the process, the temperature is gradually increased and the spider rotates to the next empty flask to collect the corresponding fractions.
Example: With a mixture of methanol, ethanol and water, methanol first boils at 65°C. You turn the spider towards the first flask. Then raise the temperature to 78°C to distill ethanol and switch to the next flask. Finally, you raise the temperature to 100°C to collect the last fraction, the water.
In the case of complex mixtures such as crude oil, which consists of many substances with different boiling points, fractional distillation is carried out in large columns. The column is equipped with so-called “bell bottoms”. The rising steam bubbles through these floors, which are kept at certain temperatures. Substances with higher boiling points condense on the respective base of the bell and can be removed via taps attached to the side. The temperature of the individual fractions can be monitored via thermometers. Fully filled bell bottoms flow back into the flask via an overflow.
Fractional distillation is used not only in laboratories, but especially in industry. A typical example is the petroleum industry, where crude oil is broken down into various components such as gasoline, kerosene and diesel.
Vacuum Distillation
Vacuum distillation is a distillation technique in which the pressure in the distillation plant is reduced. By reducing the overall pressure, the boiling point of the components in the substance mixture is reduced. This is particularly important if the mixture contains substances that are unstable at high temperatures or could decompose. Vacuum distillation therefore makes it possible to separate temperature-sensitive substances without risking their thermal decomposition.
Vacuum distillation is often used in laboratory practice, as adverse side reactions can occur in the sump at higher temperatures. The sump often contains residues of the starting material, catalyst residues or by-products. At high temperatures, these could reduce the yield by entering into undesired reactions. Lower pressure ensures that the mixture to be separated boils faster and is therefore treated more gently.
Vacuum distillation is also important in large industry. In petroleum refining, the so-called “sump product” of atmospheric distillation is subjected to a subsequent vacuum distillation. This mainly produces base oils for lubricating oil production and vacuum gas oil. Vacuum gas oil serves as a valuable starting material for downstream processes such as Cat Crackers or Hydrocrackers. In addition, in this industrial application, low-boiling residues are removed and partly returned to atmospheric distillation.
In the technical design of vacuum distillation, the apparatus is evacuated using a pump. The apparatus must be designed for negative pressure, otherwise there is a risk of implosion. It is therefore recommended to use small round bottom flasks that are specifically suitable for negative pressure. Safety goggles are also essential. This distillation method is particularly suitable for substances with a high boiling point or for substances that easily decompose at higher temperatures. The pressure reduction reduces the boiling points of the substances, which enables careful separation.
Cold Distillation
During cold distillation, the distillation feed is cooled down considerably, usually with the help of liquid nitrogen (-196 °C). This method is primarily used to remove solvents from a mixture. First, the mixture is heated or the apparatus is placed under vacuum so that the solvent evaporates. As a result of intensive cooling in the receiver, the solvent solidifies there while the desired product remains in the reaction flask.
Overpressure Distillation
Overpressure distillation is used to increase the boiling point differences of the components to be separated. In this case, the distillation plant operates under increased pressure. The increased pressure shifts the boiling points of the substances, which enables better separation, especially for substances with very low and closely spaced boiling points. Typical applications include air liquefaction or the processing of plant material that contains oils that are difficult to distill. When using superheated steam under excess pressure, the ratio of oil and water in the distillate can be improved.
Bullet Tube Distillation
Ball tube distillation is a process that is used primarily in laboratories for the distillation of small quantities of substances. The method is based on a spherical container in which the liquid is heated. The short distance between receiver and condenser ensures gentle distillation. It is particularly suitable for sensitive or difficult to evaporate substances.
Drag Distillation
During drag distillation, an additional substance is added which “drags along” the substance to be distilled off. Steam distillation is the most well-known form of this technique. It is used in particular when vacuum distillation is impracticable. Examples include:
Steam Distillation
In steam distillation, the introduction of water vapor entrains liquids or solids which have a higher boiling point than water or are insoluble in water. The steam is then condensed and the distillate is obtained. This method is used, for example, to obtain essential oils from plants.
Azeotropic Distillation
Azeotropic distillation is a process for separating components of an azeotropic mixture. An azeotrope is a mixture of substances with a constant boiling point that cannot be separated by normal distillation. During azeotropic distillation, another solvent (agent) is added, which forms a new azeotrope with the original components. This azeotrope can then be separated by distillation.
Example: In acid-catalyzed esterification, the resulting water can be almost completely removed by adding toluene, hexane or chloroform. These substances form heteroazeotropes with the water, which condense in two phases and can be easily recycled with a water separator.
Extractive Distillation
Extractive distillation adds a high-boiling, non-volatile substance which does not combine as an azeotrope with the components to be separated. A typical example is the use of ionic liquids to change the phase equilibrium and to enable the separation of narrowly boiling liquids or azeotropic mixtures. By changing the thermodynamic properties of the mixture, distillation can be carried out at reasonable cost.
Short Path Distillation
Short-path distillation (KWD) is a particularly gentle thermal separation process that is carried out in the medium vacuum range (1 to 0.001 mbar). The gas phase only travels a short distance between the evaporator and the condenser. Because of the low pressure, distillation can be carried out even at relatively low temperatures, which protects thermally sensitive products. The method is suitable for molecules that are difficult to evaporate, such as long-chain hydrocarbons, and is used to separate substances such as tocopherols, fatty acid esters and pharmaceutical agents.
Reactive Distillation
Reactive distillation combines distillation with a chemical reaction. This combination makes it possible to continuously influence the chemical equilibrium and thus achieve complete reactions. By removing a reactant at the same time, the equilibrium is shifted, which results in a larger turnover. In addition, azeotropes resulting from the chemical reaction can be broken. Reactive distillation is particularly suitable for equilibrium-limited reactions and is occasionally used in the chemical industry, for example in potassium production.
The chemical reaction can be catalyzed homogeneously or heterogeneously. In the case of homogeneous catalysts, an additional separation stage is required to separate the catalyst. In heterogeneous catalysis, the catalyst is often used in the form of reactive packs in the distillation column.
Zone Distillation
The zone distillation takes place in an oblong container and contains a partial melt of the substance to be separated in a moving liquid zone. The steam condenses into the solid phase, and the admixtures are distributed unevenly over the course of the process. As a result of moving the zone heater along the container, a condensate is formed with an even distribution of impurities, isolating the purest part as a product. This process can be repeated several times to achieve higher purity. Zone distillation is the distillative counterpart to zone recrystallization.
Dry Distillation
Dry distillation, also known as separation distillation, decomposes a substance by heating it to high temperatures without adding a solvent or water. This method is used in the chemical industry and in the processing of natural resources, for example in wood gasification. During wood gasification, wood is heated in the absence of oxygen and breaks down into gaseous, liquid and solid components. The gaseous phase can be used as fuel, while the solid phase, often referred to as charcoal, can be further processed.
Accidental Distillation Processes
Distillation processes can take place unintentionally in technical systems, such as extraction systems for vapors. Extracted vapors condense in extraction pipes and lead to blockages or deposits in the long term. Examples include:
- Fat deposits in kitchen hoods.
- Water condensate in compressed air hoses, which can freeze at low temperatures.
- Soothing in chimneys.
Distillation Applications
Distillation of Alcohol
The most well-known example is the separation of ethanol by distillation. As a rule, the mixture contains ethanol, water and small amounts of methanol. The boiling temperatures are: methanol 65 °C, ethanol 78 °C and water 100 °C. Methanol evaporates first, creating the so-called flow. This preflow must be discarded as methanol is highly toxic. Ethanol is then distilled. However, some of the water also evaporates, as there is still no complete temperature difference at 78°C, meaning that the separation is not complete.
Crude Oil Distillation
Crude oil is broken down by distillation in oil refineries to obtain products such as gasoline, diesel, kerosene or heating oil. Because crude oil contains hydrocarbons with various boiling points, two distillation processes are required: atmospheric distillation and subsequent vacuum distillation. Vacuum distillation makes it possible to separate heavy hydrocarbons at slightly higher temperatures without the formation of unwanted by-products as a result of cracking.
Distillation of Essential Oils
When distilling essential oils, steam is passed over plant material. The steam removes the oils from the plants. You then condense the steam and the oil-water mixture. A separating funnel is used to separate the oil from the water. This method is often used to obtain fragrances and flavorings.
Solvent Recovery
Here you distill used solvents in order to purify and reuse them. The solvent is heated to remove the impurities. The purified solvent vapor is condensed and collected in a collection container. In this way, you can save resources and reduce costs.
Water Treatment
Water distillation heats water until it evaporates. The steam then condenses into pure water in a cooling device. Through this process, you remove salts, minerals and impurities from the water. It is particularly suitable for producing ultrapure water for medical or industrial applications.
Distillation in Various Industries
Depending on the industry, whether chemical, pharmaceutical, petrochemical, beverage or water management, distillation is used in various forms. The following sections provide an overview of how distillation is used in various industries.
Distillation in the Chemical Industry
In the chemical industry, distillation is one of the most important processes for breaking down substances such as solvents, bio-oils, fats and plastics into their components. Plant engineering is crucial for setting up efficient distillation systems. Vacuum distillation plays a particularly important role, as it allows heat-sensitive compounds to be treated gently. The lower process temperatures prevent unwanted decomposition processes such as polymerization or cracking. As a result, higher yields can be achieved and significant energy savings are possible. Vacuum distillation is used to purify monomers, extract natural compounds, chemical syntheses and produce flavorings and aromas.
Distillation in the Pharmaceutical Industry
Vacuum distillation is also of central importance in the pharmaceutical industry, particularly in the production and purification of active pharmaceutical ingredients (APIs). By using the vacuum process, heat-sensitive substances can be treated gently and a high degree of purity can be achieved. In addition, by-products are reduced to a minimum, which is crucial when synthesizing drugs. Vacuum distillation also allows natural pharmaceutical ingredients to be extracted and purified, making it an indispensable process in pharmaceutical manufacturing.
Distillation in the Petrochemical Industry
In the petrochemical industry, particularly in oil refineries, distillation is crucial for the production of products such as gasoline, diesel, kerosene and lubricating oils. After atmospheric distillation, a second distillation is carried out under vacuum. This makes it possible to separate heavier hydrocarbons at only slightly elevated temperatures. The process minimizes cracking of the components and the formation of unwanted by-products, which leads to higher product purity and efficiency.
Distillation in the Beverage and Beverage Industry
In the beverage and beverage industry, distillation is primarily used to produce spirits. Distillation makes it possible to control the alcohol content and aroma. Although vacuum distillation is less common in this industry, it can be used to remove unwanted substances from fruit juices to improve the quality of the final product.
Distillation in Water and Wastewater Management
In water and wastewater management, distillation is a key element in the treatment of drinking water. This removes pollutants and microorganisms through evaporation and condensation. Vacuum distillation can be used specifically in industrial wastewater treatment to remove chemical contaminants, which enables gentle and energy-efficient water purification.
Distillation Process
Distillation Preparation
As part of pre-engineering, the appropriate distillation method and the required equipment are carefully selected.
- Objective: Think about what you want to achieve with distillation. Is it about isolating a specific substance, or do you want to separate the individual components of a mixture?
- Determine substance properties: Find out about the physical properties of the substances to be distilled. Knowing the boiling points is crucial to choosing the right temperature for distillation. For example, ethanol has a lower boiling point (78.37 °C) than water (100 °C).
- Prepare equipment: Make sure you have all necessary equipment at hand. The planning and design of distillation devices, such as columns, coolers and collection vessels, is usually carried out during basic engineering. The basic equipment includes:
- Distillation flask: To heat the mixture.
- Thermometer: To monitor the temperature.
- Capacitor: To cool the resulting steam.
- Collector: To collect the distillate.
- Safe work environment: Since you're working with heat and potentially hazardous chemicals, a safe environment is essential. Always wear suitable protective clothing (lab coat, gloves, goggles) and ensure that the distillation apparatus is stable on a heat-resistant surface. Work in a well-ventilated area or under a flue.
Profound consulting from experts can significantly influence the success of a distillation, particularly with complex mixtures.
Carrying out the Distillation
- Filling the distillation flask: Place your mixture in the distillation flask. Make sure that the flask is not more than two-thirds full to leave room for steam to develop.
- Heating: Heat the mixture evenly and slowly in the distillation flask. Use a thermometer to monitor the temperature and make sure it doesn't rise too quickly. This is important so that the vapor is produced in a controlled manner and the desired substance evaporates first.
- Condensing steam: As soon as the substance with the lower boiling point evaporates, the vapor is passed through the condenser. The condenser cools the steam and converts it back into a liquid.
- Collect distillate: Pour the condensed distillate into the collecting vessel. Make sure that all connections in the equipment are tight to prevent loss of steam.
- Temperature monitoring: During the entire process, you must carefully monitor the temperature and adjust it if necessary. The temperature changes may indicate that the composition of the mixture in the flask is changing.
Notes and Special Features
- Make sure that distillation is a dynamic process. The composition of your mixture can change during distillation, which you can see through color changes or sediment formation in the flask.
- The substance with the lower boiling point evaporates first and is then collected as pure distillate. If several substances are present, further separations can be carried out by redistillation (rectification).
- Effective project management is essential to successfully design distillation processes from planning to installation to commissioning.
Distillation Residue
What Are Residues From Distillation?
Distillation residues are the substances that remain in the distillation apparatus after the distillation process. They often consist of:
- Unmodified starting materials: Materials that have not evaporated due to their high boiling points or lack of volatility at the applied temperature.
- Difficult to distill ingredients: Substances whose boiling points are too high to go into the gaseous state during distillation.
- Unwanted by-products: Substances that are produced during the process but are not required in the end product.
There are different types of distillation residues:
- Dry residue: Remains when all volatile components have been removed. This residue is usually a solid or a viscous substance.
- Oily residue: An oily or tar-like residue that is often produced during the distillation of organic matter.
- Unmodified starting materials: Materials that have not yet been brought to the boiling point because the distillation was stopped prematurely.
What Is the Meaning of Distillation Residues?
Distillation residues are not simply “waste.” They can provide important information and, in some cases, contain valuable substances:
- Process evaluation: The analysis of residues makes it possible to assess the efficiency of the distillation process and can reveal problems such as insufficient separation or incorrect temperature settings.
- Further processing: In certain cases, residues can undergo additional treatments to obtain further valuable products. For example, residues from crude oil distillation are often further fractionated or cracked.
- Raw material quality indicator: In the fractional distillation of crude oil, the amount and type of residue can provide information about the quality of the crude oil.
What Do You Do with Distillation Residues?
How the residues are handled depends on their type and composition as well as on the purpose of the distillation. Common methods include:
- Disposal: If the residue contains toxic or hazardous substances, it must be safely disposed of, taking into account environmental protection.
- Recycle: Some residues can be recycled or reused in other processes to reduce waste and improve efficiency.
- Further processing: Some residues are further processed to obtain additional products. For example, the residue from crude oil distillation can be further fractionated.
Examples of Residues
- Alcohol production: The residue, often referred to as “Stillsage”, contains non-fermentable materials and can be used as animal feed or to generate energy.
- Wine distillation: The residue can be further distilled to obtain an alcoholic spirit, or used in agriculture to improve the soil.
FAQ - Common Questions About Distillation
How Does Distillation Work?
During distillation, a mixture of liquids is separated by heating. Depending on the boiling point, the components evaporate one after the other. The steam is then condensed again in a cooling device and collected as a distillate. It is crucial that the ingredients have different boiling points.
What Is a Distillate?
The distillate is the product that is obtained during distillation. It is produced when the evaporated substance condenses and is collected in a collection container. The distillate is generally purer than the original mixture, as unwanted constituents remain.
What Is the Template for Distilling?
The receiver is the container in which the distillate is collected after condensation. It must be chemically resistant and have sufficient capacity for the condensed product. When distilling alcohol, the receiver is also known as a “collecting flask”.
What Is a Distillation Apparatus?
A distillation apparatus is the technical device that is used to carry out the distillation. It usually consists of the following parts:
- Heating source
- Distilling flask (to heat the liquid)
- Thermometer (for temperature monitoring)
- Cooling pipe or Liebig cooler (to condense the steam)
- Template (to collect the distillate)
Which Mixtures Can Be Separated by Distillation?
Distillation makes it possible to separate liquid mixtures whose components have different boiling points. Examples include:
- Alcohol-water mixtures
- Crude oil (in various fractions such as gasoline, diesel, etc.)
- Essential oils from plant mixtures in which the boiling points of the components are too close together are harder to separate.
What Are the Differences Between Simple and Fractional Distillation?
- Easy distillation: For mixtures with a large difference in boiling points. The liquid is heated and evaporates. The steam condenses and is collected as a distillate. Suitable for separating water and alcohol
- Fractional Distillation: For mixtures with close boiling points. A smoker column with fillers increases selectivity. The steam condenses several times in the column and enriches with the substance with a lower boiling point.
What Are the Differences and Similarities Between Fractional, Azeotropic and Dry Distillation?
- Fractional Distillation: Separates mixtures with close boiling points. Use a column to improve separation.
- Azeotropic Distillation: Separates mixtures that form an azeotrope, i.e. a mixture that cannot be separated by simple distillation. Additives or special techniques such as pressure change are used.
- Dry distillation: No liquids. Substances such as wood or coal are heated and chemically decompose. Gaseous and solid products are produced.
Commonalities: All processes use heat to separate the components of the starting material.
Differences: Scope of application, technology used and separation principle.
What Are the Advantages of Vacuum Distillation Over Atmospheric Distillation?
Vacuum distillation lowers the ambient pressure, which lowers the boiling points of the substances. Benefits include:
- Gentle distillation of heat-sensitive substances.
- Lower energy consumption.
- Preventing thermal decomposition.
Why Is Vacuum Used in Vacuum Distillation?
The vacuum lowers the pressure, which reduces the boiling points of the substances. This allows distillation to take place at lower temperatures. This is particularly important for heat-sensitive substances that would otherwise disintegrate.
Which Vacuum Pumps Are Used for Distilling?
The following vacuum pumps are mainly used for distilling:
- Diaphragm pumps: For low vacuum, ideal for sensitive substances.
- Rotary vane pumps: Generate medium to high vacuum, robust and reliable.
- Turbomolecular pumps: For very high vacuum levels, often used in the chemical industry.
Bonus items: What Types of Pumps Do Exist? Operating Modes & Applications
What Should Be Considered When Buying a Distillation System?
When buying a distillation system, you should pay attention to the following:
- Scope of application: Which mixture should be separated?
- Boiling point differences: Is a simple distillation sufficient or is a fractional distillation required?
- Material quality: Chemically resistant materials, such as borosilicate glass.
- Vacuum pump: If vacuum distillation is required, select a suitable pump.
- Scalability: Can the equipment be expanded for later requirements?
- Safety: Temperature and pressure monitoring systems.
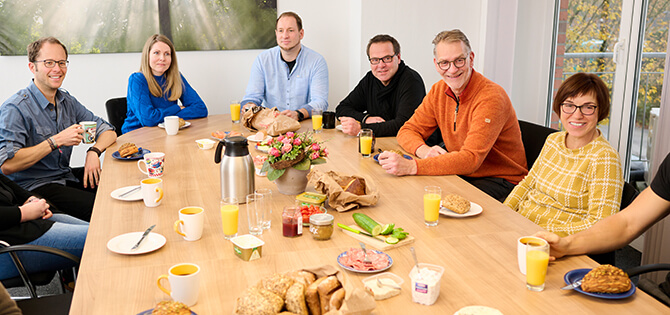
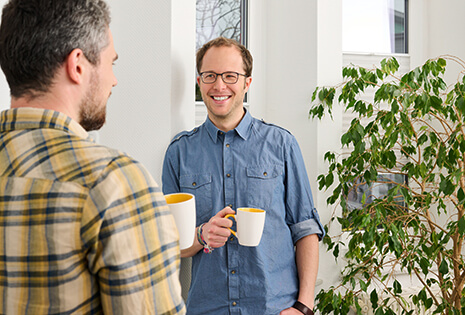
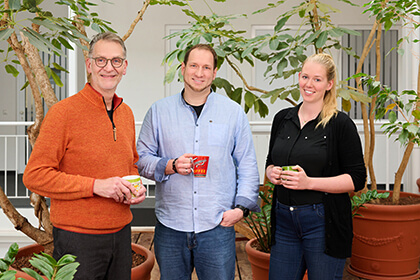
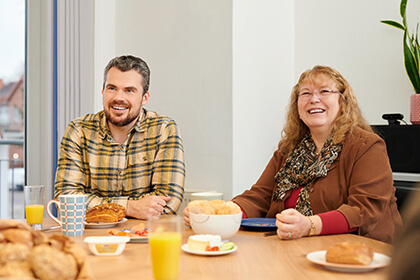
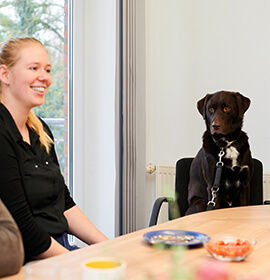
Are you an engineer or designer looking for new challenges? With us you can expect a familiar atmosphere and exciting tasks!
View Job Ads Now!