Principle of rectification
Rectification, also known as countercurrent distillation, is a thermal separation process that is used in process engineering to separate complex mixtures. It is based on the different volatilities of the individual components of a mixture, i.e. on their different boiling points. This is an extended form of distillation in which separation is significantly more efficient through a multi-stage process.
The basic principle of rectification is based on a countercurrent process of steam and liquid in a vertical column, the so-called column. The steam rises upwards from the bottom of the column and hits the liquid, which trickles down from above. As the steam rises, it contains more and more of the low-boiling components of the mixture. At the same time, the liquid that flows downwards absorbs more of the high-boiling components.
Mass and heat transfer
In the column, there is a continuous exchange of materials and heat between the rising vapor phase and the downflowing liquid phase. This involves highly volatile components evaporating from the liquid and turning into the gas phase. On the other hand, high-boiling components of the vapor condense and pass into the liquid. As a result of this process, the concentration of low-boiling substances in steam continues to increase, while the proportion of low-volatile components in the liquid increases.
The temperature in the system varies: In the bottom of the column, where the more volatile components are concentrated, the temperature is higher. In the upper area of the column, where the low-boiling components dominate, the temperature is lower. This temperature difference makes a significant contribution to separation.
Theoretical levels
An important aspect of rectification is the concept of so-called theoretical stages. A theoretical level represents an ideal mixture in which steam and liquid are in complete equilibrium. At each of these stages, an exchange takes place, which further changes the concentration of the components. In reality, a column is designed to simulate as many of these theoretical steps as possible in order to maximize separation.
Phase equilibrium
During the entire process, a phase equilibrium is established between the gas and liquid phases, which depends on temperature and pressure. This equilibrium defines how much of each substance is present in the gas or liquid phase. For pure substances and azeotropic mixtures, the gas and liquid phase compositions are identical. In all other cases, the concentration of the highly volatile substance is higher in the vapor phase than in the liquid, which makes separation easier.
Multiple evaporation and condensation
The repeated contact of steam and liquid in the column significantly increases the separating effect compared to simple distillation. Any contact between the two phases causes part of the vapor to condense and at the same time parts of the liquid to evaporate again. This continuous process enriches the more volatile components in the steam and the low-volatile components in the liquid.
Application principle
The process is used in particular when liquids with closely spaced boiling points must be separated. Rectification also makes it possible to separate substances whose boiling point difference is very small, sometimes less than one degree Celsius. This ability to achieve high levels of purity even with minimal differences in boiling point makes it an essential process for separating complex mixtures.
Advantages and disadvantages compared to other separation processes
Compared to other thermal separation processes, such as simple distillation, rectification offers a range of benefits:
- Higher separation effect: Compared to simple distillation, the separation effect during rectification is significantly more efficient. The steam is countercurrent to the liquid and comes into contact several times, which results in better separation of the components.
- Continuous operation: Rectification can be carried out continuously, which is particularly advantageous in industry. Continuous operation enables constant production without frequent interruptions.
- Energy efficiency: In contrast to multiple distillation, rectification is more energetically efficient. This is because the repeated contact processes in the column result in a more effective use of the energy used.
- Space-saving: Since a column allows multiple separation in a single system, it requires less space than connecting several simple distillation apparatuses in series.
- Technically less complex: By integrating the various separation steps in a column, the technical design and operation is less complicated than when arranging several distillation stages.
Despite its many advantages, rectification also has some drawbacks:
- Complex systems: Although the column system requires less space and works more efficiently, it is technologically more complex than simple distillation plants. Monitoring and control as well as pre-engineering require a high degree of technical knowledge and precision.
- Higher investment costs: The purchase costs for a rectification column are generally higher than for a simple distillation unit, which burdens the initial investment.
- Maintenance and repair: As rectification systems have complex column internals and are operated continuously, they require regular maintenance and professional consulting to ensure optimum operating conditions.
- High energy requirements for complex mixtures: Although rectification can be more energy efficient compared to other separation processes, energy requirements increase when very complex or azeotropic mixtures have to be separated.
Rectification plant: The column
In plant engineering, a rectification column is a special separation unit which is used to separate mixtures of substances, such as liquids, on the basis of their different boiling points. The column consists of several components which are required for effective separation.
Components of a column
- Sump: The lower part of the column, in which the more volatile component (heavy boiler) is collected and removed. There is also a heater here that supports evaporation.
- Head: The upper part of the column, where the more volatile component (low boiler) condenses and is removed. A condenser converts the vapor back into the liquid.
- Trays or packings: The liquid and the steam come into contact on the floors or in the packs. This interaction enables mass transfer, which results in the accumulation of low boilers in steam and heavy boilers in liquid.
- Evaporator (reboiler): It ensures the complete evaporation of the liquid collected in the sump and drives the steam upwards.
- Condenser: It cools the steam that rises from the head of the column and condenses it.
How an ideal column works
In an ideal column, the separation takes place into theoretical equilibrium levels, so-called “soils.” A soil represents a unit on which the equilibrium between the vapor and liquid phases takes place. In an ideal column with two trays and infinite return (i.e. no substance is removed), the steam flow is continuously enriched while the flow of liquid decreases downwards.
- On the first floor, some of the rising steam condenses, with more heavy boilers accumulating in the liquid and more low boilers accumulating in the steam.
- The enriched steam rises further upwards and reaches the second floor, where an equilibrium is once again established. In this way, the proportion of low boiler in steam is further increased, and this collects in the head of the column.
This ideal scenario describes a column in which the gas and liquid flows are always the same and the soils are in perfect thermodynamic equilibrium.
The real column
In practice, a real column never achieves the efficiency of an ideal column. This is where mass transfer effects come into play, which limit the separation efficiency. A soil column has a soil efficiency of around 0.7, which means that thermodynamic equilibrium on the soils is not fully achieved.
- Ground columns: They usually reach 0.7 to 2 theoretical levels per meter, depending on the type of soil (e.g. bell floors or slit floors).
- packing columns: There are no clear equilibrium levels here, and the separation efficiency is given in so-called theoretical steps per meter. Modern packings, such as structured fabric packings, reach up to 50 theoretical levels per meter.
The modeling, basic and detailed engineering and measurement of mass transfer in real columns is complex and requires expertise in several disciplines, as many factors influence efficiency. To determine the number of theoretical stages and the separation efficiency, engineers use experimental data and the so-called HTU-NTU method (Height of Transfer Unit, Number of Transfer Units).
Separation of azeotropic mixtures
Azeotropic mixtures are mixtures of substances which, at a certain mixing ratio and temperature, cannot be further separated by normal distillation or rectification. At this point, the mixture evaporates without changing the composition.
In order to separate azeotropic mixtures beyond the azeotropic point, the latter must be moved. There are various approaches to this:
- Pressure change: By increasing or lowering the operating pressure, the azeotropic point can be moved so that further separation is possible.
- Addition of an auxiliary: Another substance can be added to change azeotropic behavior. This adjuvant causes the components of the original mixture to evaporate and condense differently.
These methods also make it possible to separate azeotropic mixtures which would not be completely separable under normal conditions.
Continuous and discontinuous operation of columns
There are two main operating modes of columns: continuous and discontinuous (batch) operation.
- Continuous mode of operation: In this method, the mixture to be separated is fed continuously into the column (inflow) and the products (top and bottom product) are also removed continuously. The composition of the products remains constant since the column is in a quasi-stationary state. This means that the concentrations of the components on the theoretical plates of the column are stable. This mode of operation is ideal for large quantities of mixture that must be processed continuously.
- Discontinuous mode of operation: Here, a fixed amount of the mixture is introduced into the column. The column is operated until an equilibrium has been established on all theoretical soils. Then the product is removed, whether from the head or from the swamp. During this process, however, the composition of the mixture changes continuously, causing the balance on the soils to shift. As soon as the product no longer meets the desired specifications, the batch is canceled and a new one is started. This mode of operation is often used for smaller quantities or in laboratories.
Special processes for separating multi-component mixtures
Multi-component mixtures which either have azeotropic properties or have a low relative volatility require special processes to be effectively separated. Here are a few of the common methods:
- Dual pressure process (alternating pressure distillation): This process uses the fact that the azeotropic point of a mixture changes with pressure. By specifically changing the pressure, the separation of components such as tetrahydrofuran (THF) and water or ethanol and water can be made possible.
- Extractive rectification (Distex process): In this process, an adjuvant is added which changes the composition of the azeotrope. One example of this is the separation of benzene and cyclohexane by adding aniline. The adjuvant influences the volatility of the components and thus facilitates separation.
- Azeotrope correction: In this process, an auxiliary substance is also used which forms a new azeotrope with one of the components of the azeotropic mixture. This method is often used when there are close-boiling mixtures or existing azeotropes. The adjuvant can either be a component of the new azeotrope or act as an azeotrope converter and enable separation.
Rectification evaluation method
The McCabe-Thiele process
The McCabe-Thiele method is a graphical method for analyzing rectification based on the equilibrium diagram of the underlying mixture of substances. In this diagram, the molar fractions of the lighter boiling component in the liquid phase are compared with the corresponding proportions in the gas phase. It is important that the process takes place at constant pressure, which results in an isobaric equilibrium diagram.
In this diagram, isolines for the liquid and gas phases are plotted, and the operating and equilibrium lines are plotted. By drawing in horizontal and vertical lines (steps between phases) step by step, the number of theoretical plates in a column can be determined. These floors represent the individual steps that are necessary to completely separate the components.
The McCabe-Thiele method provides an easy way to graphically determine separation efficiency and is often used to study the effects of operating parameters such as the return ratio.
The Ponchon-Savarit process
The Ponchon-Savarit process is an extension of the McCabe-Thiele process, which also includes energy balances in the analysis of rectification. This is done by using an enthalpy composition diagram (H (x, y)). Both the material flows and the energy balances of the phase transitions are taken into account.
In contrast to the McCabe-Thiele process, which only looks at the balance of substances, the Ponchon-Savarit process also analyses the energy exchange between the liquid and gas phases. This makes it possible to make more precise statements about energy requirements and the course of the process. The energy consumption of the individual separation steps is also shown graphically, which makes it possible to size the column more precisely.
The Ponchon-Savarit process requires more input data and is computationally more complex, but provides more realistic results, particularly when thermodynamic effects play an important role.
Applications and areas of application of rectification
Applications in industry
In industry, rectification is a widely used process for separating mixtures of substances. The most important industrial applications include separating components based on their different boiling points.
- Petroleum refining: In the petroleum industry, rectification is used to separate crude oil into various fractions such as gasoline, kerosene, diesel and heavy oil. Crude oil is processed in multi-stage distillation columns. In addition, water vapor is used to minimize undesired reactions and to increase separation efficiency.
- Air separation: Using the Linde process, air is liquefied and broken down into its main components — nitrogen, oxygen and argon — through rectification. Larger plants also obtain a mixture of helium and neon, which is then further separated.
- Alcohol production: In the production of whiskey and other spirits, rectification is used to increase the alcohol content and remove unwanted substances. Irish whiskey, for example, is distilled in a bubble with an attached booster column, while Scottish whiskey is distilled twice in a row.
- Alternative fuels: Separating methanol or ethanol from water is a common use of rectification in the production of alternative fuels.
- Chemical industry: Rectification is often used in chemical production to separate solvents from water or other compounds. Examples include acetone/water, butyl acetate/water and glycerin/water.
There are also applications in the fiber industry, where solvent/water mixtures are separated from spinning baths. Rectification also plays a central role in the production of lactic acid or the recovery of solvents.
Applications in the laboratory
In the laboratory, rectification is primarily used for syntheses and purification of substances. When liquids with similar boiling points need to be separated, rectification provides a precise method to ensure high purity of the substances.
- Separation of liquid mixtures: When synthesizing chemical compounds or isolating natural substances, it is often necessary to separate liquid mixtures that have boiling points close together. The selection of the rectification column depends on the difference in boiling point. A common column in the laboratory is the Vigreux column, which is suitable for smaller boiling point differences.
- Purification of substances: In many organic syntheses, rectification is essential to remove impurities from the reaction mixture. Rectification makes it possible to obtain high-purity products that are required for further experiments.
Industrial processes and laboratories use rectification for a variety of separation processes based on the difference in boiling points, with applications being found both in large-scale plants and in precise, scientific experiments.
FAQ: Frequently asked questions
What is the difference between rectification and distillation?
Rectification and distillation are both thermal separation processes to separate liquid mixtures of substances. The main difference lies in the repetition of the separation process:
- Distillation: Distillation involves a one-time evaporation and condensation. The mixture is heated, the components with lower boiling points evaporate first and are then separated off.
- Rectification: During rectification, on the other hand, the separation process is repeated several times. The steam is continuously condensed and evaporated again, with fractional separation taking place over many stages (e.g. in a column). As a result, a higher purity of the separated substances can be achieved.
What is the return ratio during rectification?
The reflux ratio is the ratio between the part of the condensed steam that is returned to the column and the part that is withdrawn as a product. A higher reflux ratio improves separation efficiency as more liquid circulates in the column, which increases the interaction between steam and liquid. This results in better separation of the components, but also requires more energy. An optimal return ratio is therefore crucial for rectification efficiency.
What options are there for energy optimization?
There are various approaches to improve energy efficiency during rectification:
- Heat integration: By using waste heat, the energy released when the steam condenses can be used for the evaporation process.
- Multiple effect rectification: In this process, the heat of evaporation from one column is used for a second column in order to reduce energy consumption.
- Vacuum rectification: By working at reduced pressure, the boiling point of the components can be reduced, which reduces energy consumption.
- Optimizing the return ratio: An adjusted return ratio that takes into account the balance between separation efficiency and energy consumption can minimize overall energy consumption.
- Improved heat exchangers: High-performance heat exchangers can help to increase thermal efficiency by minimizing heat loss.
- Multi-level systems: In multi-stage rectification plants, evaporation energy can be used gradually, which reduces overall energy consumption.
- Mechanical vapor compaction: This compresses the vapor (vapors) produced by evaporation, which brings it to a higher pressure and temperature level and can be used again for heating.
- Thermal vapor densification: By using heat, the vapor is brought to a higher temperature so that it can be used again in the process for evaporation, which reduces the energy requirement for heating.
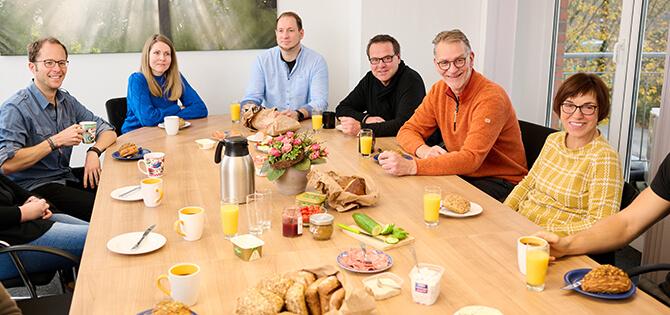
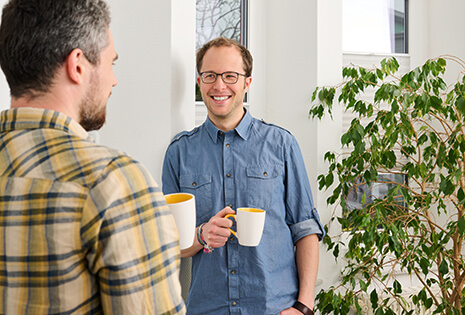
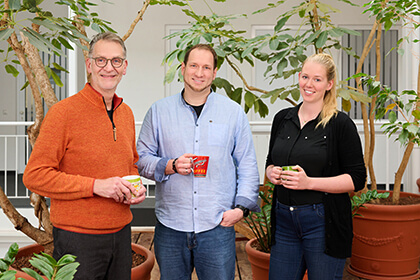
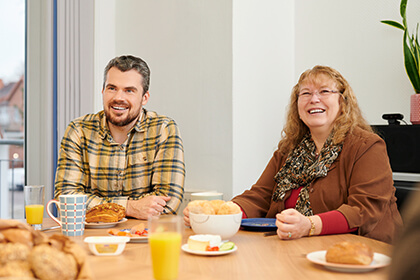
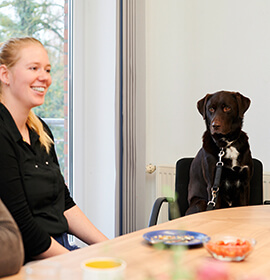
Are you an engineer or designer looking for new challenges? With us you can expect a familiar atmosphere and exciting tasks!
View Job Ads Now!