Definition: What is dispersion?
Dispersion means the mixing of at least two substances which do not or only with difficulty dissolve in one another or combine chemically with one another. In this case, a substance, the so-called disperse phase (also known as dispersed phase, inner phase or secondary phase), is finely distributed in another substance, the continuous phase (also known as dispersion medium, dispersing agent, continuous phase, outer phase or main phase). The aim of dispersion is to produce a homogeneous mixture in which the substances remain in a stable ratio to one another. Important examples of dispersions include emulsions and suspensions.
When dispersing, there is no chemical reaction between the substances. It is only through mechanical forces that a distribution of the particles is achieved in order to increase the interfaces between the phases. As a result, the formation of a homogeneous mixture can be supported, as the interfacial tension between the phases often hinders the formation of a dispersion. In many cases, dispersion requires a fine and uniform distribution of the particles in order to ensure the greatest possible stability of the dispersion.
Dispersion objectives
The main goal of dispersion is to produce a fine, stable distribution of solid particles, liquid droplets, or gas bubbles in a liquid medium. The following goals are particularly important:
- Preparation of emulsions or suspensions: In many industrial applications, a liquid or solid phase should be evenly distributed in another medium. In an emulsion, both phases are liquid, while in a suspension, solid particles are distributed in a liquid.
- Maximize interfaces: In order to create a stable dispersion, the interface between the phases must be enlarged. This is achieved by crushing the particles so that they are evenly distributed in the medium.
- Long-term stability of the dispersion: To ensure that the dispersion remains stable, emulsifiers or stabilizers are often added to prevent agglomerates from regressing. This ensures that the disperse phase does not separate or clump from the continuous phase.
Dispersion applications
Dispersion plays a crucial role in many industrial and scientific areas. Typical applications include:
- Paints and varnishes: The dispersion of pigments in binders is decisive for the color power, opacity and shine of paints and varnishes. The aim here is to distribute pigment particles as finely and evenly as possible in order to achieve optimal optical and physical properties.
- Pharmaceutical industry: In the manufacture of drugs, solid active ingredients are dispersed in liquids to produce suspensions or solutions. This ensures uniform dosing and improved bioavailability of the active ingredients.
- Food industry: Dispersing is used in the production of foods, such as dressings or chocolate spreads, to ensure a homogeneous distribution of the ingredients.
- Cosmetics: In creams, lotions or makeup products, dispersion is used to evenly distribute active ingredients, pigments and fillers and create a pleasant texture.
- Nanotechnology: In the research and production of nanomaterials, dispersion is crucial to evenly distribute nanoparticles and thus achieve the desired properties, such as coatings or additives.
Classification of disperse systems
Classification by particle size
Disperse systems can be divided into three main categories based on the size of their particles:
- Molecularly dispersed system
- Particle size: < 1 nm
- Traits: The boundaries between the dispersive phase and the dispersion medium are not visible. Molecules or atoms are so finely distributed that no optical methods can separate them. However, mechanical separations are possible through nanofiltration. Gas mixtures can be enriched or separated by cascades of gas centrifuges.
- Examples: Real solutions, such as salt in water or gas mixtures in fluid phases.
- Colloidally dispersed system
- Particle size: 1 nm to 1 µm
- Traits: The boundaries between the dispersive phase and the dispersion medium are visible under an ultramicroscope. The particles show Brownian motion, which is due to the thermal movement of the liquid. Separation by ultracentrifuges or ultrafiltration is possible with liquid dispersions.
- Examples: protein solutions, gelatin, latex.
- Coarsely dispersed system
- Particle size: > 1 µm
- Traits: The boundaries between the dispersive phase and the dispersion medium are often visible even without a microscope. The particles are large enough that Brownian motion is no longer noticeable. Separations are possible by conventional centrifuges or filtration.
- Examples: Milk fat globules in milk, suspensions such as sand in water.
When all particles in a dispersion have a similar size, we speak of a monodisperse, homodisperse or isodisperse system. When the particles have different sizes, this is referred to as heterodisperse or polydisperse system.
Classification by aggregate states
Disperse systems can also be classified based on the aggregate states of the dispersive phase and the dispersion medium. There are a total of eight types of dispersion based on two-phase systems:
- Emulsion
- Disperse phase: Liquid
- Dispersion medium: Liquid
- Examples: Milk, butter, skin creams, lotions.
- Suds
- Disperse phase: Gas
- Dispersion medium: Liquid
- Examples: Soap foam, sparkling wine, cola foam, whipped cream.
- Suspension
- Disperse phase: Solid
- Dispersion medium: Liquid
- Examples: Lime milk, naturally cloudy apple juice, marmalade.
- Aerosol (liquid)
- Disperse phase: Liquid
- Dispersion medium: Gas
- Examples: Fog, clouds, sprays.
- Aerosol (solid)
- Disperse phase: Solid
- Dispersion medium: Gas
- Examples: Smoke, particulate matter, sandstorms.
- Porous solid (thoroughly moistened)
- Disperse phase: Liquid
- Dispersion medium: Solid
- Examples: Wet sponge, damp brick, turbidity in amber.
- Porous solid (dry)
- Disperse phase: Gas
- Dispersion medium: Solid
- Examples: foam, porous concrete, metal foam.
- Solid mix
- Disperse phase: Solid
- Dispersion medium: Solid
- Examples: Granite, pigments in cured paints.
Assigning the phase to a solid or liquid aggregate state can sometimes be difficult. Both finely divided solid and liquid substances in a gaseous disperser can show similar flow properties.
Devices: Which dispersing units are there?
Dispersing uses various dispersing units, each of which has specific properties and functions. In the following, you will learn more about the most important devices used for dispersion, as well as their advantages and disadvantages.
Dissolver
The dissolver is used for easily wettable materials such as pigments. It works with a serrated agitator that rotates at a high circumferential speed. These velocities are generally 20 to 25 m/s. Higher velocities increase the shear forces, which results in the agglomerates being comminuted, but also causes the temperature of the medium to rise. Dissolvers are particularly suitable for low to medium viscosity substances and are often used for pre-dispersion.
- Advantages: Suitable for low to medium viscosity systems.
- Drawback: Not suitable for highly viscous or difficult to disperse substances.
Kneader
A kneader is primarily used for pasty systems. The kneading tools move the materials against each other or against a fixed surface, resulting in mixing and pre-dispersion. This device is particularly suitable for systems with high viscosity where other dispersing units are reaching their limits.
- Advantages: Efficient when processing highly viscous, pasty substances.
- Drawback: More suitable for pre-dispersion, less suitable for fine crushing.
Three-roller
The three-roller consists of three rotating rollers (feed roller, middle roller, removal roller), which rotate in a ratio of 1:3:9 with respect to each other. The dispersing material is guided into the gap between the feed roll and the middle roll and is then further processed between the middle and removal roller. Agglomerates are crushed by squeezing and shearing. Because of the high solvent losses, the three-roller is mainly used for pasty, low-solvent systems.
- Advantages: Very good adjustability of the effect intensity, particularly suitable for pasty materials.
- Drawbacks: High solvent loss and the rollers require continuous monitoring.
Ball mill
The ball mill is a cylindrical container that is half filled with metal, steatite or porcelain balls. The agglomerates are crushed by the movements of the balls caused by sliding and rolling.
- Advantages: Easy to operate as it is a closed system, which causes hardly any solvent losses. No need for constant monitoring.
- Drawbacks: Long running times, heavy cleaning costs, discontinuous operation, noise pollution and large machinery required.
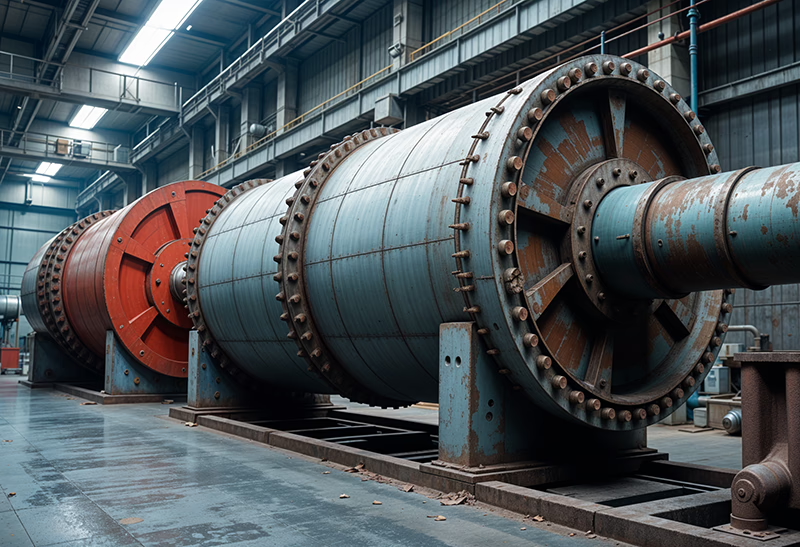
Agitator mill and agitator ball mill
The agitator mill is a container with a central shaft on which stirrer discs are mounted. The container is filled with fillers (pearls) up to 60— 80%. When the shaft rotates, the agglomerates are crushed by the shear forces between the beads. The denser the pearls, the more intensive the dispersion. There are glass beads, ceramic beads, and zirconia beads. Finer beads allow faster and more efficient crushing but require careful pre-dispersion.
- Advantages: Continuous operation possible, no solvent emissions, fast operation.
- Drawbacks: High cleaning costs and abrasion when using hard pearls.
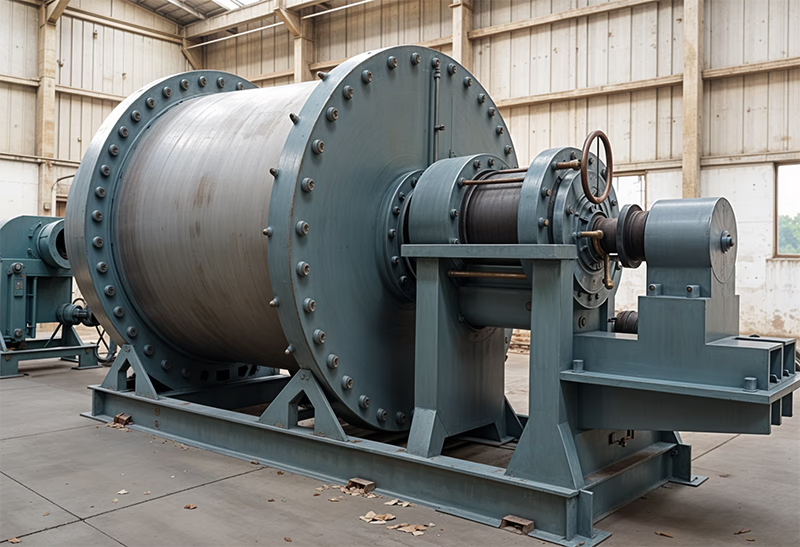
Extruder
The extruder, in particular the co-spin twin screw extruder, is mainly used to disperse plastic mixtures, powder coatings, pigments and additives. The dispersing material is processed by the shear forces between the screws and the wall.
- Advantages: Efficient processing of solid and viscous materials, continuous working method.
- Drawbacks: Complexity of cleaning and adjustment.
Co-spin twin screw extruder
The co-spin twin screw extruder has two parallel screws that rotate in the same direction. This type of extruder produces strong shear forces that contribute to the shredding and homogenization of solid and highly viscous materials. It is often used in the processing of powders, pigments and additives.
- Advantage: Very efficient dispersion of hard-to-disperse solids.
- Drawback: High technical effort and complex cleaning.
Dispersion process
There are two basic methods of dispersion: dry dispersion and wet dispersion. Both methods aim to make the distribution of dispersed substances in a carrier material as uniform as possible, using different physical principles.
Dry dispersion
Dry dispersion involves the processing of free-flowing solids. These solids must be processed in such a way that the particles can be evenly distributed. For this to succeed, it is necessary to overcome the binding forces that exist between the individual particles. When dry, these binding forces are significantly stronger, as there is no liquid that reduces the adhesive forces between the particles.
To achieve this, mechanical processes are used which generate intensive shear and frictional forces to separate the particles from one another and distribute them evenly in the carrier material. Dry dispersion is often used for solids that must be processed without liquid and is generally more energy-intensive than wet dispersion.
Wet dispersion
Wet dispersion takes place when the substances to be dispersed are already dissolved in a liquid or are present as a wet system. This applies to systems such as suspensions, emulsions or gels. Wet dispersion is much easier than dry dispersion because the adhesive forces between particles in a liquid are significantly lower. As a result, the particles can be separated from one another and evenly distributed with significantly less energy consumption.
This process is used in particular when the substances have a strong tendency to agglomerate, i.e. to form clumps or aggregates. Dispersing in liquid reduces the risk of such clumps and enables a more uniform distribution of the particles.
However, wet dispersion also has a significant disadvantage: If the end product is a solid or a mixture of solids, an additional process step may be necessary. One example would be to disperse a powder in a liquid and then mix it again with a solid carrier material. This additional step increases effort and can make product development more complicated.
Completion of the dispersing material
During dispersion, completing the dispersing material is an important step which takes place after the pigments or fillers have been dispersed. In this last step, you add all remaining components that are necessary for the finished system, such as binders, solvents, additives, or other liquid components.
Particular care must be taken to avoid a so-called solvent shock. This can occur when the pigment precipitates due to sudden and uncontrolled addition of solvents. The pigments, which have previously been finely distributed in the liquid, can combine again to form larger aggregates when added too quickly. This not only affects the optical properties but also the mechanical and chemical properties of the end product.
How to avoid solvent shock
- Slow and steady addition: Add the remaining ingredients, especially solvents, slowly and with constant stirring. This helps to minimize the risk of pigment loss.
- Temperature control: Make sure that the system temperature remains constant. Temperature fluctuations can influence the interactions between the pigments and the solvent and thus interfere with the dispersion process.
- Adjust the mixing speed: Choose an appropriate mixing speed that is strong enough to ensure even distribution, but gentle enough to avoid shear forces that could lead to adverse reactions.
These precautionary measures are crucial to achieve a homogeneous end product and to ensure that all components in the paint or dispersion remain stable. A cleanly carried out completion of the dispersing material is therefore essential for the quality of the end product.
FAQ about dispersing
Can be dispersed in water?
Yes, many substances can be dispersed in water. Water is often used as a dispersing agent (or dispersing agent) for the distribution of solids or liquids in a continuous phase. For dispersion in water to be efficient, dispersants must be added, which increase particle stability and allow uniform distribution.
What are dispersants?
Dispersants are additives that help distribute particles evenly in a liquid medium. They prevent particles from clumping (agglomeration) and improve the stability of the dispersion. Dispersants are used in various industries, such as in paint and varnish production or in the production of nanoparticles.
What is the doughnut effect in a dissolver?
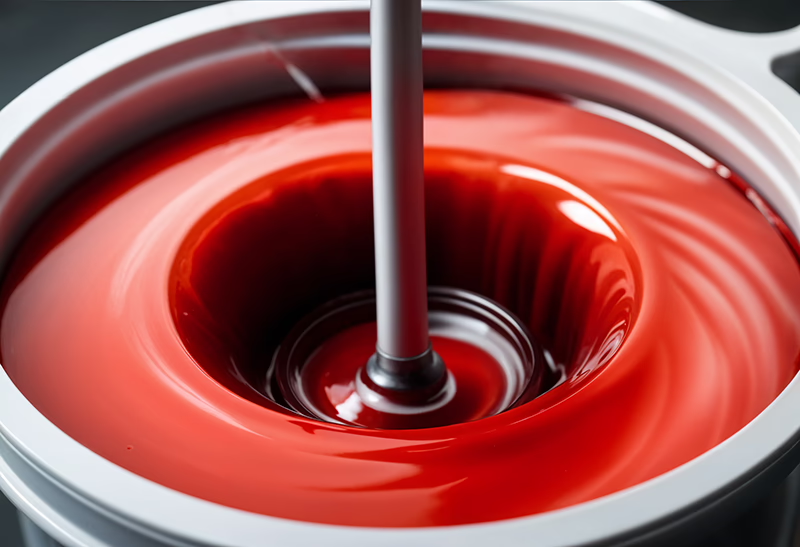
The doughnut effect describes a specific flow pattern that occurs during the dispersion process around the rotating toothed disc of the dissolver. This structure is an indicator that energy is optimally transferred to the material to be dispersed. A successful doughnut effect signals that the particles are being shredded and distributed efficiently.
Key factors for the doughnut effect:
- The diameter of the tooth pulley in relation to the diameter of the container
- The height of the toothed disc above the bottom of the container
- The filling height of the material
- The circumferential speed of the tooth disc (at least 20 m/s)
If the speed is too low, the material is simply stirred and no doughnut effect occurs. Too low a viscosity causes the base to foam and splatter, while too high a viscosity causes the material to stagnate and not all pigments reach the tooth disc.
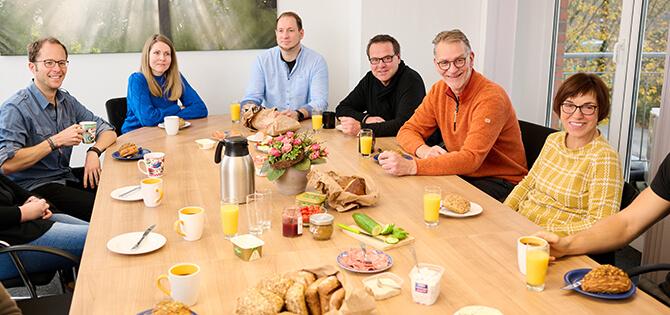
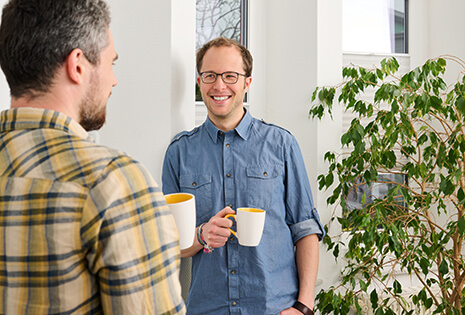
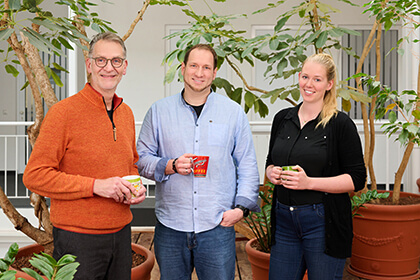
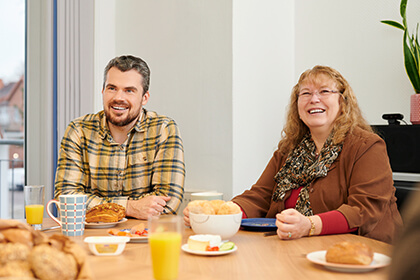
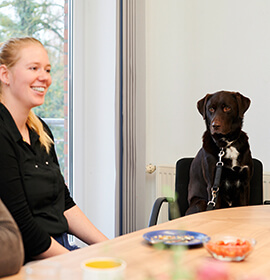
Are you an engineer or designer looking for new challenges? With us you can expect a familiar atmosphere and exciting tasks!
View Job Ads Now!