Definition: Was ist Dispergieren?
Dispergieren bezeichnet das Mischen von mindestens zwei Stoffen, die sich nicht oder nur schwer ineinander lösen oder chemisch miteinander verbinden. Dabei wird ein Stoff, die sogenannte disperse Phase (auch dispergierte Phase, innere Phase oder Nebenphase genannt), fein in einem anderen Stoff, der kontinuierlichen Phase (auch Dispersionsmedium Dispersionsmittel, Dispergens, kontinuierliche Phase, äußere Phase oder Hauptphase genannt), verteilt. Ziel des Dispergierens ist die Herstellung einer homogenen Mischung, bei der die Stoffe in einem stabilen Verhältnis zueinander bleiben. Wichtige Beispiele für Dispersionen sind Emulsionen und Suspensionen.
Beim Dispergieren erfolgt keine chemische Reaktion zwischen den Stoffen. Es wird lediglich durch mechanische Kräfte eine Verteilung der Partikel erreicht, um die Grenzflächen zwischen den Phasen zu vergrößern. Dadurch kann die Bildung einer homogenen Mischung unterstützt werden, da die Grenzflächenspannung zwischen den Phasen die Entstehung einer Dispersion oft behindert. In vielen Fällen kommt es bei der Dispergierung auf eine feine und gleichmäßige Verteilung der Partikel an, um eine möglichst große Stabilität der Dispersion zu gewährleisten.
Ziele der Dispergierung
Das Hauptziel der Dispergierung ist die Erzeugung einer feinen, stabilen Verteilung von Feststoffpartikeln, Flüssigkeitströpfchen oder Gasblasen in einem flüssigen Medium. Dabei sind folgende Ziele besonders wichtig:
- Herstellung von Emulsionen oder Suspensionen: In vielen industriellen Anwendungen soll eine Flüssigkeit oder Feststoffphase gleichmäßig in einem anderen Medium verteilt werden. In einer Emulsion sind beide Phasen flüssig, während in einer Suspension feste Partikel in einer Flüssigkeit verteilt werden.
- Maximierung der Grenzflächen: Um eine stabile Dispersion zu schaffen, muss die Grenzfläche zwischen den Phasen vergrößert werden. Dies wird durch Zerkleinerung der Partikel erreicht, sodass sie sich gleichmäßig im Medium verteilen.
- Langzeitstabilität der Dispersion: Damit die Dispersion stabil bleibt, werden oft Emulgatoren oder Stabilisatoren hinzugefügt, um die Rückbildung von Agglomeraten zu verhindern. Dies sorgt dafür, dass sich die disperse Phase nicht von der kontinuierlichen Phase absetzt oder klumpt.
Anwendungen der Dispergierung
Dispergierung spielt in vielen industriellen und wissenschaftlichen Bereichen eine entscheidende Rolle. Typische Anwendungen sind:
- Farben und Lacke: Die Dispergierung von Pigmenten in Bindemitteln ist entscheidend für die Farbkraft, Deckkraft und den Glanz von Farben und Lacken. Hier ist das Ziel, Pigmentpartikel möglichst fein und gleichmäßig zu verteilen, um optimale optische und physikalische Eigenschaften zu erreichen.
- Pharmazeutische Industrie: In der Herstellung von Medikamenten werden feste Wirkstoffe in Flüssigkeiten dispergiert, um Suspensionen oder Lösungen zu erzeugen. Dies sorgt für eine gleichmäßige Dosierung und eine verbesserte Bioverfügbarkeit der Wirkstoffe.
- Lebensmittelindustrie: Bei der Herstellung von Lebensmitteln, wie z. B. Dressings oder Schokoladenaufstrichen, wird Dispergieren eingesetzt, um eine homogene Verteilung der Zutaten zu gewährleisten.
- Kosmetik: In Cremes, Lotionen oder Make-up-Produkten wird die Dispergierung genutzt, um Wirkstoffe, Pigmente und Füllstoffe gleichmäßig zu verteilen und eine angenehme Textur zu schaffen.
- Nanotechnologie: In der Forschung und Produktion von Nanomaterialien ist die Dispergierung entscheidend, um Nanopartikel gleichmäßig zu verteilen und damit die gewünschten Eigenschaften wie etwa bei Beschichtungen oder Additiven zu erzielen.
Einteilung disperser Systeme
Einteilung nach Teilchengröße
Disperse Systeme lassen sich nach der Größe ihrer Teilchen in drei Hauptkategorien unterteilen:
- Molekulardisperses System
- Teilchengröße: < 1 nm
- Merkmale: Die Grenzen zwischen der dispersiven Phase und dem Dispersionsmedium sind nicht sichtbar. Moleküle oder Atome sind so fein verteilt, dass keine optischen Methoden sie trennen können. Mechanische Trennungen sind jedoch durch Nanofiltration möglich. Bei Gasgemischen können durch Kaskaden von Gaszentrifugen Anreicherungen oder Abtrennungen stattfinden.
- Beispiele: Echte Lösungen, wie Salz in Wasser oder Gasgemische in fluiden Phasen.
- Kolloiddisperses System
- Teilchengröße: 1 nm bis 1 µm
- Merkmale: Die Grenzen zwischen der dispersiven Phase und dem Dispersionsmedium sind unter einem Ultramikroskop sichtbar. Die Teilchen zeigen eine Brownsche Bewegung, die auf die thermische Bewegung der Flüssigkeit zurückzuführen ist. Trennung durch Ultrazentrifugen oder Ultrafiltration ist bei flüssigen Dispersionen möglich.
- Beispiele: Proteinlösungen, Gelatine, Latex.
- Grobdisperses System
- Teilchengröße: > 1 µm
- Merkmale: Die Grenzen zwischen der dispersiven Phase und dem Dispersionsmedium sind oft auch ohne Mikroskop sichtbar. Die Teilchen sind groß genug, dass die Brownsche Bewegung nicht mehr bemerkbar ist. Trennungen sind durch gewöhnliche Zentrifugen oder Filtration möglich.
- Beispiele: Milchfettkügelchen in Milch, Suspensionen wie Sand in Wasser.
Wenn alle Teilchen in einer Dispersion eine ähnliche Größe haben, spricht man von einem monodispersen, homodispersen oder isodispersen System. Wenn die Teilchen unterschiedliche Größen haben, bezeichnet man dies als heterodisperses oder polydisperses System.
Einteilung nach Aggregatzuständen
Disperse Systeme können auch anhand der Aggregatzustände der dispersiven Phase und des Dispersionsmediums klassifiziert werden. Es gibt insgesamt acht Dispersionsarten, die auf zweiphasigen Systemen basieren:
- Emulsion
- Disperse Phase: Flüssig
- Dispersionsmedium: Flüssig
- Beispiele: Milch, Butter, Hautcremes, Lotionen.
- Schaum
- Disperse Phase: Gas
- Dispersionsmedium: Flüssig
- Beispiele: Seifenschaum, Sekt, Colaschaum, Schlagsahne.
- Suspension
- Disperse Phase: Fest
- Dispersionsmedium: Flüssig
- Beispiele: Kalkmilch, naturtrüber Apfelsaft, Marmelade.
- Aerosol (flüssig)
- Disperse Phase: Flüssig
- Dispersionsmedium: Gas
- Beispiele: Nebel, Wolken, Sprays.
- Aerosol (fest)
- Disperse Phase: Fest
- Dispersionsmedium: Gas
- Beispiele: Rauch, Feinstaub, Sandstürme.
- Poröser Festkörper (durchfeuchtet)
- Disperse Phase: Flüssig
- Dispersionsmedium: Fest
- Beispiele: Nasser Schwamm, feuchter Backstein, Trübung in Bernstein.
- Poröser Festkörper (trocken)
- Disperse Phase: Gas
- Dispersionsmedium: Fest
- Beispiele: Schaumstoff, Porenbeton, Metallschaum.
- Feste Mischung
- Disperse Phase: Fest
- Dispersionsmedium: Fest
- Beispiele: Granit, Pigmente in ausgehärteten Anstrichen.
Dabei kann die Zuordnung der Phase zu einem festen oder flüssigen Aggregatzustand manchmal schwierig sein. Sowohl fein verteilte feste als auch flüssige Stoffe in einem gasförmigen Dispergens können ähnliche Fließeigenschaften zeigen.
Geräte: Welche Dispergieraggregate gibt es?
Beim Dispergieren werden verschiedene Dispergieraggregate eingesetzt, die jeweils spezifische Eigenschaften und Funktionsweisen aufweisen. Im Folgenden erfährst Du mehr über die wichtigsten Geräte, die für die Dispergierung genutzt werden, sowie ihre Vor- und Nachteile.
Dissolver
Der Dissolver wird für leicht benetzbare Materialien wie Pigmente verwendet. Er arbeitet mit einer gezahnten Rührscheibe, die mit hoher Umfangsgeschwindigkeit rotiert. Diese Geschwindigkeiten liegen in der Regel bei 20 bis 25 m/s. Höhere Geschwindigkeiten erhöhen die Scherkräfte, was zur Zerkleinerung der Agglomerate führt, jedoch auch die Temperatur des Mediums steigen lässt. Dissolver eignen sich besonders gut für niedrig- bis mittelviskose Stoffe und werden oft zur Vordispergierung eingesetzt.
- Vorteil: Geeignet für niedrig- bis mittelviskose Systeme.
- Nachteil: Nicht für hochviskose oder schwer dispergierbare Stoffe geeignet.
Kneter
Ein Kneter wird vorwiegend für pastöse Systeme eingesetzt. Die Knetwerkzeuge bewegen die Materialien gegeneinander oder gegen eine feststehende Fläche, wodurch eine Vermischung und Vordispergierung erreicht wird. Dieses Gerät eignet sich vor allem für Systeme mit hoher Viskosität, bei denen andere Dispergieraggregate an ihre Grenzen stoßen.
- Vorteil: Effizient bei der Verarbeitung von hochviskosen, pastösen Stoffen.
- Nachteil: Eher zur Vordispergierung geeignet, weniger für Feinzerkleinerung.
Dreiwalze
Die Dreiwalze besteht aus drei rotierenden Walzen (Aufgabewalze, Mittelwalze, Abnahmewalze), die im Verhältnis 1:3:9 zueinander rotieren. Das Dispergiergut wird in den Spalt zwischen der Aufgabewalze und der Mittelwalze geführt und danach zwischen der Mittel- und Abnahmewalze weiter verarbeitet. Durch das Quetschen und Scheren werden Agglomerate zerkleinert. Wegen der hohen Lösemittelverluste wird die Dreiwalze hauptsächlich für pastöse, lösemittelarme Systeme verwendet.
- Vorteile: Sehr gute Einstellbarkeit der Wirkungsintensität, besonders geeignet für pastöse Materialien.
- Nachteile: Hoher Lösemittelverlust und die Walzen erfordern stetige Überwachung.
Kugelmühle
Die Kugelmühle ist ein zylinderförmiger Behälter, der zur Hälfte mit Kugeln aus Metall, Steatit oder Porzellan gefüllt ist. Die Agglomerate werden durch die Bewegungen der Kugeln, welche durch Rutschen und Rollen entstehen, zerkleinert.
- Vorteile: Einfach zu bedienen, da es sich um ein geschlossenes System handelt, was kaum Lösemittelverluste verursacht. Keine ständige Überwachung notwendig.
- Nachteile: Lange Laufzeiten, großer Reinigungsaufwand, diskontinuierlicher Betrieb, Lärmbelästigung und großer Maschinenpark erforderlich.

Rührwerksmühle und Rührwerkskugelmühle
Die Rührwerksmühle ist ein Behälter mit einer zentralen Welle, auf der Rührscheiben montiert sind. Der Behälter wird mit Füllkörpern (Perlen) zu 60–80% gefüllt. Wenn die Welle rotiert, werden die Agglomerate durch die Scherkräfte zwischen den Perlen zerkleinert. Je dichter die Perlen, desto intensiver die Dispergierung. Es gibt Glasperlen, Keramikperlen und Zirkonoxidperlen. Feinere Perlen ermöglichen eine schnellere und effizientere Zerkleinerung, erfordern jedoch eine sorgfältige Vordispergierung.
- Vorteile: Kontinuierlicher Betrieb möglich, keine Lösemittelemissionen, schnelle Arbeitsweise.
- Nachteile: Hoher Reinigungsaufwand und Abrasion bei der Verwendung von harten Perlen.

Extruder
Der Extruder, insbesondere der Gleichdrall-Doppelschneckenextruder, wird hauptsächlich zur Dispergierung von Kunststoffmischungen, Pulverlacken, Pigmenten und Additiven eingesetzt. Dabei wird das Dispergiergut durch die Scherkräfte zwischen den Schnecken und der Wand verarbeitet.
- Vorteile: Effiziente Verarbeitung von festen und viskosen Materialien, kontinuierliche Arbeitsweise.
- Nachteile: Komplexität der Reinigung und Einstellung.
Gleichdrall-Doppelschneckenextruder
Der Gleichdrall-Doppelschneckenextruder hat zwei parallele Schnecken, die in dieselbe Richtung rotieren. Diese Art von Extruder erzeugt starke Scherkräfte, die zur Zerkleinerung und Homogenisierung von festen und hochviskosen Materialien beitragen. Er wird häufig bei der Verarbeitung von Pulvern, Pigmenten und Additiven eingesetzt.
- Vorteil: Sehr effiziente Dispergierung schwer dispergierbarer Feststoffe.
- Nachteil: Hoher technischer Aufwand und komplexe Reinigung.
Verfahren zur Dispergierung
Es gibt zwei grundlegende Verfahren, die bei der Dispergierung unterschieden werden: Trockendispergierung und Nassdispergierung. Beide Verfahren zielen darauf ab, die Verteilung der dispergierten Stoffe in einem Trägermaterial so gleichmäßig wie möglich zu gestalten, wobei unterschiedliche physikalische Prinzipien zum Einsatz kommen.
Trockendispergierung
Bei der Trockendispergierung geht es um die Verarbeitung von rieselfähigen Feststoffen. Diese Feststoffe müssen so aufbereitet werden, dass die Partikel gleichmäßig verteilt werden können. Damit das gelingt, ist es notwendig, die Bindungskräfte, die zwischen den einzelnen Partikeln bestehen, zu überwinden. In trockenem Zustand sind diese Bindungskräfte deutlich stärker, da es keine Flüssigkeit gibt, die die Adhäsionskräfte zwischen den Partikeln reduziert.
Um dies zu erreichen, kommen mechanische Verfahren zum Einsatz, die intensive Scher- und Reibungskräfte erzeugen, um die Partikel voneinander zu trennen und gleichmäßig im Trägermaterial zu verteilen. Trockendispergierung wird häufig bei Feststoffen angewendet, die ohne Flüssigkeit verarbeitet werden müssen, und ist in der Regel energieaufwendiger als die Nassdispergierung.
Nassdispergierung
Die Nassdispergierung erfolgt, wenn die zu dispergierenden Stoffe bereits in einer Flüssigkeit gelöst oder als nasses System vorliegen. Dies betrifft Systeme wie Suspensionen, Emulsionen oder Gele. Die Nassdispergierung ist wesentlich einfacher als die Trockendispergierung, da die Haftkräfte zwischen den Partikeln in einer Flüssigkeit deutlich geringer sind. Dadurch lassen sich die Partikel mit deutlich weniger Energieaufwand voneinander trennen und gleichmäßig verteilen.
Dieses Verfahren kommt insbesondere dann zum Einsatz, wenn die Stoffe eine starke Neigung zur Agglomeration aufweisen, also dazu, Klumpen oder Aggregate zu bilden. Das Dispergieren in Flüssigkeit reduziert die Gefahr solcher Verklumpungen und ermöglicht eine gleichmäßigere Verteilung der Teilchen.
Allerdings hat die Nassdispergierung auch einen entscheidenden Nachteil: Wenn das Endprodukt ein Feststoff oder eine Mischung mit Feststoffen ist, kann ein zusätzlicher Prozessschritt nötig sein. Ein Beispiel wäre das Dispergieren eines Pulvers in einer Flüssigkeit, um es anschließend wieder mit einem festen Trägermaterial zu vermischen. Dieser zusätzliche Schritt erhöht den Aufwand und kann die Produktentwicklung komplizierter gestalten.
Komplettieren des Dispergiergutes
Beim Dispergieren ist das Komplettieren des Dispergiergutes ein wichtiger Schritt, der nach der Dispergierung der Pigmente oder Füllstoffe erfolgt. Du fügst in diesem letzten Schritt alle übrigen Komponenten hinzu, die für das fertige System notwendig sind, wie z. B. Bindemittel, Lösungsmittel, Additive oder weitere flüssige Bestandteile.
Dabei ist besondere Vorsicht geboten, um einen sogenannten Lösemittelschock zu vermeiden. Dieser kann auftreten, wenn das Pigment durch plötzliche und unkontrollierte Zugabe von Lösungsmitteln ausfällt. Die Pigmente, die zuvor fein in der Flüssigkeit verteilt wurden, können sich durch zu schnelle Zugabe wieder zu größeren Aggregaten zusammenschließen. Dies beeinträchtigt nicht nur die optischen Eigenschaften, sondern auch die mechanischen und chemischen Eigenschaften des Endprodukts.
So vermeidest Du einen Lösemittelschock
- Langsame und gleichmäßige Zugabe: Füge die restlichen Bestandteile, insbesondere Lösungsmittel, langsam und unter ständigem Rühren hinzu. Dies hilft, das Risiko eines Pigmentausfalls zu minimieren.
- Temperaturkontrolle: Achte darauf, dass die Temperatur des Systems konstant bleibt. Temperaturschwankungen können die Wechselwirkungen zwischen den Pigmenten und dem Lösungsmittel beeinflussen und so den Dispergierprozess stören.
- Rührgeschwindigkeit anpassen: Wähle eine passende Rührgeschwindigkeit, die stark genug ist, um eine gleichmäßige Verteilung zu gewährleisten, aber sanft genug, um Scherkräfte zu vermeiden, die zu unerwünschten Reaktionen führen könnten.
Diese Vorsichtsmaßnahmen sind entscheidend, um ein homogenes Endprodukt zu erzielen und sicherzustellen, dass alle Komponenten im Lack oder in der Dispersion stabil bleiben. Ein sauber durchgeführtes Komplettieren des Dispergiergutes ist daher für die Qualität des Endprodukts essenziell.
FAQ über Dispergieren
Kann in Wasser dispergiert werden?
Ja, viele Stoffe können in Wasser dispergiert werden. Wasser dient häufig als Dispersionsmittel (oder auch Dispergens) für die Verteilung von Feststoffen oder Flüssigkeiten in einer kontinuierlichen Phase. Damit das Dispergieren in Wasser effizient ist, müssen Dispergiermittel hinzugefügt werden, die die Partikelstabilität erhöhen und eine gleichmäßige Verteilung ermöglichen.
Was sind Dispergiermittel?
Dispergiermittel sind Additive, die helfen, Partikel gleichmäßig in einem flüssigen Medium zu verteilen. Sie verhindern das Verklumpen (Agglomeration) der Partikel und verbessern die Stabilität der Dispersion. Dispergiermittel kommen in verschiedenen Industrien zum Einsatz, z. B. in der Farben- und Lackherstellung oder bei der Produktion von Nanopartikeln.
Was ist der Doughnut-Effekt beim Dissolver?

Der Doughnut-Effekt beschreibt ein spezifisches Fließmuster, das während des Dispergierprozesses um die rotierende Zahnscheibe des Dissolvers entsteht. Diese Struktur ist ein Indikator dafür, dass die Energie optimal auf das zu dispergierende Material übertragen wird. Ein erfolgreicher Doughnut-Effekt signalisiert, dass die Partikel effizient zerkleinert und verteilt werden.
Wichtige Faktoren für den Doughnut-Effekt:
- Der Durchmesser der Zahnscheibe im Verhältnis zum Behälterdurchmesser
- Die Höhe der Zahnscheibe über dem Behälterboden
- Die Einfüllhöhe des Materials
- Die Umfangsgeschwindigkeit der Zahnscheibe (mindestens 20 m/s)
Bei einer zu niedrigen Geschwindigkeit wird das Material lediglich gerührt, und kein Doughnut-Effekt tritt auf. Eine zu geringe Viskosität führt dazu, dass der Ansatz schäumt und spritzt, während bei zu hoher Viskosität das Material stockt und nicht mehr alle Pigmente die Zahnscheibe erreichen.
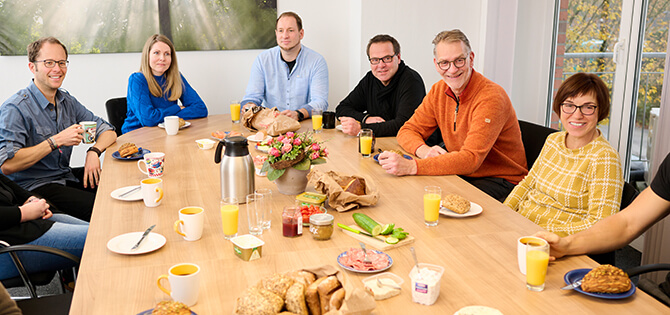
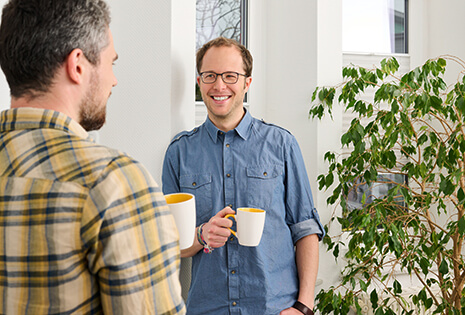
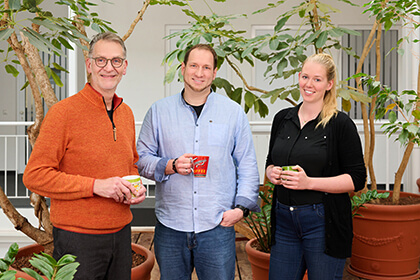
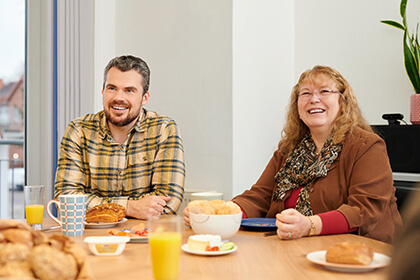
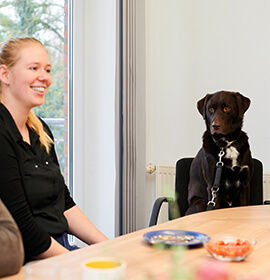
Bist Du Ingenieur*in oder Konstrukteur*in und suchst neue Herausforderungen? Bei uns erwarten Dich ein familiäres Umfeld und spannende Aufgaben!
Jetzt Stellenanzeigen ansehen!